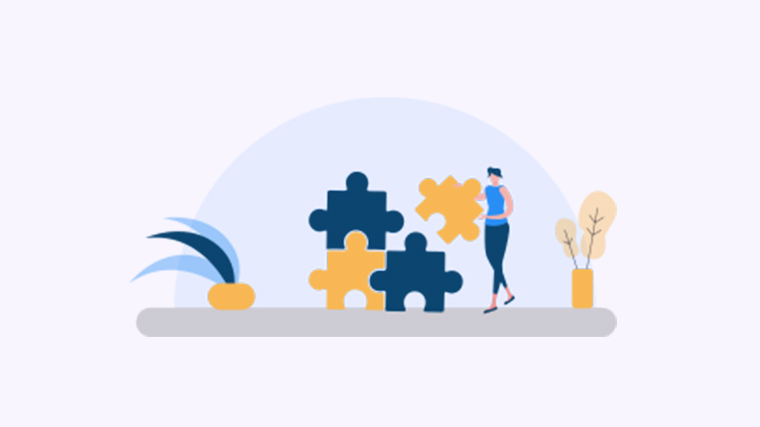
编者语:MES系统是介于ERP和自控系统(DCS、PLC等)之间的系统,是管控一体化的桥梁,对于已经实现ERP系统的企业来说,缺少MES系统就相当于在计划与过程控制间形成了“断层”。MES属于与生产过程连接的企业信息系统,是实现企业综合自动化的关键环节。
传统的MES(Traditional MES,T-MES)是指在第一阶段上发展起来的信息系统。T-MES从70年代的零星车间级应用发展到复杂的具有一定集成能力的大系统,并占据了一定的市场份额。可以简单地将T-MES分为两大类:①专用的MES系统(Point MES)。这类系统是自成一体的应用系统,它只解决某个特定的领域间题,如车间维护、生产监控、有限能力调度或是SCADA等;②集成的MES系统(Integrated MES)。该类系统起初是针对一个特定的、规范化的环境而设计的,如航空、装配、半导体、食品和卫生等行业,目前已拓展到整个工业领域。在功能上它已实现了与上层事务处理和下层实时控制系统的集成,但此类系统依然是针对一个特定的行业,缺少通用性和广泛的集成能力。
由于T-MES系统是基于预先设定的程式进行系统开发的,因此,开发此类系统成本高、效率低,并隐含着较大的风险。如过程有徽小变化,就可能导致系统不能正常运转,系统的稳定性差。具体表现在以下五个方面:
通用性差。目前市场上的T-MES系统,无论其功能多么复杂,均是针对特定的行业、特定的领域问题开发的。由于没有一定的技术规范指导,针对不同行业的MES功能基本上无法借鉴和使用,因而使得系统的开发周期长、投资大,限制了MES市场的快速发展。
可集成性弱。从技术发展角度和用户需求来看,软件结构本身应能与其它应用系统集成,做到相箱相成,相得益彰。不仅提高了企业遗产系统(legacy system)的生命周期,降低对信息系统的投入。同时,也为用户选择较为合适的各种软件提供了更大的空间。目前,某些具有集成功能的MES,虽能实现与上层事务处理和下层控制系统的集成,但也仅仅局限于某个特定的系统或功能,使得用户在选择MES产品时受到很大的制约,限制了MES软件产品的推广。
缺乏互操作性。互操作性是系统敏捷性的一个重要标志。企业采用的数据库、操作系统是异构的,在分布式生产环境下,需要从不同的MES系统中裁剪不同的功能,以满足某个特定任务的需要,实现互操作。目前T-MES墓本上没有此类功能。
重构能力差。重构能力是指系统具有随业务过程的变化进行功能配置和动态改变的能力。不同的行业、不同的企业其生产组织模式不尽相同,信息系统必须具有可重构能力,即根据不同的需求搭建相应的系统。
敏捷性差。敏捷性是所有先进制造模式的核心。在生产中表现为对市场的快速响应和对实际生产环境的应变能力,在信息系统中表现为系统的可重构、可重用和可扩展(3R特性)。对于T-MES,由于系统结构本身和采用的开发技术,一个微小的过程改变,系统就会无所适从,甚至不能正常运转。尽管如此T-MES在市场占有率1995年达到10亿美元,预计1999年达到35亿美元。
随着信息技术的发展和市场竞争的加剧,具有高度敏捷性的制造执行系统日益成为市场的热点,国际MES协会的成立为可集成MES系统的研究与开发提供了技术保证。
相关阅读: 以工业软件MES支撑“两化融合”的实现 第八届MES开发与应用专题研讨会召开
Gkong小贴士:什么是MES系统?
MES(英文Manufacturing Execution System的缩写),即生产执行系统,是近几年发展起来的企业信息化系统,目前在发达国家已经普遍推广。 MES是介于ERP(企业资源计划系统)和自控系统(DCS、PLC等)之间的系统,是管控一体化的桥梁,对于已经实现ERP系统的企业来说,缺少MES系统就相当于在计划与过程控制间形成了“断层”。MES属于与生产过程连接的企业信息系统,是实现企业综合自动化的关键环节。 生产执行系统通过控制包括物料、设备、人员、流程指令和设施在内的所有工厂资源来提高制造竞争力,确保整个生产行为的最优。生产信息管理系统主要作用是,一方面,实时收集和传递生产数据,通过设计的功能(程序)提供给所有需要的管理者,使他们能迅速知晓生产的变化,对生产进行有针对性的调控,实现对生产有效控制; 另一方面,通过对生产数据的分析,找出规律,改进生产组织和管理的方法,优化生产管理体系。 制造执行系统协会MESA定义的MES共有11个功能模块,但由于离散制造企业(如机械制造、电子电器、航空制造、汽车制造等行业)和流程生产行业(如化工、制药、石油化工、电力、钢铁制造、能源、水泥等)的生产模式、管理模式以及自动控制水平之间存在较大的差异,所以在不同的行业MES系统存在较大的差异,并且同一行业的不同企业之间其需求也存在差异,所以并不是一个MES产品就可以包打天下,而是需要根据不同行业和不同企业的需求状况进行针对性的开发。对于化工、冶金等流程工业,将各种不同的自控系统联网,自动采集生产过程的数据实现企业的生产信息集成,建立全厂范围的实时和历史数据库,是企业实现MES应用最关键、最核心、也是最基础的任务。