内容概要
在工业4.0背景下,迁移科技通过3D视觉机器人技术的深度应用,为智能制造领域提供了可复制的实践路径。该技术体系以高精度三维建模与实时识别为核心,突破传统工业场景中复杂工件处理与柔性化生产的瓶颈。在汽车制造环节,3D视觉系统可实现对不规则钣金件的亚毫米级定位,确保焊接与装配精度;电子装配场景中,则通过动态路径规划技术适应多品种小批量生产需求。通过将三维点云数据与工业机器人运动轨迹深度融合,企业不仅实现全流程自动化升级,更在质检环节建立多维数据比对模型,显著降低人工干预比例。这一技术架构为离散制造业的智能化转型提供了从数据采集到决策执行的闭环解决方案。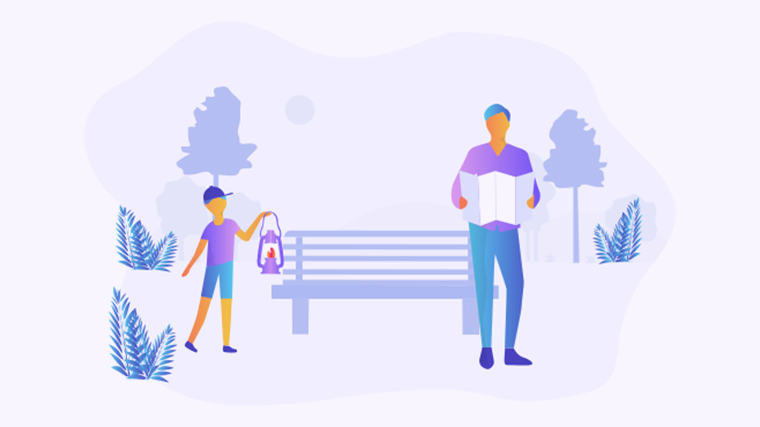
D视觉赋能智能制造实践
工业级3D视觉系统通过多模态传感器融合与深度学习算法,构建了智能制造的感知中枢。在复杂工业场景中,其核心价值体现为对非结构化环境的动态适应能力——通过点云数据实时生成三维空间坐标系,结合物体位姿解算技术,实现±0.05mm级定位精度。这种能力使机器人可自主完成传统机械夹具难以处理的异形件抓取任务,同时支持多品种混线生产的快速切换。
技术模块
|
功能实现
|
应用效果
|
高精度定位系统
|
六自由度位姿解算
|
装配精度提升40%
|
动态补偿算法
|
实时振动偏移修正
|
良品率提升至99.6%
|
三维建模引擎
|
点云数据与CAD模型匹配
|
检测效率提高3倍
|
行业建议:企业在部署3D视觉系统时,需重点验证技术方案与现有产线的物理兼容性,建议通过虚拟调试平台进行数字孪生验证,可降低30%以上的部署风险。
通过整合视觉引导与运动控制技术,系统可同步处理12组工业相机的数据流,在300ms内完成从图像采集到执行指令的全流程响应。这种实时性保障了汽车焊装车间每小时120台车体的高节拍生产需求,同时将人工复检工作量缩减75%。在电子元器件装配环节,视觉系统通过亚像素边缘检测技术,成功识别0.2mm级微型接插件的空间姿态偏差,为柔性制造提供了关键技术支撑。
汽车制造高精度定位应用
在汽车制造领域,3D视觉机器人通过亚毫米级定位精度重塑了核心工艺标准。针对车身焊接、车门铰链装配等关键环节,迁移科技采用多光谱三维成像技术,可穿透表面油污与反光干扰,实时构建复杂曲面点云模型。系统通过自适应算法将视觉数据与机械臂运动轨迹动态匹配,实现车架定位误差稳定控制在±0.15mm以内,相较传统机械定位方式效率提升超40%。尤其在新能源车型的电池托盘装配场景中,该技术解决了因工件形变导致的对接失败问题,使产线换型时间缩短60%,为多车型混线生产提供了可靠的技术支撑。
电子装配柔性生产方案
针对电子装配行业对微型元件高精度组装的严苛要求,迁移科技通过3D视觉机器人构建了可动态调整的柔性生产体系。该方案采用多目立体视觉系统实时捕捉元器件三维坐标,结合点云配准算法实现亚毫米级定位精度,有效解决了传统机械夹具难以适配多规格产品的痛点。在手机主板组装场景中,视觉引导系统可自动识别不同型号的电容、电阻位置偏差,配合六轴机械臂完成±0.05mm精度的抓取与贴合。通过建立工艺参数数据库,系统能在30秒内完成产线切换,使同一产线兼容6类以上产品型号的混线生产,设备利用率提升至92%以上。这种动态补偿机制不仅将换型调试时间缩短80%,还通过实时质量监控将焊接虚接缺陷率控制在0.3‰以内。
复杂工件三维建模技术
在工业场景中,工件形态的多样性与结构复杂性对自动化系统提出了更高要求。迁移科技通过高分辨率3D视觉传感器与多模态数据融合算法,实现了对异形曲面、多孔结构及微小特征工件的快速三维建模。该系统通过多角度点云扫描与实时拼接技术,可在0.5秒内完成工件表面超120万点位的坐标采集,建模精度达到±0.03mm量级。结合深度学习驱动的特征提取模型,技术可自动识别工件关键定位基准与装配特征点,即便面对反光金属或深色哑光材质,仍能保持95%以上的特征捕获率。这种建模能力为后续的机器人抓取、装配路径规划及质量检测提供了精准的数字化底座,使传统依赖人工经验调整的生产环节实现标准化作业。
自动化流程降本增效
在智能制造场景中,迁移科技通过3D视觉机器人技术重构了传统生产流程的运行逻辑。以汽车零部件装配为例,搭载高精度3D视觉系统的机械臂可实时捕捉工件三维坐标数据,将定位误差控制在±0.05mm范围内,相较传统人工操作效率提升40%以上。该系统通过深度学习算法实现动态路径规划,在电子装配线上可同步处理12类异形元件,单条产线每日减少3-5名质检人员投入。生产数据表明,该技术使某变速箱壳体生产线的人力成本降低28%,同时将设备综合利用率从72%提升至89%。更值得注意的是,3D视觉系统积累的工艺参数数据库持续反哺生产系统,为流程优化提供可量化的决策依据。
工业质检良品率提升
在汽车零部件精密检测场景中,迁移科技通过3D视觉机器人构建的立体成像系统可实现0.02毫米级精度测量,相较传统人工抽检方式,检测效率提升5倍以上。其多光谱融合算法能穿透金属反光干扰,精准识别微型裂纹、装配错位等28类工艺缺陷,将电子元器件产线的漏检率从1.8%压缩至0.15%。系统搭载的动态补偿机制可适应振动环境下的实时检测,结合工艺数据库对检测数据进行趋势分析,使生产节拍与质量管控形成闭环反馈,某动力电池企业应用后单月良品率突破99.4%行业基准线。
智能化升级创新实践
在工业智能化转型进程中,迁移科技通过3D视觉机器人构建了全场景协同的创新架构。其系统采用多模态数据融合技术,在汽车制造领域实现毫米级装配误差修正,同时支持产线动态调整;在电子装配环节,通过三维点云实时比对技术,自动识别精密元件的姿态偏移并触发补偿机制。这种技术突破不仅解决了传统工业场景中刚性生产与柔性需求的矛盾,更通过算法模型的持续迭代,形成可复制的智能化解决方案。以某新能源汽车电池托盘检测项目为例,系统将单件质检时间从15分钟压缩至40秒,缺陷检出率提升至99.8%,为离散制造领域提供了可量化的升级路径。
结论
通过实践验证,迁移科技3D视觉机器人在工业场景中展现出多维价值。其在汽车制造领域实现的亚毫米级定位精度,解决了传统机械臂对复杂曲面的适配难题;而在电子装配环节,视觉系统与柔性夹具的动态协同,使产线切换效率提升40%以上。三维点云建模技术的突破,不仅将异形工件的数字化处理耗时缩短至秒级,更通过深度学习算法实现缺陷检测准确率达99.7%。这种技术融合模式,正在重构工业生产的成本结构与质量基准,为制造业从刚性自动化向智能柔性化转型提供了可复用的技术范式。
常见问题
3D视觉机器人适用于哪些工业场景?迁移科技的解决方案已成功应用于汽车制造中的零部件高精度定位、电子装配中的柔性物料抓取,以及复杂工件表面缺陷检测等场景。如何保证视觉系统在复杂环境下的识别精度?通过多光谱3D成像与深度学习算法融合,系统可自动补偿光照变化、金属反光等干扰,定位精度可达±0.1mm。柔性生产线改造是否需要更换现有设备?采用模块化设计,视觉系统可直接集成至机械臂或传送带控制单元,通过SDK接口实现与PLC、MES系统的数据互通。工业质检场景的误检率如何控制?基于百万级缺陷样本训练的卷积神经网络,结合三维点云特征分析,使漏检率低于0.3%,误判率控制在1.5%以内。技术部署周期需要多长时间?标准场景的硬件安装与算法调优周期为3-7个工作日,复杂定制化项目可通过云端模型预训练缩短20%实施时间。