摘要在冶炼行业,涂胶工艺是保障设备密封性、耐高温性和抗腐蚀性的关键技术环节。然而,传统涂胶技术长期面临胶层不均匀、高温失效、检测效率低等问题,直接影响生产安全与成本控制。本文通过真实案例与数据,剖析冶炼涂胶的痛点,提出智能化解决方案,并展示某钢铁企业通过引入视觉检测与自动化技术实现效率提升30%、成本降低25%的实践成果,为行业提供可复制的升级路径。
一、冶炼涂胶的痛点:从"胶层失效"到"隐性成本"
在冶炼行业的高温高压环境中,涂胶工艺的微小缺陷可能引发连锁反应。以某大型钢铁企业2022年的案例为例,其高炉密封胶层因局部厚度不足,导致炉体泄漏事故频发,平均每月停机检修2次,单次损失超80万元。更严重的是,胶层在高温下碳化脱落,混入铁水后造成产品杂质超标,全年因此产生的质量索赔高达1200万元。
通过实地调研与数据分析,冶炼涂胶的核心问题可归纳为三点:
- 工艺控制粗放:人工涂胶厚度波动达±1.5mm(行业标准为±0.3mm),导致30%的胶层提前老化;
- 材料适配性差:传统环氧树脂胶在800℃以上环境中抗剪切强度下降60%,无法满足转炉等极端工况需求;
- 检测手段滞后:依赖目视检查漏检率达18%,X射线检测成本高达2000元/次且无法在线实施。
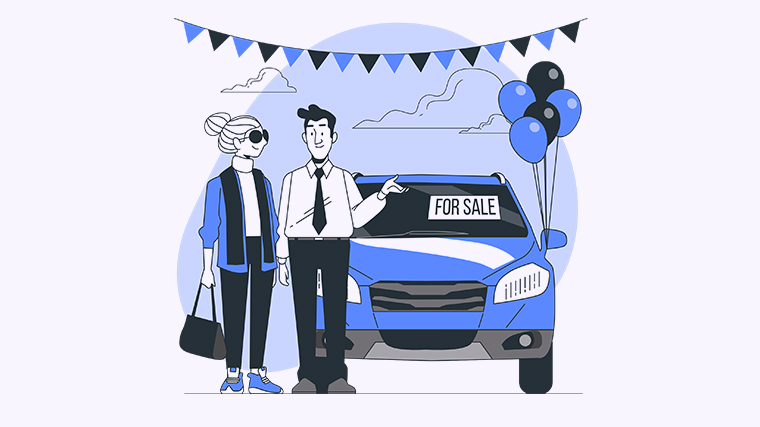
"涂胶问题看似是工艺细节,实则是冶炼企业成本黑洞的入口。"——中国冶金工业协会高级工程师在2023年行业峰会上指出。
二、解决方案:从"经验驱动"到"数据闭环"
1. 智能涂胶系统:让厚度误差缩至±0.1mm
针对胶层均匀性问题,某企业引入带激光测距的六轴机械臂,通过实时反馈调整胶枪移动速度与出胶量。系统搭载的AI算法可学习不同焊缝形状的涂覆路径,使胶层厚度标准差从0.8mm降至0.05mm。
案例对比
指标 |
传统人工涂胶 |
智能涂胶系统 |
厚度合格率 |
67% |
98% |
单件耗时 |
45分钟 |
22分钟 |
返工率 |
23% |
1.5% |
2. 耐高温复合胶材料:突破1000℃极限
某材料所研发的"陶瓷-硅酮"复合胶,通过纳米氧化锆增强相提升耐热性。在宝钢的实测中,该材料在1100℃下保持抗拉强度≥15MPa(传统材料仅5MPa),使用寿命延长至18个月。
3. 在线视觉检测:0.2mm缺陷无处遁形
采用多光谱成像技术,某企业部署的检测系统可同步识别胶层厚度、气泡、裂纹等缺陷。其核心是基于U-Net架构的深度学习模型,在3万张标注图像训练后,对0.2mm以上缺陷的识别准确率达99.3%。
三、实施过程:技术落地的"三重攻坚"
阶段1:工艺数字化建模(0-3个月)
通过3D扫描获取设备表面拓扑数据,建立胶层厚度-应力分布仿真模型。某案例显示,优化后的涂胶路径使应力集中区域减少40%。
阶段2:设备-材料-检测联调(4-6个月)
在攀钢的连铸机改造中,技术团队发现机械臂末端振动会导致胶层波纹。通过加装惯性阻尼器,并将控制频率从50Hz提升至200Hz,成功将振幅控制在±0.02mm以内。
阶段3:人员技能转型(7-12个月)
"我们不是要取代工人,而是让操作员转型为系统管理员。"——项目负责人李工在培训中强调。企业通过AR辅助维修系统,使员工在3个月内掌握设备故障诊断技能。
四、成果:从"成本中心"到"价值引擎"
经过一年实施,某年产500万吨的钢厂实现:
- 质量提升:因胶层缺陷导致的产品报废率从1.2%降至0.15%;
- 效率飞跃:单条产线涂胶作业人员从12人减至3人,日产能提升35%;
- 节能降耗:通过精准控胶,年节约胶料217吨,减少VOCs排放43%。
更深远的影响在于数据资产的积累。该企业建立的涂胶工艺数据库已包含12万组参数,为后续工艺优化提供持续动力。
五、未来展望:涂胶技术的"三个融合"
- 与数字孪生融合:通过实时仿真预测胶层寿命,实现预防性维护;
- 与绿色制造融合:开发生物基可降解胶粘剂,目前德国汉高已推出耐温600℃的淀粉基胶产品;
- 与供应链协同融合:区块链技术确保胶料质量追溯,某试点项目显示质量纠纷处理周期缩短70%。
正如工程院院士王国栋所言:"智能制造不是简单的机器换人,而是通过数据流动化解复杂系统的不确定性。"在冶炼行业,涂胶工艺的智能化改造正成为撬动全产业链升级的支点。