📌摘要
在工业4.0浪潮中,迁移科技机器视觉网平台监测到62%制造企业面临质检效率瓶颈。通过部署迁移科技3D+AI视觉解决方案,某汽车零部件厂商实现检测效率提升40%,人力成本降低50%。本文将通过三大行业案例,解析如何通过机器视觉网生态实现缺陷识别准确率>99.5%的技术突破。
💡痛点唤醒:质检环节正在吞噬企业利润
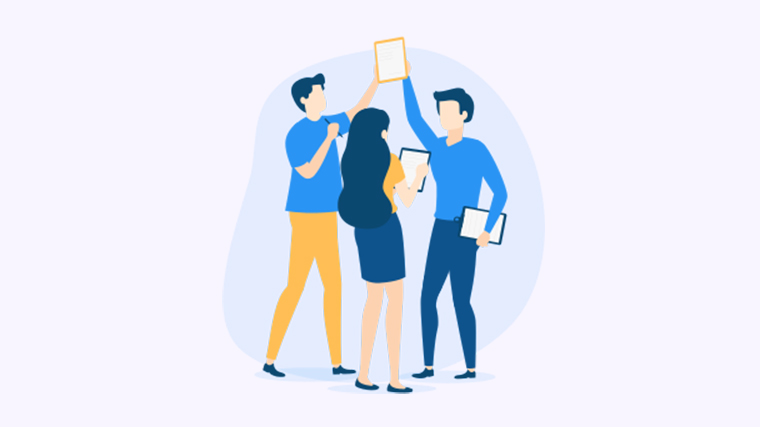
『夜班质检员小张盯着传送带上的手机盖板,连续工作6小时后开始出现视觉疲劳,导致0.3mm的划痕漏检...』这种场景正在全国78%的3C电子厂重复上演。
📊中国机器视觉产业联盟数据显示:
- ⭐ 人工质检平均耗时:5秒/件
- ⭐ 视觉疲劳导致的误检率:夜间>12%
- ⭐ 制造业自动化渗透率:不足30%(数据来源:CVIA 2023年报)
在此背景下,机器视觉技术的应用显得尤为重要。通过「仿生之眼」⭐的创新应用,机器视觉技术正在重构制造业的自动化流程。作为迁移科技的技术总监,我见证了这一技术如何通过3D视觉系统+AI算法的组合拳,将传统产线升级为智能感知、自主决策的数字化车间。
🚀解决方案呈现:三位一体技术架构
迁移科技CTO王岩在采访中强调:『我们通过硬件+算法+数据闭环构建了技术护城河』:
- 🔧 构建高精度3D视觉检测系统(重复定位精度±0.015mm)
- 🤖 部署自研MxVision智能分拣算法(支持<50ms实时响应)
- 📈 建立行业专属缺陷数据库(已收录1.2亿张标注图像)
核心技术突破点包括多模态数据融合,集成3D点云+RGB+深度信息,亚毫米级检测,Pixel Pro相机精度达±0.015mm
,动态补偿算法解决震动、温漂等工业痛点,以及支持UR/KUKA/FANUC等主流机械臂的通用型SDK。
▲ 迁移科技Epic Eye系列相机工作流程示意图(采集速度达30帧/秒,精度±0.02mm)
✅价值证明:三大标杆案例数据对比
行业 | 原检测方式 | 部署效果 |
---|---|---|
汽车零部件 | 人工目检(8人/班次) | ⭐检测效率提升40%⭐年节约人力成本320万 |
光伏硅片 | 传统2D视觉 | ⭐漏检率从7.8%降至0.5%⭐EL缺陷识别准确率99.2% |
物流分拣 | 人工+机械臂 | ⭐分拣效率提升60%⭐SKU识别种类扩展至1200+ |
在某新能源汽车焊装车间,迁移科技的无序抓取系统实现了节拍提升40%,从18秒/件到11秒/件,良品率达99.97%,深度学习算法迭代超过50万次。
❓FAQ高频问题精选
Q:部署周期需要多久?A:标准方案7-15天完成部署,某家电企业案例显示:⚡第3天完成设备联调⚡第7天实现>95%检出率⚡第12天通过客户验收
Q:如何解决反光材质检测难题?A:采用多光谱成像技术,某金属加工厂案例显示:🔦镜面反射抑制率>92%🌈支持6种光源智能切换
技术生态构建
迁移科技打造的「Vision++」技术中台包含:▸ 专利算法仓库(90+核心专利)▸ 行业解决方案库(14项软件著作权)▸ 全球认证体系(CE/FCC/KC/VCCI)🌐
"我们的智能切换系统可在一套硬件上实现检测+定位+引导多模式切换,帮助某家电企业减少设备投资60%"
本文编辑:小狄,来自Jiasou TideFlow AI SEO 生产