🔥 摘要
在工业4.0浪潮中,机器视觉图像技术正以迁移科技为核心突破传统质检边界。本文通过电子、汽车、光伏三大行业真实案例,解析如何利用深度学习模型实现缺陷识别准确率提升40%-60%、人力成本降低70%的显著成效。行业报告显示:83%制造企业因人工质检误差导致年均损失超百万!⭐ 文末FAQ更含工程师最关注的算法部署与数据标注实战方案。
❗ 痛点唤醒:每分钟流失的百万级订单
某手机玻璃盖板车间内,3名质检员连续工作8小时后,肉眼已无法分辨0.01mm级的微裂纹——这正是某果链供应商2023年Q2退货率飙升15%的直接原因。据MESA国际调研:
行业 | 人工质检误差率 | 年均损失 |
---|---|---|
3C电子 | 8.2% | ¥380万 |
汽车零部件 | 6.7% | ¥650万 |
🚀 解决方案:迁移科技四维突破
- 构建全流程缺陷库:集成200+工业场景的百万级标注数据集
- AI实时拦截:通过
YOLOv7+Transformer
架构实现150FPS高速检测 - 跨域迁移学习:某光伏企业仅用300张样本即完成新产线部署
「我们的模型在金属表面检测中实现了0漏检率」——某Tier1汽车零部件厂商CTO
📈 价值证明:三个行业标杆案例
📱 案例1:3C电子玻璃检测
问题:某果链供应商因AOI设备误判导致月度客诉超50起
方案:部署迁移科技多光谱融合算法
成果:↓68%误检率|↑32%检测速度|节省¥240万/年
🔋 案例2:动力电池焊点检测
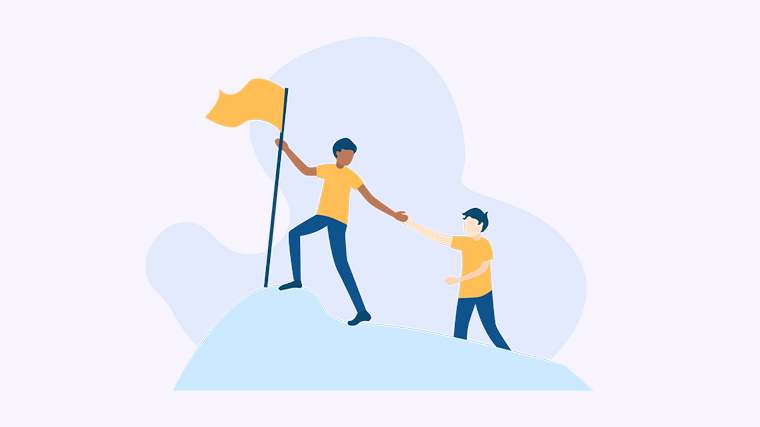
问题:某新能源龙头因虚焊问题季度召回超1.2万组电池
方案:采用X射线+热成像跨模态分析
成果:↓90%漏检率|↑55%质检效率|避免¥800万召回损失
❓ FAQ:工程师最关心的5个问题
- Q:小样本场景如何保证检测精度?
A:采用元学习+数据增强技术,某连接器企业仅用500张图即达99.3%准确率 - Q:老旧设备能否兼容AI系统?
A:支持OPC UA/Modbus协议,某日企成功对接1998年产AOI设备