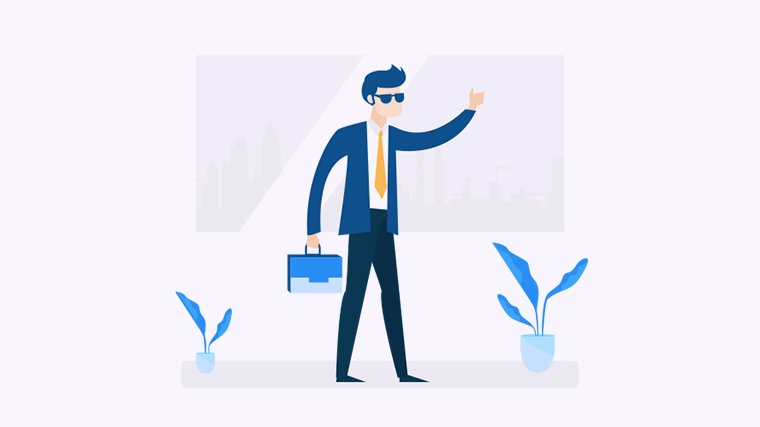
两化深度融合是以信息技术为代表的高新技术与工业领域所有要素融合,进而改造传统工业产业,淘汰落后生产能力,形成新型工业装备,催生新型工业模式,构建新型工业体系,建立现代产业体系,提升工业能力和锤炼工业素质的过程。在这个过程中,信息化要素与工业化要素的全面融合,为传统产业的升级以及工业经济的转型提供了有力的保障和支撑。
国家信息化专家咨询委员会委员、中国航天科技集团总工程师杨海成认为,两化深度融合的本质,是一个以传统产业的升级与换代和新兴产业的崛起与发展为特征的工业体系乃至工业经济的转型升级过程。他提出了促进两化深度融合的六大路径、四个要点。
深度融合六大路径
随着全球经济一体化趋势不断加强和信息技术不断创新,信息化与经济全球化相互交织,我国工业迫切需要转变发展方式,实现产业形态的转型,制造模式的转型,制造过程的转型。通过两化深度融合,将先进信息技术用于产品设计、生产、管理以及全生命周期,具体包括六条路径。
产品高端化。应用嵌入式系统、传感器、RFID、移动互联网、多媒体等技术到产品(装备)中,提高产品的数字化、智能化、网络化程度,增强产品加工制造、物流运输、运行维护等过程中的信息动态感知、智能处理与优化控制能力,促进产品和品牌创新,增加产品附加值。
研发设计知识化。在CAD、CAE、PDM等工业软件基础上,融合产品专业知识、业务流程、标准规范、专业软构件,建立产品正向创新设计的集成平台,支持分布式协同设计、多学科仿真优化、虚拟仿真与物理验证,提高产品自主创新能力。
生产过程智能化。生产制造智能化通过提高生产设备的数字化、智能化和网络化程度以及生产过程的自动化、柔性化和集成化水平,实现生产制造涉及的人员、物料、设备的优化配置和集成化管控,促进生产效率的显著提高,促进从粗放型生产向精益生产转变。
全生命周期绿色化。采用全生命周期评价、制造执行系统、物联网等新型信息技术,强化研发设计、生产制造、销售、供应、运行、报废回收等产品全生命周期的环境影响评价与优化,提高资源利用率,减少能源消耗和环境污染,实现经济效益和社会效益协调优化。
制造服务化。以云计算、数据融合处理与分析、远程监控与诊断等技术为支撑,拓展产品研发设计、工程总包、大修维修MRO、系统集成、物流、电子商务、租赁等服务,促进企业从产品生产销售向专业服务商、总包商、系统集成服务商、专业化公共服务商转型。
企业数字化。应用新一代集成协同技术,实现全业务过程数字化综合集成,拓展和优化企业价值链,形成应对动态不确定的市场竞争的企业战略选择执行能力和资源优化配置能力。
转型升级四大重点
杨海成提出,要以改造提升传统制造业的需求作为出发点和落脚点,促进企业核心业务与信息化的深度融合。其重点是要深化高新信息技术在研发设计、生产制造、经营管理等关键业务环节的应用,实现技术创新和业务模式创新,大幅提高企业能源效率和资源综合利用率。
传统制造业的转型也要结合战略性新兴产业的发展。我国开展面向高端产品及装备数字化、智能化、物联化的共性关键技术攻关,大力发展一批支撑两化融合的新兴信息产业。积极采用控制技术、网络通信技术、嵌入式技术等高新信息技术,自主研发高端产品及装备的智能化核心系统,推进高新信息技术和核心系统在航空航天装备、轨道交通装备、海洋工程装备、智能制造装备等重大产品及装备中的集成应用。
同时,我国要加强制造业各行业之间的交叉融合,特别是推进制造业与服务业的融合,促进产业结构优化和制造业的服务化转型。利用远程监控、数据融合分析与处理等新型信息技术,支撑装备制造企业开展工程总包及成套服务、大修维修服务、产品后市场服务,促进制造企业强化服务手段,支持第三方专业化制造服务的发展等。
我国还要做大做强工业软件产业,促进软件企业的转型,完善两化深度融合的支撑保障体系。必须紧密结合工业领域两化融合的发展需求,采用不同策略发展工业软件,结合重大产品/工程,带动工业软件发展,自主研发部分核心领域的工业软件,将工业软件与标准规范、知识经验、业务流程等要素融合起来,打造信息化的软装备。