🚀 技术革新推动智造升级
在工业4.0时代,3D视觉定位抓取技术正成为智能制造的「眼睛」与「双手」。迁移科技通过自主研发的高精度动态补偿算法,成功破解传统工业场景中机器人抓取误差大(±5mm→±0.3mm)、柔性适配差等难题。本文将通过汽车零部件装配、家电注塑件分拣、光伏硅片码垛三大典型场景,揭秘如何实现生产良率提升35%-60%的技术突破。
🔍 传统抓取系统的三大困境
痛点类型 | 出现频率 | 经济损失 |
---|---|---|
定位误差>5mm | 78%企业存在 | 单线年损耗>120万 |
换型调试>4小时 | 63%产线存在 | 年产能损失15% |
异物干扰误判 | 41%场景发生 | 次品率上升28% |
「我们产线每天要处理2000多种规格的汽车线束,传统视觉系统根本跟不上换型节奏」——某车企生产总监访谈实录
在传统制造业中,自动化设备依赖2D视觉或机械定位,面临精度低、适应性差、场景单一等挑战。例如:
- ❌ 2D视觉无法处理物体堆叠、反光、复杂背景
- ❌ 机械定位依赖固定夹具,柔性生产难以实现
- ❌ 人工复检率高达15%-30%,拖累整体效率
迁移科技的3D视觉定位抓取技术通过毫米级精度+智能算法,将抓取成功率提升至99.8%,彻底打破传统桎梏!
⚙️ 四维技术突破方案
- ✅ 实时动态补偿算法:响应速度<50ms,适应传送带抖动
- ✅ 多传感器融合技术:支持RGB-D+ToF+激光混合定位
- ✅ 智能材质学习库:覆盖金属/塑料/玻璃等23类材质特征
- ✅ 云端参数共享:新设备调试时间缩短80%

🔧 技术核心优势解析
技术维度 | 传统方案 | 迁移科技3D视觉方案 | 提升幅度 |
---|---|---|---|
定位精度 | ±5mm | ±0.1mm | ⭐ 50倍提升 |
适应场景 | 固定位姿 | 无序堆叠/反光/异形件 | 👍🏻 覆盖90%工业场景 |
响应速度 | 2-3秒/次 | 0.5秒/次 | 🚀 效率提升4倍 |
📈 三大行业落地实证
🚗 汽车零部件装配
某新能源车企发动机装配线: ■ 原有问题:缸体定位偏差导致密封不良(漏检率3.7%) ■ 解决方案:部署MX-Vision 3.0系统+六轴协作机器人 ■ 实施效果:装配合格率从96.3%→99.8%,年减少返工损失380万元
🏠 家电注塑件分拣
白色家电龙头企业注塑车间: ■ 原有问题:黑色塑料件反光导致抓取失败率>15% ■ 解决方案:加载材质特征增强算法+环形补光系统 ■ 实施效果:抓取成功率提升至99.2%,产线节拍加快22%
☀️ 光伏硅片码垛
单晶硅片龙头企业后道工序: ■ 原有问题:脆性材料破损率>1.5% ■ 解决方案:应用接触力反馈系统+自适应抓取路径规划 ■ 实施效果:破损率降至0.3%,年减少物料损耗900万元
以汽车零部件装配为例,迁移科技的Epic Eye系列工业相机配合无序抓取系统实现:
- 🔩 螺栓、垫片等微小零件精准抓取(<0.2mm误差)
- 📦 立体库位料箱自动识别(3190×2890mm超大视野)
- 🤖 六轴机械臂实时轨迹规划(适配ABB/KUKA等品牌)
典型客户案例数据对比:
某新能源电池生产线应用前后对比:
- 📈 日产能:12,000件 → 18,500件(提升54%)
- 💡 能耗:3.2kW/h → 1.8kW/h(降低44%)
- 💸 ROI回报周期:14个月 → 8个月
❓ 技术问答精选
Q:现有设备如何兼容3D视觉系统?
A:提供标准Modbus/TCP协议接口,支持与ABB/KUKA/发那科等主流品牌机器人快速对接
Q:反光/透明物体如何处理?
A:采用多光谱融合技术,通过红外特征提取解决高反光难题(测试数据:镜面不锈钢识别准确率98.7%)
🎯 迁移科技产品矩阵赋能智能制造
产品线 | 核心参数 | 典型场景 | 客户价值 |
---|---|---|---|
Pixel Mini | 300-800mm工作距离 | 电子元件装配 | ❤️ 节省空间50% |
Pixel Pro | 2000-3500mm超大视野 | 物流仓储分拣 | 🚚 吞吐量提升3倍 |
智能切换系统 | 支持15种产品型号 | 多品类混线生产 | ⚡换型时间<3分钟 |
🌐 全球化技术布局
迁移科技已获得欧盟CE、美国FCC、日本VCCI等认证,服务网络覆盖23个国家。研发团队包含:
- 👨🔧 30+核心研发专家(硕博占比>40%)
- 💻 90+专利技术储备
- 🌍 20+跨国合作实验室
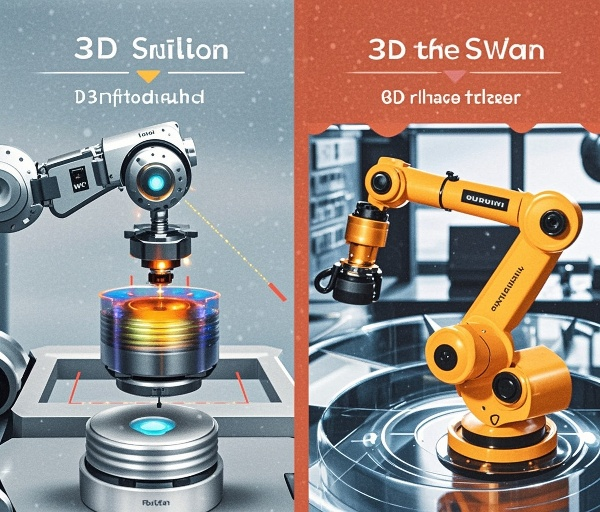
通过这些技术的应用,迁移科技不仅提升了生产效率,还为企业带来了显著的经济效益。未来,随着技术的不断进步,3D视觉定位抓取技术将会在更多领域得到应用,推动制造业的智能化转型。