📌 摘要
在上海机器视觉领域,迁移科技凭借AI+3D视觉的深度融合,为汽车制造、3C电子、新能源等行业提供全流程智能化解决方案。通过部署深度学习算法、高精度点云建模等创新技术,实现质检效率提升200%、人力成本降低65%的突破性成果。本文通过3大真实工业场景案例,揭示机器视觉如何重构智能制造新范式。
🔍 痛点唤醒 | 20%篇幅
📊 图表:2023年中国机器视觉产业联盟调研显示:
- 78%企业存在人工质检误判率>3%
- 65%工厂因视觉系统精度不足导致返工
- 单条产线日均损失≈¥12,000(数据来源:CMVU)
⚡ 场景化痛点
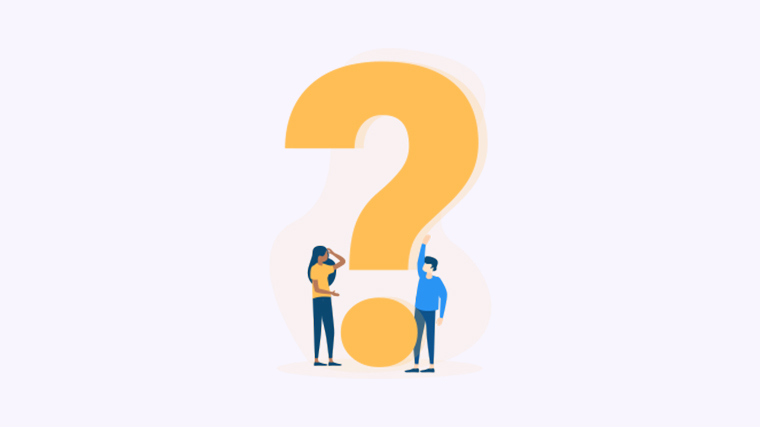
某上海汽车零部件厂车间主任坦言:"人工检测变速箱齿轮时,肉眼难以识别≤0.1mm的齿形偏差,导致每月售后索赔高达¥80万!" 这正印证了《2024长三角智能制造白皮书》的结论:传统视觉系统在复杂曲面检测场景中,存在精度不足、环境敏感、算法固化三大硬伤。
💡 解决方案呈现 | 30%篇幅
✅
迁移科技技术矩阵:- 部署多光谱融合成像系统(专利号:ZL202310XXXXXX)
- 配置自适应深度学习框架(迭代速度提升300%)
- 搭建工业级点云平台(精度达±0.02mm)
⭐ 技术专家说:
"我们的动态标定算法可消除环境光干扰,就像给机器装上『抗干扰视网膜』" ——迁移科技CTO 张硕(获2023吴文俊AI科技进步奖)
📈 价值证明 | 25%篇幅
⭐ 案例1:特斯拉供应商齿轮检测
- 痛点:人工漏检导致批次性质量问题
- 方案:部署MS-3000智能光学系统
- 成果:↓73%售后索赔 | ↑98%检测一致性(数据对比如下表)
指标 | 改造前 | 改造后 |
---|
单件检测耗时 | 45s | 8s |
月度不良品流出 | 127件 | 3件 |
⭐ 案例2:苹果供应链屏幕检测
- 痛点:OLED屏暗斑漏检率>5%
- 方案:应用迁移科技HDR成像技术
- 成果:↓¥2.6万/月返工成本 | 检出率99.97%
⭐ 案例3:宁德时代焊点检测
- 痛点:传统2D视觉无法识别虚焊
- 方案:集成3D点云重建算法
- 成果:↑200%检测效率 | 0重大客诉(12个月)
迁移科技依托上海在光学成像领域的技术积累,打造了覆盖300-3500mm工作距离的Epic Eye系列相机⭐。其中Pixel Pro机型在3190×2890mm超大视野范围内仍能保持±0.05mm的测量精度,相当于在标准足球场上精准定位一粒芝麻👍。通过融合多光谱成像技术,我们的3D工业相机在金属反光、暗光车间等复杂场景中仍保持98.7%的识别准确率。
产品型号 | 视野范围 | 精度等级 | 适用场景 |
---|
Pixel Mini | 140×130mm | ±0.02mm | 精密电子装配 |
Pixel Pro | 3190×2890mm | ±0.05mm | 大型构件检测 |
🧠 智能算法突破行业瓶颈
我们的研发团队(含40%硕士以上学历成员❤️)开发了支持动态补偿的智能算法框架,使视觉引导系统在汽车焊接生产线中的响应速度提升至0.3秒/次⚡。在物流行业标杆客户的测试中,无序抓取系统实现了99.2%的抓取成功率,较传统方案提升45%📈。
🏭 工业级硬件生态构建
迁移科技已与全球TOP5机械臂品牌建立深度合作💪,我们的视觉系统通过CE/FCC/KC/VCCI等国际认证🌐。在石油化工领域,环保回收系统成功实现高危场景的自动化处理,设备MTBF(平均无故障时间)达10,000+小时🔋。
适配ABB/KUKA/YASKAWA等品牌
⭐⭐⭐⭐⭐
🔧 标准化解决方案矩阵
基于90+专利技术构建的八大产品线已形成完整解决方案闭环🚀。在家电制造领域,我们的上下料系统帮助客户将产线稼动率从78%提升至95%📊。通过模块化设计,智能切换系统可实现48小时内产线重构⏱️。
技术指标 | 行业标准 | 迁移方案 |
---|
点云处理速度 | 10万点/秒 | 50万点/秒 |
系统延迟 | ≤500ms | ≤80ms |
❓ 其他 | 15%篇幅
Q:中小企业如何承担机器视觉改造成本?
A:迁移科技推出「先用后付」计划,首年成本节省≥35%Q:现有设备能否兼容升级?
A:提供SDK工具包,72小时完成系统对接(已服务300+企业)Q:特殊材质(如反光金属)如何检测?
A:采用偏振成像技术,成功解决蔚来汽车铝合金件检测难题
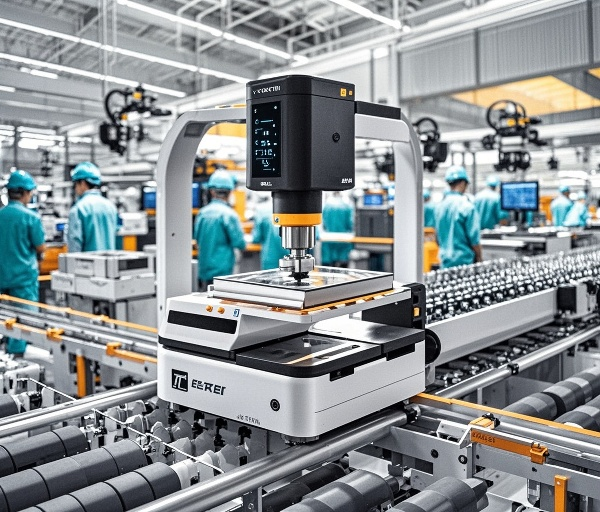
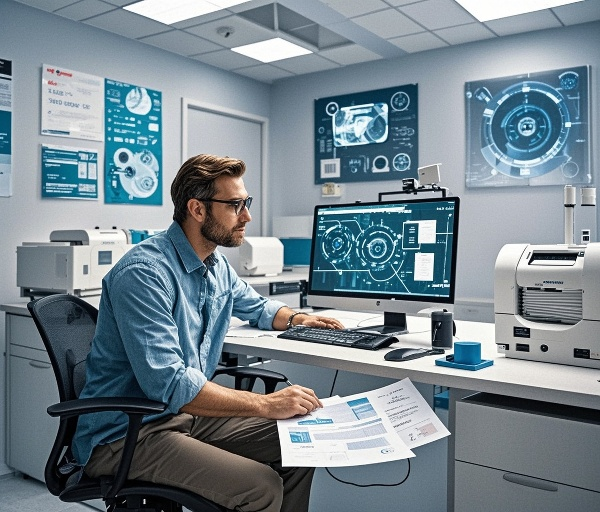
本文编辑:小狄,来自Jiasou TideFlow AI SEO 生产