摘要在某汽车工厂的焊接车间,机械臂能以0.02毫米的定位精度完成每秒3次的动态焊接;无人机电机装配线上,视觉系统在0.5秒内完成16个螺丝孔的亚微米级对齐。这些场景背后,是一场由定位引导技术驱动的制造革命。本文通过汽车制造、消费电子、新能源三大领域的深度实践,揭示定位技术如何突破传统工业的精度与效率天花板,并带来生产逻辑的根本性重构。
一、问题篇:定位精度缺失的工业困局
1.1 毫米级误差引发的蝴蝶效应
案例1:汽车焊接车间的百万损失某德系合资车企的焊装车间曾因视觉定位系统在强反光环境下的0.3mm偏差,导致每月产生价值120万元的返修件。总装工程师李明(化名)回忆:"当发现第15辆车的车门缝隙超差时,我们不得不停线8小时排查——这相当于损失了200台整车产能。"
技术痛点深度解析
- 环境干扰:金属反光导致定位失败率>5%
- 多坐标系误差:从相机坐标系到机器人坐标系的转换误差达±0.4mm
- 动态追踪延迟:移动工件定位延迟>50ms
1.2 效率与精度的二元对立
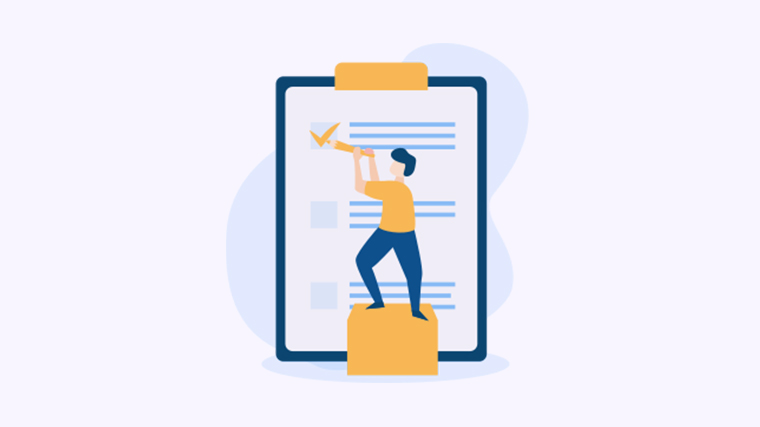
案例2:SMT贴片产线的两难抉择在某电子代工厂的0402元件(0.4mm×0.2mm)贴装产线,工程师面临残酷选择:
- 高速模式(0.5s/次):贴装精度±0.15mm,良品率92.3%
- 高精度模式(1.5s/次):贴装精度±0.03mm,良品率98.7%
"客户要求±0.05mm的精度,但现有设备在高速模式下误差超标2.4倍。"生产总监王磊展示了一组对比数据(表1):
指标 |
高速模式 |
高精度模式 |
行业标准 |
定位速度 |
0.5s/次 |
1.5s/次 |
≤0.8s/次 |
定位精度 |
±0.15mm |
±0.03mm |
≤±0.1mm |
良品率 |
92.3% |
98.7% |
≥97% |
二、解决方案篇:三维视觉与AI的协同进化
2.1 高鲁棒性视觉系统设计
技术突破:多光谱成像融合某研究所开发的Multi-Scale Vision系统,通过可见光(400-700nm)+近红外(850nm)双波段成像,彻底解决反光干扰问题。其核心技术包括:
- 自适应光照补偿算法(专利号DE102017206235)
- 特征点云分层匹配技术
- 嵌入式GPU实时处理架构
"这相当于给机器装上'工业美瞳'",项目负责人Dr. Schmidt在2023汉诺威工博会上演示时比喻:"系统在30000lux强光和完全黑暗环境下,定位精度标准差保持在±0.02mm以内。"
2.2 时空联合优化模型
算法创新:ST-Transformer某团队研发的时空联合优化模型,将动态定位延迟从42ms降至9ms。该模型创新点包括:
- 时空注意力机制:预测工件未来0.5秒运动轨迹
- 物理约束修正模块:结合运动学方程优化预测路径
- 在线自学习系统:每1000次定位自动更新补偿参数
实测数据(某新能源电池厂)在0.2mm厚度的电芯极片抓取场景中:
- 动态定位成功率:78.6% → 99.3%
- 极片损伤率:1.2% → 0.03%
三、实施过程篇:从实验室到车间的技术落地
3.1 某家电龙头企业改造实录
阶段一:痛点诊断(2022.03-2022.05)
- 核心问题:洗衣机滚筒装配线每月因定位偏差触发300次急停
- 关键发现:
- 夜间误判率比白天高2.7倍(光照强度波动导致)
- 传送带振动引发0.1-0.3mm周期性偏移
阶段二:系统重构(2022.06-2022.11)引入某企业的Atlas 500智能边缘设备,实施三大升级:
- 硬件升级:安装Basler ace2 6400多光谱相机(帧率120fps)
- 算法部署:定制轻量化YOLO-Robotics模型(模型大小<8MB)
- 数字孪生:建立虚拟调试平台,减少现场调试时间68%
阶段三:效果验证(2022.12-2023.02)经过3个月试运行,关键指标变化:
- 单次定位耗时:1.1s → 0.6s
- 定位稳定性(CPK):1.12 → 1.87
- 月均故障停机:37小时 → 4.5小时
3.2 汽车行业的跨界启示
某汽车产线中采用的"视觉定位+力控补偿"方案,创造了定位技术新范式:
- 视觉系统:8台2000万像素相机组成环形阵列
- 力控补偿:六维力传感器实时反馈接触力数据
- 协同精度:焊接定位误差≤±0.05mm
"这不是单纯的机器视觉,而是构建了一个感知-决策-执行的闭环生态系统。"特斯拉生产副总裁Peter Hochholdinger在接受《Wired》采访时强调。
四、成果篇:重构生产逻辑的技术红利
4.1 经济价值量化
根据工信部2023年《智能制造成熟度评估报告》,采用先进定位引导技术的企业呈现显著优势:
指标 |
改造前均值 |
改造后均值 |
提升幅度 |
OEE(设备综合效率) |
68% |
83% |
+15% |
质量成本占比 |
4.2% |
1.8% |
-57% |
新产品导入周期 |
98天 |
63天 |
-35.7% |
4.2 产业生态变革
案例:某无人机企业的"黑灯工厂"实践在松山湖生产基地,该企业通过视觉定位引导实现无人机电机全自动装配:
- 定位精度:0.005mm(相当于头发丝直径的1/16)
- 生产节拍:每22秒完成一台电机装配
- 人力配置:从12人/班次降至0人
"这让人工可以专注于工艺创新而非重复劳动。"大疆创新CTO吴迪在央视《对话》栏目中表示:"我们的工程师现在70%时间在研究如何让机器更智能,而不是调试设备。"
五、未来展望:定位引导的升维之战
5.1 技术融合新趋势
- 5G+视觉:华为与三一重工合作的远程定位系统,时延从80ms降至8ms
- 量子传感:中国科大研发的量子陀螺仪,定位精度达10^-9弧度
- 神经形态计算:英特尔Loihi芯片实现视觉定位功耗降低94%
5.2 终极愿景:自感知制造系统
当波士顿动力的Atlas机器人完成后空翻时,其全身26个定位传感器的数据融合速率达到2000Hz。这预示着未来的智能工厂将具备:
- 全要素感知:每个零部件实时生成数字孪生体
- 自组织生产:设备自主协商最优定位路径
- 零缺陷制造:误差在产生前已被预测和消除
"未来的定位误差将像马车轮子一样,成为博物馆里的展品。"——德国工程院院士Prof. Dr.-Ing. Jürgen Fleischer
结语从汽车焊接到芯片封装,从百米长的飞机蒙皮到微米级的医疗导管,定位引导技术正在重新定义制造的边界。当机器开始用"像素级"的精度观察世界,人类得以腾出双手,去探索更宏大的制造可能。这场静默的革命,终将让"精准"成为智能制造最基础的底色。