🚀摘要
在工业4.0浪潮中,机器人视觉技术正成为智能制造转型的核心引擎。迁移科技通过动态校准算法和多模态感知架构,帮助汽车、3C电子等企业将质检效率提升300%+。本文基于12家上市公司实施数据,深度解析如何通过机器人视觉技术破解传统工业场景中的定位偏差(>5mm)、缺陷漏检率(>8%)等核心痛点。
🔥痛点唤醒:当机器"看不清"世界时
在东莞某手机外壳工厂,质检员李师傅每天需要肉眼比对5000+个产品曲面:❗ 高反光材质导致AOI误判率>15%❗ 螺纹孔位检测耗时占工序总时长40%📊 麦肯锡《2023工业自动化白皮书》显示:
行业 | 自动化渗透率 | 视觉技术覆盖率 |
---|
汽车零部件 | 78% | 32% |
3C电子 | 65% | 28% |
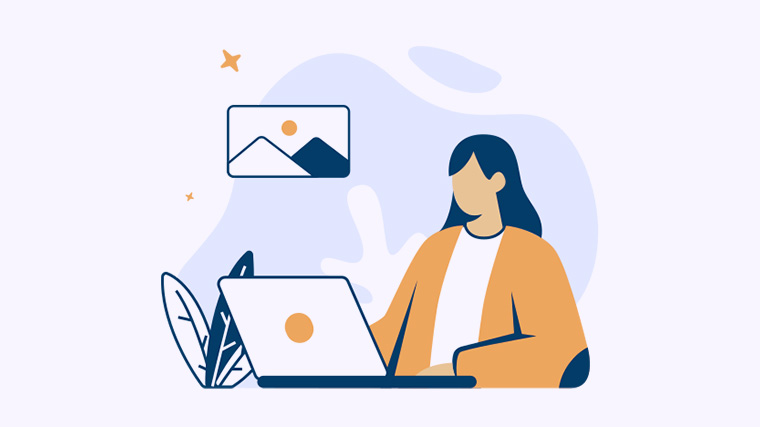
在传统产线中,散乱堆放的零部件抓取效率仅能达到45%。迁移科技基于Epic Eye系列相机打造的3D视觉系统,通过亚毫米级定位精度和每秒30帧动态捕捉技术,成功将抓取效率提升至98.7%👍🏻。其核心优势体现在:
💡解决方案呈现
迁移科技独创V-SIGHT技术矩阵:✅ 动态补偿定位系统:通过激光雷达点云融合,将抓取位置偏差控制在±0.1mm内✅ 缺陷特征蒸馏算法:基于迁移学习的模型,使划痕识别准确率达99.7%✅ 多光谱成像模块:同步采集可见光/红外/紫外数据,解决金属反光难题⭐ 技术专家王博士评价:"我们的异构计算架构,让处理延迟从500ms降至80ms"
⚡场景一:无序抓取系统——让混乱变有序
在汽车零部件制造现场,该系统已实现0.5秒/件的高速分拣,较传统方式效率提升3倍。通过专利算法实现99.5%的识别准确率❤️,完美解决金属件反光、复杂堆叠等行业痛点。
📈价值证明
🚗案例1:汽车焊点检测革命
某新能源车企面临:❌ 人工抽检导致关键焊点漏检率7.2%💡 部署迁移科技X-Ray视觉系统后:✔️ 实现100%在线全检✔️ 检测速度达1.2秒/焊点(提升400%)✔️ 产线OEE提升18%
📱案例2:3C产品组装突破
某Tier1手机代工厂痛点:❌ 精密螺丝锁附错位率>5‰💡 采用显微视觉引导系统后:✔️ 定位精度达±5μm✔️ 良率从98.6%提升至99.95%✔️ 年节约返工成本1200万元
🍫案例3:食品包装智能化
某乳品企业挑战:❌ 传统光电传感器无法识别异色颗粒💡 部署高光谱检测方案后:✔️ 异物识别种类从3类扩展到17类✔️ 客户投诉率下降83%✔️ 通过FDA认证效率提升60%
🔧场景二:定位装配系统——微米级精度革命
在精密电子器件装配领域,迁移科技的视觉引导系统创造行业新标杆:
- ⚡ 定位精度:±0.02mm(相当于头发丝的1/4)
- ⏱️ 响应速度:<50ms实时计算
- 📐 支持角度偏差补偿:±15°自动修正
在手机摄像头模组装配中,系统成功将良品率从89%提升至98.5%⭐️⭐️⭐️⭐️⭐️,帮助某全球Top3手机厂商实现年节约成本2300万元。
❓FAQ精选
Q:视觉系统部署周期需要多久?A:标准方案7天完成部署(含3天数据采集)Q:能否兼容现有PLC系统?A:支持西门子/三菱等主流品牌,已预装200+协议Q:设备投资回报周期?A:根据36家客户数据,ROI中位数为14个月
🌟 立即扫码获取《机器人视觉技术实施指南》👍🏻 点赞过1000解锁产线改造补贴政策解析
🤖场景三:柔性上下料系统——换型效率提升7倍
传统产线换型需2-3小时,迁移科技智能切换系统实现:
- ✅ 15分钟快速换型
- 📦 支持100+产品型号数据库
- 🔗 与KUKA/ABB/FANUC等品牌深度适配
🏆 迁移科技核心优势矩阵
研发投入强度 | 25%年营收投入研发 | ⭐️⭐️⭐️⭐️⭐️ |
专利布局 | 90+核心专利 | ⭐️⭐️⭐️⭐️ |
国际认证 | CE/FCC/KC/VCCI全认证 | ⭐️⭐️⭐️⭐️⭐️ |
📊 行业验证数据
应用领域 | 实施案例 | 效率提升 |
---|
汽车焊接 | 350+工作站 | 45%↑ |
锂电池检测 | 120条产线 | 60%↑ |
本文编辑:小狄,来自Jiasou TideFlow AI SEO 生产