在工业制造的庞大体系中,工业零件检测堪称至关重要的一环,宛如工业制造的 “睛雨表”,精准反映着生产过程的健康状况与产品质量的高低。每一个工业零件都像是工业产品这座大厦的基石,其质量的优劣直接关乎到最终产品的性能、可靠性与安全性。例如在汽车制造中,发动机的零部件若是存在尺寸偏差或内部缺陷,可能导致发动机动力不足、油耗增加,甚至引发严重的安全事故;航空航天领域更是如此,一个小小的零件故障,都可能在高空环境下引发灾难性的后果 。
传统的工业零件检测方法多种多样,常见的有:
检测方法
|
操作方式
|
特点
|
人工目视检测
|
检测人员凭借肉眼,直接观察零件表面,判断是否存在缺陷
|
灵活性高,能直观发现明显缺陷;但效率低、主观性强,容易受检测人员经验、疲劳程度等因素影响,对于微小缺陷难以察觉
|
接触式测量
|
利用卡尺、千分尺等工具,与零件表面直接接触,测量零件的尺寸、形状等参数
|
测量精度相对较高,适用于简单形状零件的尺寸测量;但操作繁琐,测量速度慢,且可能对零件表面造成损伤,不适用于高精度、复杂形状零件的检测
|
无损检测
|
借助超声、射线、磁粉等技术,在不破坏零件的前提下,检测零件内部的缺陷
|
能有效检测内部缺陷,保障零件内部质量;然而设备昂贵,检测成本高,对检测人员的专业要求也很高
|
这些传统方法在工业发展历程中发挥了重要作用,但随着现代工业向高精度、高效率、高复杂度方向迈进,其局限性愈发凸显,难以满足日益增长的生产需求,于是,工业零件三维检测技术应运而生,为工业零件检测带来了新的变革与突破。
从传统到三维:检测技术的 “变身”
传统检测方法大盘点
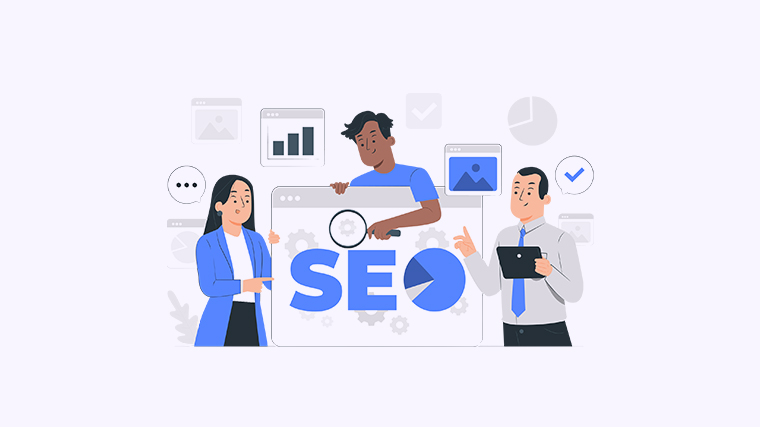
在过去,工业零件检测主要依赖一些传统工具和方法。卡尺是最常见的长度测量工具之一,通过游标尺与主尺的配合,能较为精确地测量零件的外径、内径、长度、深度等尺寸 。比如在机械加工车间,工人师傅们经常用卡尺来测量轴类零件的外径,以判断其是否符合设计要求。塞规则是用于检测孔径的专用量具,一般分为通规和止规,通过将塞规插入被测孔径,根据通规能通过、止规不能通过的原则来判断孔径是否合格,常用于批量生产中对孔径的快速检测。千分尺的测量精度比卡尺更高,可精确到 0.01mm 甚至更高,常用于对精度要求极高的零件尺寸测量,如精密模具的零部件测量。
传统方法的 “烦恼”
传统检测方法虽然在一定时期内满足了工业生产的基本需求,但在面对现代工业的高精度、高效率、高复杂度要求时,逐渐暴露出诸多问题。效率低下是其一大痛点,以人工使用卡尺测量为例,每测量一个尺寸都需要人工操作、读数和记录,对于复杂零件,测量一个完整的尺寸链需要耗费大量时间,难以满足大规模生产线上快速检测的需求。在精度方面,传统检测方法也存在局限性,像卡尺、千分尺等接触式测量工具,由于测量力的存在,可能会对零件表面造成微小损伤,影响测量精度,而且人工读数也容易引入人为误差。对于复杂曲面的零件,传统检测方法更是力不从心,无法全面采集零件表面的几何信息,导致检测结果不完整,无法准确评估零件的整体质量。
三维检测技术登场
随着科技的不断进步,三维检测技术应运而生,为工业零件检测带来了革命性的变化。三维检测技术是一种通过对物体进行全方位扫描,获取其三维空间坐标数据的测量技术。它能够快速、准确地获取零件表面的完整几何信息,并将这些信息转化为数字模型。在实际检测过程中,三维检测设备会对工业零件进行扫描,生成包含零件表面所有细节的点云数据,然后将这些点云数据与预先建立的 CAD 模型进行比对分析,通过专业软件计算出零件的实际尺寸与设计尺寸之间的偏差,从而精确判断零件是否合格,以及存在哪些缺陷和误差。
三维检测 “大揭秘”
三维检测的 “秘密武器”:设备与原理
在三维检测领域,有着多种功能强大的设备,它们如同身怀绝技的 “秘密武器”,为工业零件检测提供了有力支持。手持式三维扫描仪以其便携性和灵活性著称,它可以方便地在各种工作场景中使用,无论是在车间现场对大型零件的检测,还是在实验室对小型精密零件的测量,都能轻松应对。其工作原理主要基于激光三角测量原理,激光发射器发射出一束激光,照射到零件表面后,反射光被相机接收,通过计算激光发射点、相机接收点与零件表面反射点之间的几何关系,从而确定零件表面点的三维坐标 。例如在汽车零部件的售后维修检测中,维修人员可以手持扫描仪,快速对损坏的零部件进行扫描,获取其实际形状和尺寸数据,与标准模型对比,精准判断损坏程度和范围,为维修提供准确依据。
关节臂式三维扫描仪则像是一个灵活的机械手臂,它具有多个可活动关节,能够在较大空间范围内对零件进行全方位扫描,适用于大型、复杂形状零件的检测。这种扫描仪一般采用光学测量原理,通过安装在关节臂末端的测头,利用光学传感器获取零件表面的点云数据 。在航空航天领域,对于飞机发动机叶片这样形状复杂且精度要求极高的零件,关节臂式三维扫描仪可以在叶片的不同位置进行多角度扫描,精确采集叶片表面的三维数据,确保叶片的制造精度符合设计要求,保障发动机的性能和安全。
结构光三维扫描仪采用的是结构光技术,它通过投影仪将具有特定编码信息的结构光图案投射到零件表面,当这些图案照射到零件表面时,会因零件表面的形状起伏而发生变形,相机从不同角度拍摄变形后的图案,然后利用三角测量原理,通过计算投影仪、相机与零件表面各点之间的几何关系,解算出零件表面各点的三维坐标,从而构建出零件的三维模型。在消费电子领域,对于手机外壳、电脑键盘等零部件的检测,结构光三维扫描仪能够快速、准确地获取零部件表面的细微特征和尺寸信息,高效检测出可能存在的缺陷,如表面划痕、尺寸偏差等,满足消费电子产品大规模生产中的高精度检测需求。
三维检测 “四步走”
工业零件三维检测通常遵循一套严谨的流程,可大致分为三维扫描、数据处理、模型比对、结果分析四个关键步骤。
三维扫描是检测的第一步,也是获取零件原始数据的关键环节。在这个阶段,根据零件的形状、尺寸、材质以及检测精度要求等因素,选择合适的三维扫描设备,如前文提到的手持式、关节臂式或结构光三维扫描仪等。扫描过程中,扫描设备会围绕零件进行全方位的扫描,发射出的激光、结构光等信号与零件表面相互作用,反射回来的信号被设备接收并转化为一系列的点云数据,这些点云数据就像是零件表面的 “数字指纹”,记录了零件表面各个点的三维坐标信息,为后续的分析提供了原始素材。
完成三维扫描后,得到的大量点云数据还不能直接用于检测分析,需要进行数据处理。数据处理主要包括数据滤波、降噪、精简等操作。由于在扫描过程中,可能会受到环境噪声、设备误差等因素的影响,导致采集到的点云数据存在一些干扰点和噪声点,数据滤波和降噪就是要去除这些无用的噪声数据,提高数据的质量和准确性。数据精简则是在不影响零件几何特征的前提下,减少点云数据的数量,以提高后续处理和分析的效率。例如,通过采用合适的滤波算法,可以去除因扫描时零件表面反光、灰尘等引起的噪声点;利用采样算法对密集的点云数据进行有针对性的精简,保留关键的几何信息,使数据更易于处理和分析。
经过数据处理后,得到的高质量点云数据需要与预先建立的零件 CAD 模型进行模型比对。CAD 模型是根据零件的设计图纸,利用计算机辅助设计软件创建的三维数字模型,它包含了零件的精确设计尺寸和形状信息。将扫描得到的点云数据与 CAD 模型导入到专业的检测软件中,软件会自动根据一定的算法,将点云数据与 CAD 模型进行匹配和对齐,然后计算出点云数据中每个点与 CAD 模型对应点之间的空间坐标偏差,这些偏差数据直观地反映了零件实际制造形状与设计形状之间的差异。
在完成模型比对后,就进入到结果分析阶段。检测人员通过检测软件提供的可视化界面,查看零件的偏差数据分布情况,以彩色云图、偏差报告等形式直观展示出来。根据这些结果,判断零件是否符合设计要求和质量标准。如果偏差在允许的公差范围内,则零件被判定为合格;若偏差超出公差范围,检测人员需要进一步分析偏差产生的原因,是制造工艺问题、设备故障,还是原材料缺陷等,以便采取相应的改进措施,如调整加工参数、维修设备、更换原材料等,确保后续生产的零件质量符合要求。
三维检测 VS 传统检测:数据说话
精度大比拼
在精度方面,三维检测技术展现出了碾压传统检测方法的实力。传统检测方法,如卡尺、千分尺等接触式测量工具,由于受到测量原理、人为操作等因素的限制,测量误差通常在毫米级 。例如,普通卡尺的精度一般为 0.02mm,即使是高精度的千分尺,其精度也多在 0.01mm 左右。而三维检测设备,借助先进的光学测量原理和精密的算法,测量精度可达微米级。以常见的结构光三维扫描仪为例,其精度可以达到 0.01mm 甚至更高,能够精确捕捉到零件表面极其微小的尺寸变化和形状偏差,为高精度工业生产提供了可靠的质量保障。
检测方法
|
精度
|
传统检测(卡尺、千分尺等)
|
毫米级,如卡尺精度一般为 0.02mm,千分尺精度多为 0.01mm
|
三维检测(以结构光三维扫描仪为例)
|
微米级,精度可达 0.01mm 甚至更高
|
效率大对决
从效率上看,三维检测技术同样具有明显优势。传统检测方法,尤其是人工操作的检测方式,效率十分低下。比如人工使用卡尺测量一个复杂零件的多个尺寸,每测量一个尺寸都需要手动操作、读数、记录,整个过程繁琐且耗时。对于批量生产的零件,检测效率更是难以满足生产需求。而三维检测设备能够实现自动化、快速扫描,大大缩短了检测时间。以手持式三维扫描仪为例,在对中等复杂程度的零件进行扫描时,仅需几分钟即可完成整个零件表面的三维数据采集,后续的数据处理和分析也可通过专业软件快速完成,相比传统检测方法,检测效率提升数倍甚至数十倍。
检测方法
|
检测数量
|
检测时间
|
传统检测(人工使用卡尺测量)
|
50 个中等复杂程度零件
|
约 20 小时
|
三维检测(手持式三维扫描仪)
|
50 个中等复杂程度零件
|
约 1 小时
|
检测完整性对比
在检测完整性方面,三维检测技术的优势也十分突出。传统检测方法往往只能对零件的部分关键尺寸或表面进行抽样检测,难以获取零件的整体几何信息。例如,对于具有复杂曲面的零件,传统检测方法可能只能测量几个有限的点或截面,无法全面反映零件的实际形状和尺寸。而三维检测技术能够对零件进行全方位、无死角的扫描,获取零件表面的完整三维数据,无论是复杂曲面、内部结构还是微小特征,都能被精确捕捉。通过将扫描得到的三维模型与 CAD 设计模型进行全面比对,可以准确发现零件在各个部位可能存在的尺寸偏差和形状缺陷,确保检测结果的完整性和准确性。
检测方法
|
复杂零件检测的数据完整性
|
传统检测
|
只能检测部分关键尺寸或表面,难以获取整体几何信息,对于复杂曲面和内部结构检测能力有限
|
三维检测
|
能够全方位扫描,获取零件表面完整三维数据,准确反映零件整体形状、尺寸及微小特征
|
三维检测的 “高光时刻”
汽车制造:零部件的 “品质守护者”
在汽车制造领域,工业零件三维检测技术宛如一位尽责的 “品质守护者”,发挥着不可或缺的关键作用。以发动机缸体为例,作为发动机的核心部件,其结构复杂,内部包含众多高精度的孔系、油路、水道以及各种复杂的曲面,这些结构的尺寸精度和形状精度直接影响发动机的性能,如动力输出、燃油经济性、排放指标等。利用三维检测技术,在发动机缸体的生产过程中,可对毛坯件进行全面扫描检测,提前发现铸造缺陷,如砂眼、气孔、缩松等,避免将有缺陷的毛坯件投入后续加工,减少废品率和加工成本。在加工完成后,通过三维检测设备精确测量缸体各部位的尺寸,与设计模型进行比对,确保每个缸筒的直径、圆柱度,以及各安装面的平面度、垂直度等关键尺寸都符合严格的公差要求,保障发动机的装配精度和运行稳定性。
汽车轮毂的质量同样关乎行车安全,其动态平衡性能、尺寸精度和结构强度都至关重要。传统检测方法难以全面检测轮毂复杂的曲面轮廓和内部结构。而三维检测技术可以对轮毂进行全方位扫描,获取其完整的三维数据模型,精确检测轮毂的直径、轮辋厚度、螺栓孔位置等尺寸参数,以及表面的平整度、粗糙度等质量指标。通过与标准模型对比,能够快速发现轮毂在制造过程中可能出现的尺寸偏差、变形、裂纹等缺陷,确保每一个出厂的轮毂都符合高质量标准,为汽车的安全行驶提供坚实保障。
航空航天:高标准下的 “检测担当”
航空航天领域对零部件的质量和精度要求近乎苛刻,工业零件三维检测技术在这里成为了满足高标准的 “检测担当”。航空发动机叶片是航空发动机的关键热端部件,在高温、高压、高转速的极端工况下工作,其形状复杂,具有高精度的曲面和薄壁结构,对叶片的型面精度、轮廓度、厚度均匀性以及内部质量都有着极高的要求。哪怕是极其微小的尺寸偏差或内部缺陷,都可能在发动机高速运转时引发严重的安全事故。三维检测技术能够利用高精度的光学扫描设备,对叶片进行微米级精度的扫描检测,不仅可以精确测量叶片的外部形状和尺寸,还能通过无损检测技术,如超声检测、X 射线检测等,与三维扫描相结合,检测叶片内部的缺陷,如裂纹、夹杂、疏松等,确保叶片的质量和性能满足航空发动机严苛的运行要求,为航空发动机的安全稳定运行提供可靠保障。
飞机的结构件,如机翼大梁、机身框架等,通常具有大型化、复杂化的特点,且对结构强度和尺寸精度要求极高。在制造过程中,三维检测技术可以对这些大型结构件进行整体扫描检测,快速获取其三维尺寸数据,与数字化设计模型进行全面比对分析,精确检测出结构件的尺寸偏差、形状变形以及装配位置精度等,及时发现制造过程中的问题并进行调整优化,确保飞机结构件的制造质量和装配精度,保障飞机的整体结构强度和飞行安全。例如在飞机装配过程中,通过三维检测技术对各部件的装配接口进行精确测量和定位,实现高精度的数字化装配,提高装配效率和质量,减少因装配误差导致的安全隐患。
机械制造:全方位的 “质量管家”
在机械制造行业,工业零件三维检测技术就像是一位全方位的 “质量管家”,为提高机械产品质量和可靠性发挥着重要作用。在机械传动零部件,如齿轮、蜗轮蜗杆等的制造过程中,三维检测技术可对其齿形、齿向、齿距等关键参数进行精确测量。齿轮作为机械传动中常用的零件,其精度直接影响到传动的平稳性、噪声和效率。通过三维检测设备对齿轮进行扫描,获取齿轮的三维数据模型,利用专业软件分析齿轮的各项参数,与设计标准进行对比,能够准确检测出齿轮在加工过程中可能出现的齿形误差、齿向误差、齿距累积误差等问题,及时调整加工工艺,保证齿轮的质量和传动性能,提高机械设备的整体运行稳定性和可靠性。
模具在机械制造中广泛应用,其质量直接决定了产品的成型精度和表面质量。三维检测技术可以在模具设计阶段,对设计模型进行虚拟检测和分析,提前发现潜在的设计缺陷和问题,优化模具设计。在模具制造过程中,对模具的型芯、型腔等复杂结构进行三维扫描检测,实时监控加工精度,及时发现加工误差和缺陷,如刀具磨损导致的尺寸偏差、加工过程中的变形等,采取相应的补救措施,确保模具的制造精度和质量。在模具使用过程中,通过定期的三维检测,监测模具的磨损情况和变形程度,为模具的维护和修复提供准确的数据依据,延长模具的使用寿命,降低生产成本。
未来已来:三维检测新征程
技术突破方向
随着科技的飞速发展,工业零件三维检测技术也在不断探索新的突破方向,以满足日益增长的工业生产需求。在精度提升方面,研究人员正致力于开发更先进的光学传感器和算法,以进一步降低测量误差,实现更高精度的检测。例如,通过采用更精密的激光发射和接收装置,以及优化的三角测量算法,有望将三维检测设备的精度提升至亚微米级,甚至更高,从而满足如芯片制造、微纳加工等对精度要求极高的领域需求。
扫描速度的加快也是未来技术突破的重点之一。目前,虽然三维检测设备已经能够实现快速扫描,但在面对大规模生产线上的海量零件检测时,仍需要进一步提高扫描速度。一方面,通过研发更高速的数据采集和传输系统,减少扫描过程中的数据传输延迟;另一方面,利用并行处理技术,同时对多个零件进行扫描,提高整体检测效率,使三维检测技术能够更好地适应现代化大规模生产的节奏。
数据处理智能化也是未来的重要发展趋势。随着人工智能、机器学习等技术的不断成熟,将其应用于三维检测数据处理中,能够实现更高效、更准确的数据分析和缺陷识别。通过对大量检测数据的学习和训练,智能算法可以自动识别零件的各种缺陷类型和特征,无需人工干预,大大提高检测的准确性和效率。同时,智能数据处理还能够实现对检测结果的实时预测和分析,为生产过程的优化提供更有价值的决策支持。
应用领域拓展
除了在汽车制造、航空航天、机械制造等传统领域的广泛应用,工业零件三维检测技术在新能源、医疗设备制造等新兴领域也展现出了巨大的应用潜力。
在新能源领域,随着电动汽车、风力发电、太阳能发电等产业的快速发展,对新能源设备零部件的质量和精度要求越来越高。以电动汽车电池为例,电池模组中的电芯尺寸一致性、极片的平整度和厚度均匀性等参数,直接影响电池的性能和安全性。三维检测技术可以对电池零部件进行高精度的三维扫描检测,确保其尺寸精度和质量符合要求,提高电池的生产良率和性能稳定性。在风力发电领域,对风机叶片的三维检测可以及时发现叶片表面的损伤、裂纹以及内部结构的缺陷,保障风机的安全稳定运行,提高发电效率。
在医疗设备制造领域,三维检测技术同样发挥着重要作用。例如,在假肢制造中,通过对患者残肢进行三维扫描,获取精确的三维数据,能够定制出更贴合患者身体、佩戴更舒适的假肢。在口腔医疗领域,三维检测技术可以用于口腔修复体的制作,如牙冠、牙套等,通过对患者口腔进行三维扫描,制作出高精度的数字化模型,实现修复体的个性化定制,提高修复效果和患者的舒适度。在医疗器械生产过程中,三维检测技术还可以用于检测医疗器械零部件的尺寸精度和表面质量,确保医疗器械的安全性和有效性。
拥抱三维检测,开启工业新篇
工业零件三维检测技术凭借其高精度、高效率、全面检测等显著优势,已在众多工业领域展现出巨大的价值和潜力。它不仅是解决当前工业生产质量检测难题的关键手段,更是推动工业制造向智能化、数字化、高端化发展的重要力量。随着技术的不断突破和应用领域的持续拓展,相信三维检测技术将在未来工业发展中发挥更加核心的作用,助力工业企业在激烈的市场竞争中脱颖而出,共同开启工业高质量发展的新篇章。工业企业应积极拥抱这一先进技术,不断提升自身的检测水平和生产质量,为工业制造的进步贡献力量。