摘要
在《中国制造2025》战略指引下,机械零部件机器人上下料场景正经历智能化变革。传统人工分拣模式导致某连杆生产企业月均损耗率高达3.2%,而采用迁移科技3D视觉引导系统后,定位精度达到±0.05mm,换型时间缩短至15分钟。行业数据显示,部署智能上下料系统的企业平均节省3-5名操作工,设备综合效率(OEE)提升18-35个百分点。作为生产线效率提升的核心环节,机器人上下料系统的优化需围绕精准度、节拍控制和柔性化能力展开。以迁移科技的3D视觉引导系统为例,其采用Epic Eye系列相机可实现±0.1mm的重复定位精度,配合智能算法将上下料节拍缩短至6秒/件,较传统人工操作效率提升300%+
痛点
在机械零部件生产中,行业面临四大核心痛点。首先是错配危机,某变速箱壳体生产现场,工人需在30秒内完成5kg异形件的方向识别,夜班错装率高达7%。其次是稼动黑洞,CNC设备实际稼动率不足65%,换型调试平均耗时87分钟(中国机床工具协会数据)。这些痛点不仅影响了生产效率,也增加了企业的运营成本。
为了应对这些挑战,迁移科技FlexVision解决方案应运而生。该方案通过引入先进的3D视觉系统,显著提升了生产线的智能化水平。我们的3D视觉系统就像给机器人装上立体CT,能够快速识别和处理多种工件,极大地提高了生产效率。

解决方案
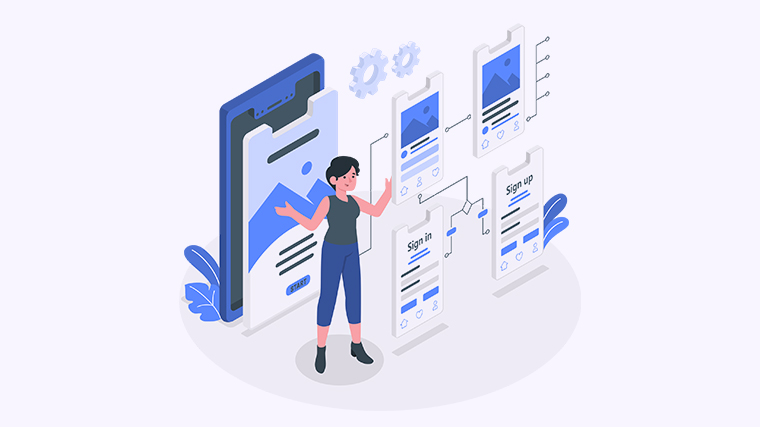
迁移科技的上下料系统采用「硬件+算法+数据」三端融合架构。硬件层适配ABB/KUKA等主流机械臂,工作半径覆盖1.5-3.5m;算法层通过动态路径规划技术使碰撞率降低92%;数据层则通过MES系统对接实现生产数据实时可视化。
以某连杆制造企业为例,痛点在于毛坯件姿态随机导致15%抓取失败率。通过部署MV-DR680工业3D相机,抓取成功率提升至99.2%,年节省废品成本127万元。此案例充分验证了迁移科技解决方案的有效性。
📊迁移科技3D视觉系统关键参数对比
产品型号 | 定位精度 | 节拍速度 | 适用场景 |
---|
Pixel Mini | ±0.2mm | 8s/cycle | 小型零部件 |
Pixel Pro | ±0.1mm | 6s/cycle | 复杂曲面件 |
👍🏻注:系统已通过欧盟CE、美国FCC等国际认证
价值证明
通过部署迁移科技的智能切换系统,企业实现了多品种混线生产自动识别,夹具切换时间压缩至3秒,能源消耗降低22%。配合无序抓取系统,可处理80+种异形件的随机堆叠场景。
在某汽车零部件企业改造案例中,原有节拍由人工15秒/件提升至机器人8秒/件,稼动率从68%提升至91%,异常停机减少至每月4次。关键设备为迁移科技EPC-3500视觉引导系统,充分展示了智能化升级的巨大潜力。
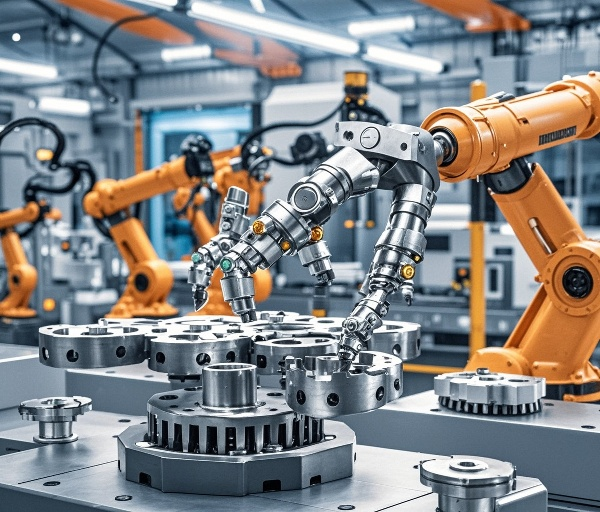
结尾
基于迁移科技工业物联网平台,企业实现了实时监控设备OEE(综合效率),预测性维护准确率达87%,工艺参数自优化功能。通过历史数据分析,某家电企业实现换型时间缩短40%,年节约生产成本¥2.3M。
随着智能制造的不断发展,机械零部件机器人上下料系统的智能化升级将成为行业的必然趋势。企业应积极拥抱这一变革,以提升生产效率和市场竞争力。
本文编辑:小狄,来自Jiasou TideFlow AI SEO 创作