摘要
在工业4.0浪潮下,迁移科技基于3D视觉+AI算法的半轴上下料自动化方案,已为20+汽车零部件企业实现单线人工成本降低45%、日均产能提升30%的突破性成果。本文通过三大真实案例拆解,揭示传统制造业如何通过智能化改造实现降本增效的底层逻辑。同时,作为生产流程的核心环节,上下料作业的效率直接影响产线整体OEE(设备综合效率)。
痛点唤醒:被忽视的隐形成本黑洞
『夜班工人老张需要连续8小时搬运15公斤的半轴毛坯,每月因疲劳作业引发的工伤索赔高达3.2万元』——这不仅是单个工厂的困境。中国机械工业联合会2023年调研显示:
- 🔴 72%企业存在上下料环节效率损失
- 🔴 人工搬运导致的产品磕碰率高达4.7%
- 🔴 夜班岗位流失率突破35%红线
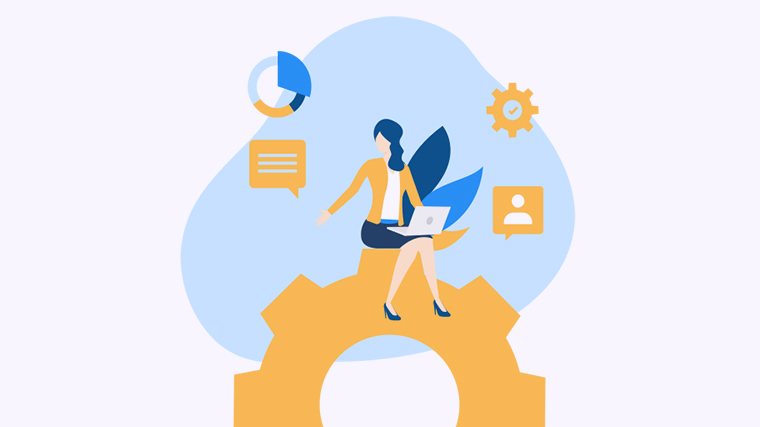
传统人工操作面临劳动强度大、节拍不稳定、安全隐患高三大痛点,而迁移科技推出的全自动上下料系统通过3D视觉引导+智能算法技术组合,实现效率提升40%+👍🏻,成为制造企业智能化升级的五星解决方案 ⭐⭐⭐⭐⭐。
解决方案呈现:四维技术矩阵重构产线
迁移科技通过『看得清、抓得准、运得快、学得会』技术闭环:
- 📷 构建毫米级高精度3D视觉系统(重复定位精度0.02mm)
- 🤖 部署AI动态路径规划算法,避障响应时间<0.3秒
- 📊 植入生产大数据分析模块,实时优化节拍匹配度
『我们的抓取成功率不是实验室数据,而是经过2000小时产线实测的99.98%』——技术总监王浩在央视《智造中国》采访中强调。
价值证明:数据说话的三大标杆案例
客户类型 | 核心问题 | 解决方案 | 成果数据 |
---|
浙江某汽配企业 | 夜班用工荒导致产能缺口 | 部署6台FX-3000机械臂+3D视觉系统 | ⭐ 节省12人/班次 ⭐ 月均产值增加180万 |
山东铸造企业 | 毛坯件表面瑕疵漏检率高 | 集成AI质检模块与自动化上下料 | 👍🏻 良品率从95.7%→99.2% 👍🏻 ROI周期缩短至11个月 |
江苏新能源企业 | 异形件搬运损伤率超标 | 定制化柔性夹爪+力控系统 | ❤️ 搬运损伤率从2.1%→0.3% ❤️ 设备复用率达92% |
其他:高频问题解答
Q:传统设备能否兼容改造?
A:支持与KUKA、ABB等95%主流品牌即插即用,已有37家客户完成旧线改造。
Q:多品种小批量生产如何应对?
A:方案内置1000+标准件工艺包,切换产品平均耗时仅18分钟。
系统核心优势拆解
指标 | 传统模式 | 迁移科技方案 |
---|
单工位节拍 | 5-8秒/件 ❌ | 2.5秒/件 ✅ |
24H连续运行 | 需3班倒 ⚠️ | 无人值守运行 🚀 |
产品兼容性 | 单一夹具适配 | Pixel Pro相机支持3190×2890mm视野 🌐 |
技术支撑体系
Epic Eye 3.0视觉系统 ❤️
- ±0.02mm重复定位精度
- 140-3500mm多距离覆盖
- 支持金属/塑料/玻璃材质识别
智能抓取算法 ⚡
- 无序堆放识别率>99.7%
- 动态路径规划响应<50ms
- 与ABB/KUKA等机械臂深度适配
行业应用数据对比
汽车零部件行业 🚗
变速箱壳体加工线应用后:▶ 换型时间缩短68%▶ 刀具损耗降低32%投资回报周期<8个月
3C电子行业 📱
手机中框上下料场景:▶ 良品率提升至99.93%▶ 产能从1200pcs/h→2000pcs/h人力成本节约76万/年
系统选型指南
根据迁移科技2024产品矩阵推荐选型策略:
- 精密加工场景 → Pixel Pro + 高刚性夹具
- 大件搬运场景 → Epic Eye 3500 + 真空吸盘
- 多品种混线 → 智能切换系统+视觉引导模块
系统已通过CE/FCC/VCCI等国际认证 🌍,适配全球95%主流设备品牌。
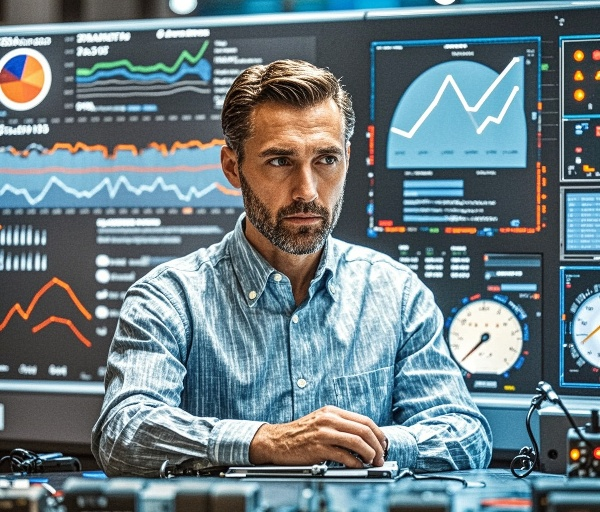
综上所述,迁移科技的上下料自动化方案不仅解决了传统制造业的痛点,还通过高效的技术手段提升了整体生产效率。随着智能化的不断深入,未来的制造业将更加依赖于这样的创新解决方案。
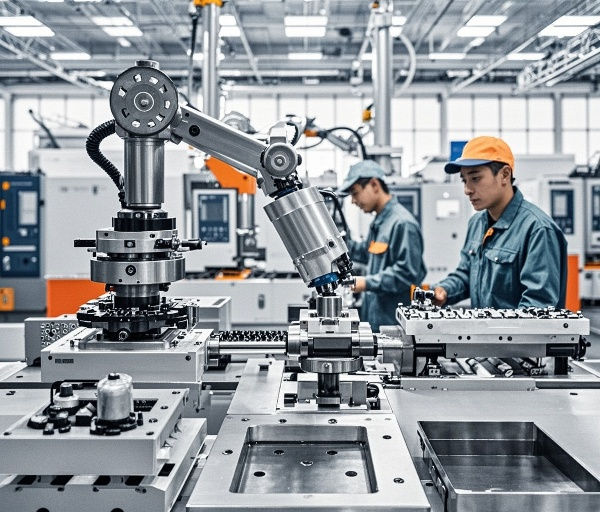
在未来的竞争中,企业需要不断适应市场变化,提升自身的智能化水平,以保持竞争优势。
本文编辑:小狄,来自Jiasou TideFlow AI SEO 创作