在工业发展的长河中,工业零件检测技术不断演进,从最初的人工检测,逐步发展到如今的三维检测技术,每一次变革都极大地推动了工业生产的进步。
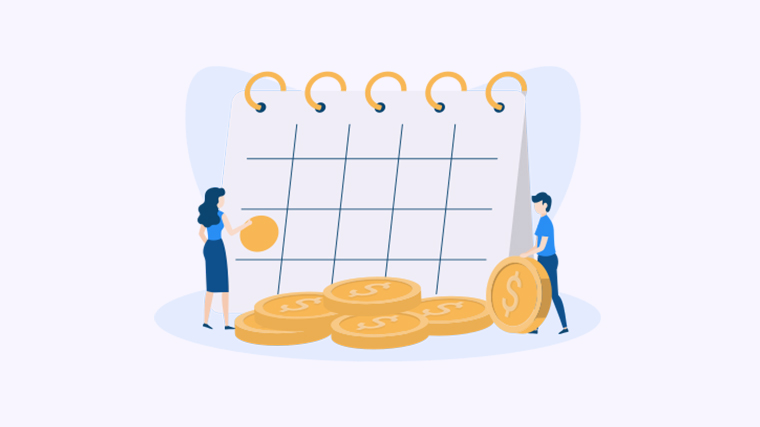
早期,工业零件检测主要依赖人工,质检员凭借肉眼和简单工具,如卡尺、千分尺等,对零件的尺寸、形状和表面质量进行判断。这种方式虽然灵活,但受人为因素影响极大,检测效率低、精度有限,且易出现漏检、误检。随着工业自动化的发展,传统机器视觉检测技术应运而生。它利用相机和图像处理算法,对零件的二维图像进行分析,能够快速检测出一些简单的尺寸和表面缺陷,在一定程度上提高了检测效率和准确性。然而,对于复杂形状的零件和需要精确测量三维尺寸的场景,传统机器视觉检测就显得力不从心。
为了突破这些局限,三维检测技术应运而生。它通过获取零件的三维数据,能够对零件进行全方位、高精度的检测。近年来,随着计算机技术、光学技术和传感器技术的飞速发展,三维检测技术不断革新,在工业生产中的应用越来越广泛,成为保障产品质量和推动工业智能化升级的关键力量。
三维检测技术大揭秘
(一)技术原理全解析
三维扫描检测技术,是工业零件检测领域的核心技术,其原理基于光学、激光或其他物理测量原理,能够获取工业零件的三维数据。以常见的结构光三维扫描技术为例,它通过投影仪向零件表面投射特定图案,如条纹、格雷码等,同时利用相机从不同角度拍摄零件表面图案的变形情况。根据三角测量原理,通过计算投影仪、相机与零件表面点之间的几何关系,就能精确获取零件表面各点的三维坐标,从而构建出零件的三维模型 。
获取三维数据后,检测系统会将其与零件的原始设计数据(通常以 CAD 模型形式存在)进行比对。通过特定的算法,计算出实际三维模型与 CAD 模型在各个维度上的尺寸偏差,从而检测出零件是否存在尺寸超差、形状偏差等问题。比如在汽车发动机缸体的生产中,利用三维扫描技术获取缸体的实际三维数据,与设计数据比对后,能够精确检测出缸筒内径、缸体平面度等关键尺寸是否符合设计要求。
(二)实现过程分步看
- 三维扫描:使用三维扫描设备,如手持式激光扫描仪、固定式结构光扫描仪等,对工业零件进行全方位扫描。在扫描过程中,需要根据零件的形状、尺寸和表面特性,合理设置扫描参数,如扫描分辨率、扫描角度、曝光时间等。对于复杂形状的零件,可能还需要进行多次扫描,并通过拼接算法将不同角度的扫描数据整合为一个完整的三维模型。例如,在航空发动机叶片的检测中,由于叶片形状复杂且尺寸精度要求高,通常会采用高精度的蓝光三维扫描仪,以确保获取叶片表面的细微特征和精确的三维数据。
- 数据处理:扫描得到的原始数据往往包含噪声、冗余信息和一些由于扫描盲区或遮挡导致的缺失数据。因此,需要对数据进行去噪、平滑、精简和填补缺失等处理。去噪可以通过滤波算法实现,如高斯滤波、双边滤波等,去除因环境干扰、设备误差等产生的噪声点;平滑处理则可以使数据表面更加光滑,减少数据波动;数据精简可以在不影响关键特征的前提下,减少数据量,提高后续处理效率;对于缺失数据,可采用基于曲面拟合、插值等方法进行填补,以保证数据的完整性,为后续的精确比对提供可靠的数据基础。
- 数据比对:将处理后的三维数据导入专业的检测分析软件,与原始 CAD 模型进行精确比对。比对过程中,软件会根据预设的公差范围,计算实际零件与设计模型在各个尺寸、形状特征上的偏差值,并以直观的方式展示出来,如色谱图、偏差表格等。色谱图中,不同颜色代表不同的偏差范围,绿色表示在公差范围内,红色表示偏差超出允许范围,通过这种可视化方式,能够快速、直观地了解零件的整体质量状况,定位存在问题的区域。
- 结果分析:根据比对结果,进行全面的误差分析和原因分析。通过统计分析误差数据,判断零件的制造工艺是否稳定,评估产品质量的一致性。对于超差的零件,深入分析其产生原因,如加工设备精度问题、刀具磨损、工艺参数不合理等。例如,如果发现一批零件在某个特定尺寸上都存在较大偏差,且偏差方向一致,就需要检查对应的加工工序和设备参数,找出问题根源。根据分析结果,给出针对性的质量评估报告和改进建议,为生产部门调整工艺、改进生产提供有力依据 。
步骤
|
具体内容
|
操作要点
|
三维扫描
|
使用三维扫描设备获取工业零件三维数据
|
根据零件特性设置扫描参数,对复杂零件多次扫描并拼接数据
|
数据处理
|
对扫描数据进行去噪、平滑、精简、填补缺失等处理
|
选择合适的算法和工具,保证数据质量
|
数据比对
|
将处理后的数据与原始 CAD 模型比对
|
利用专业软件,设置合理公差范围,以直观方式展示偏差
|
结果分析
|
根据比对结果进行误差、原因分析,得出质量评估和改进建议
|
运用统计分析方法,深入分析超差原因,提出针对性建议
|
优势尽显:三维检测 VS 传统检测
与传统检测技术相比,三维检测技术在多个关键维度展现出显著优势,这些优势使其成为现代工业生产中不可或缺的质量保障手段。下面通过表格形式,从检测精度、效率、人为因素干扰、对复杂零件检测能力等方面进行详细对比 :
对比项目
|
传统检测
|
三维检测
|
检测精度
|
较低,难以检测微小细节和形状变化
|
高精度,误差在几微米以内
|
检测效率
|
操作繁琐、检测时间长
|
快速完成大量数据处理和比对,检测时间短
|
人为因素干扰
|
易受人为因素影响,如视觉误差导致漏检或误判
|
减少人为因素干扰,可靠性高
|
对复杂零件检测能力
|
对复杂曲面零件检测困难
|
可对复杂形状和不规则表面零件进行有效检测
|
从检测精度上看,传统检测方法使用的卡尺、千分尺等工具,精度一般在 0.01 毫米左右,对于一些高精度零件,如航空发动机叶片、精密模具等,其公差要求常控制在微米级,传统检测难以满足。而三维检测技术,借助高精度传感器和先进算法,精度可达几微米甚至更高,能精准检测零件的微小尺寸变化和形状偏差。在检测效率方面,传统检测需要人工逐个测量零件的关键尺寸,操作繁琐,对于复杂零件,检测时间长,难以满足大规模生产的检测需求。三维检测技术则能在短时间内完成对零件的全方位扫描,快速处理大量数据,并与设计模型进行比对,大大缩短了检测周期。例如,在汽车零部件生产线上,使用三维检测系统,可在几分钟内完成对一个复杂零部件的检测,而传统检测方式可能需要几十分钟甚至更长时间 。
在人为因素干扰方面,传统检测严重依赖人工操作,检测人员的经验、疲劳程度、工作态度等因素都会影响检测结果的准确性,容易出现视觉误差,导致漏检或误判。三维检测技术实现了自动化检测,减少了人为因素的干扰,检测过程标准化、规范化,检测结果更可靠、稳定。面对复杂零件检测,传统检测手段对具有复杂曲面、不规则形状和内部结构的零件,检测难度大,甚至无法检测。三维检测技术则不受零件形状和结构的限制,无论是复杂的航空发动机叶轮,还是具有内部复杂油路的汽车发动机缸体,都能进行有效检测,获取全面、准确的三维数据 。
应用场景大放送
(一)汽车制造
在汽车制造这一庞大而复杂的产业体系中,三维检测技术贯穿于汽车生产的各个环节,从最初的设计开发,到零部件制造、整车装配的质量控制,再到售后的维修与改装,都发挥着举足轻重的作用,成为推动汽车产业高质量发展的关键力量。
在设计开发阶段,三维检测技术助力汽车企业开启创新加速键。通过对竞品车型或现有零部件进行三维扫描,获取精准的三维数据,工程师能够快速进行逆向工程分析,汲取先进设计理念,加速整车机械架构布置设计和车身造型数据的生成。这不仅大幅缩短了产品开发周期,还能在设计初期就对零部件的可制造性和装配性进行模拟验证,提前发现潜在问题并优化设计方案,降低后期设计变更成本。比如,某汽车品牌在开发一款新型 SUV 时,利用三维扫描技术对市场上同级别畅销车型进行扫描分析,结合自身品牌定位和用户需求,快速完成了新车型的外观造型设计和关键零部件的结构优化,使新车研发周期缩短了近三分之一 。
进入制造环节,三维检测技术成为保障零部件生产质量的坚固防线。在汽车零部件生产过程中,无论是发动机缸体、变速箱齿轮等关键部件,还是车门、座椅等内饰件,都需要严格控制尺寸精度和形状精度。三维检测系统能够实时、精准地获取零部件的三维尺寸数据,与设计模型进行比对,检测出零件的尺寸偏差、形状偏差以及表面缺陷等问题,确保每个零部件都符合高精度的生产标准。例如,在汽车发动机缸体的生产线上,采用在线三维检测系统,对缸筒内径、缸体平面度等关键尺寸进行实时监测,一旦发现尺寸超差,立即发出警报并追溯生产环节,及时调整工艺参数,有效降低了废品率,提高了生产效率和产品质量稳定性 。
质量控制是汽车生产的核心环节,三维检测技术凭借其高精度全尺寸检测能力,为汽车质量保驾护航。在整车装配前,对所有零部件进行三维检测,确保零部件之间的匹配精度,避免因尺寸偏差导致的装配不良问题,提高整车装配效率和质量。装配完成后,对整车进行全面的三维扫描检测,从车身外观尺寸、曲面精度到内部结构件的位置精度,进行全方位的质量评估,确保整车质量符合严格的出厂标准。通过三维检测技术,汽车企业能够及时发现并解决生产过程中的质量问题,提升产品品质和品牌形象,增强市场竞争力 。
在汽车售后维修与改装领域,三维检测技术同样大显身手。当汽车发生碰撞等事故后,通过对受损车身进行三维扫描,能够精确测量车身变形情况,为维修方案的制定提供准确的数据依据,实现精准修复,最大程度恢复车辆的原有性能和外观。对于汽车改装爱好者来说,三维检测技术可以帮助他们在改装前对车辆进行全面扫描,根据扫描数据进行个性化改装设计,确保改装后的零部件与原车完美匹配,提升改装效果和安全性 。
(二)航空航天
航空航天领域对零部件的精度和质量要求近乎苛刻,任何微小的缺陷或尺寸偏差都可能在极端工况下引发严重后果,危及飞行安全。因此,三维检测技术在航空航天领域的应用至关重要,是保障飞行器性能和安全的关键支撑技术 。
航空发动机被誉为飞机的 “心脏”,其零部件的制造精度和质量直接影响发动机的性能和可靠性。航空发动机叶片作为发动机的关键部件之一,形状复杂、尺寸精度要求极高,通常公差控制在微米级。三维检测技术能够对叶片进行高精度的三维扫描,获取叶片表面的每一个细微特征,包括叶型轮廓、叶尖间隙、前缘后缘半径等关键尺寸。通过与设计模型的精确比对,能够检测出叶片在制造过程中是否存在变形、磨损、裂纹等缺陷,以及尺寸是否符合设计要求。一旦发现问题,及时进行调整和修复,确保叶片的性能和质量。例如,某航空发动机制造企业采用蓝光三维扫描技术,对发动机叶片进行全尺寸检测,检测精度达到 ±0.01mm,有效保障了叶片的制造质量,提高了发动机的可靠性和使用寿命 。
除了发动机叶片,航空航天领域的其他零部件,如飞机机身结构件、起落架、航空电子设备外壳等,也都需要高精度的三维检测。飞机机身结构件通常由大量复杂的钣金件和连接件组成,对装配精度要求极高。三维检测技术可以在零部件制造过程中进行尺寸检测和质量控制,确保每个零部件的尺寸精度和形状精度符合设计要求,同时在装配过程中,对装配后的结构件进行三维扫描检测,验证装配精度和连接质量,保证飞机机身的整体强度和稳定性。对于航空电子设备外壳等精密零部件,三维检测技术能够检测其内部结构的尺寸精度和表面质量,确保电子设备的正常安装和运行 。
在航空航天产品的研发过程中,三维检测技术也发挥着重要作用。通过对新型零部件的三维扫描和检测,获取实际产品与设计模型之间的差异数据,为设计优化提供依据,加速产品研发进程。同时,在产品的质量追溯和故障分析中,三维检测技术能够提供准确的零部件三维数据,帮助工程师快速定位问题根源,制定解决方案,提高产品的可维护性和可靠性 。
(三)机械制造
机械制造作为工业领域的基础产业,产品种类繁多,涵盖了各类机械设备、工具、零部件等。在机械制造过程中,保证产品的尺寸精度、形状精度和表面质量是确保产品性能和可靠性的关键。三维检测技术的应用,为机械制造企业提供了高效、精准的质量检测手段,有力地推动了机械制造行业的技术升级和发展 。
在机械零件加工过程中,三维检测技术能够实时监测加工过程中的尺寸变化,及时发现加工误差并进行调整。例如,在数控机床加工复杂的机械零件时,通过在加工过程中对零件进行三维扫描,将实时扫描数据与设计模型进行比对,一旦发现尺寸偏差超出允许范围,系统可以自动调整机床的加工参数,如刀具路径、切削速度等,实现对加工过程的精确控制,保证零件的加工精度。这种实时检测和反馈控制机制,有效减少了废品率,提高了生产效率和产品质量。某机械制造企业在加工一批高精度齿轮时,采用了在线三维检测系统,将齿轮的加工废品率从原来的 5% 降低到了 1% 以内,生产效率提高了 30% 以上 。
对于机械产品的装配环节,三维检测技术同样不可或缺。机械产品通常由多个零部件装配而成,零部件之间的装配精度直接影响产品的性能和稳定性。通过对装配前的零部件进行三维检测,确保每个零部件的尺寸和形状符合设计要求,避免因零部件尺寸偏差导致的装配困难或装配质量问题。在装配过程中,利用三维检测技术对装配后的组件进行实时检测,验证装配精度和位置精度,及时发现并纠正装配过程中的错误,保证产品的装配质量。例如,在大型机械设备的装配中,如挖掘机、起重机等,通过三维检测技术对各个零部件和装配组件进行精确测量和检测,确保设备的整体装配精度和性能,提高设备的可靠性和使用寿命 。
在机械制造企业的质量管控体系中,三维检测技术提供了全面、准确的质量数据支持。通过对大量产品的三维检测数据进行统计分析,企业可以深入了解产品质量的波动情况,评估生产工艺的稳定性和可靠性,找出影响产品质量的关键因素,为持续改进生产工艺和质量控制提供依据。同时,三维检测技术生成的详细检测报告和数据记录,也为产品的质量追溯和售后服务提供了有力保障 。
未来展望:挑战与机遇并存
尽管三维检测技术在工业领域已取得显著进展,但在迈向更广泛应用和更高水平发展的道路上,仍面临着诸多挑战。
设备成本高昂是阻碍三维检测技术普及的一大关键因素。高精度的三维扫描设备,如专业的激光扫描仪、结构光扫描仪等,其价格通常在几十万元甚至上百万元,这对于许多中小企业来说,是一笔巨大的投资成本。除了设备采购费用,后期的设备维护、校准以及软件升级等,也需要持续投入资金,进一步增加了企业的运营成本负担 。
技术门槛高也是不容忽视的问题。三维检测技术涉及光学、计算机视觉、数学算法等多学科知识,对操作人员和技术研发人员的专业素质要求极高。操作人员需要熟练掌握扫描设备的操作技巧、数据处理软件的使用方法,以及具备一定的数据分析能力,才能确保检测工作的准确、高效进行。而技术研发人员则需要不断攻克技术难题,如提高扫描精度、优化数据处理算法、增强系统稳定性等,这需要大量的研发投入和专业人才支持 。
在数据安全与隐私保护方面,随着工业数字化程度的不断提高,三维检测过程中产生的大量零件三维数据,包含了企业的核心技术和商业机密。如何确保这些数据在采集、传输、存储和处理过程中的安全性,防止数据泄露、篡改和滥用,是企业面临的重要挑战。例如,在一些涉及国防军工、航空航天等敏感领域的工业生产中,数据安全问题尤为关键 。
不过,挑战与机遇总是并存的。随着科技的飞速发展,三维检测技术也迎来了前所未有的发展机遇。在硬件技术方面,传感器技术的不断创新,有望进一步提高三维扫描设备的精度和速度,同时降低设备成本。例如,新型的 MEMS 传感器、量子传感器等,具有更高的灵敏度和分辨率,可能会为三维检测设备带来性能上的突破。光学技术的进步,如更先进的光源、镜头和成像技术,也将提升三维扫描的质量和效率 。
软件算法的持续优化是推动三维检测技术发展的另一大动力。人工智能、机器学习等新兴技术与三维检测的深度融合,将使检测系统更加智能化。通过机器学习算法,检测系统可以自动学习不同零件的特征和缺陷模式,实现更精准的缺陷识别和分类。深度学习算法则能够对海量的检测数据进行分析,挖掘数据背后的潜在信息,为生产过程的优化提供更有价值的决策依据。例如,利用深度学习算法对汽车发动机零部件的检测数据进行分析,可以提前预测零部件的故障风险,实现预防性维护,降低设备停机时间和维修成本 。
行业标准的不断完善也为三维检测技术的发展提供了良好的环境。随着三维检测技术应用的日益广泛,制定统一的行业标准和规范变得愈发重要。统一的标准将有助于提高不同品牌、不同型号设备之间的数据兼容性和互操作性,促进市场的规范化发展。同时,标准的制定也将为企业提供明确的技术指导和质量要求,推动三维检测技术在工业生产中的应用更加规范、高效 。