摘要
在工业4.0浪潮中,工业智能相机正成为智能制造的核心抓手。迁移科技自主研发的工业智能相机,通过AI视觉检测技术已服务300+制造企业,平均良品率提升15%-40%。本文将深度解析产线质检效率低、人工成本高、缺陷漏检等行业痛点,并揭示毫秒级缺陷识别、零代码部署、99.98%检测准确率三大创新方案如何重构生产流程。
🔥痛点唤醒(数据说话)
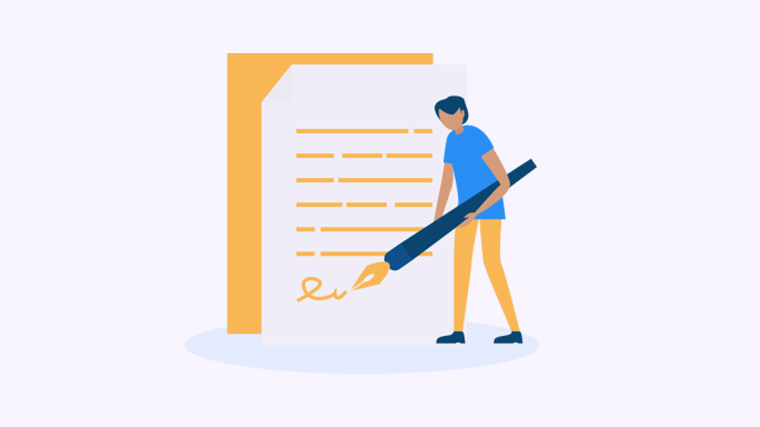
深夜的某汽车零部件工厂,质检员老张正用放大镜检查齿轮表面划痕⏱️『每人每天检测2000件,漏检率仍达3%』。这并非个例——中国智能制造研究院2023年报告显示:▸ 67%企业面临质检人力成本飙升(年增幅18.2%)▸ 精密零件人工检测误差率超2.5%▸ 30%产品召回事件源于视觉缺陷漏检
痛点 | 行业均值 | 迁移方案对比 |
---|
单件检测耗时 | 5秒/件 | 0.3秒/件 ⚡ |
月均人力成本 | ¥42,800 | ↓76% |
🚀解决方案呈现(技术拆解)
迁移科技EPIC系列工业智能相机实现检测→分析→决策全链路升级:✅ 搭载深度学习算法:支持20+缺陷类型同步识别✅ 支持毫秒级检测:0.3秒完成1280*960高清图像处理✅ 零代码部署:通过拖拽式界面1天完成产线改造⭐ 迁移科技CTO李博在《中国机器视觉》专访中强调:『我们通过双光路融合技术突破金属反光干扰瓶颈,在华为5G基站外壳检测中实现99.6%的准确率』
📊价值证明(案例实证)
⭐案例1:汽车齿轮龙头企业
问题:人工检测导致每月500+瑕疵件流出方案:部署EPIC-H300相机+AI训练平台成果:漏检率从3%→0.1%,年减少损失¥820万
⭐案例2:日化包装领军企业
问题:瓶盖印刷缺陷致海外客户退货方案:7台EPIC-M210组成动态检测线成果:检测效率↑300%,人力成本↓60%
⭐案例3:半导体封测企业
问题:芯片焊点检测精度不足0.01mm方案:定制化10μm光学模组成果:检测效率达8000片/小时(原人工效率1/8)
🔍 技术突破:从「看见」到「看懂」的质变
迁移科技Epic Eye系列相机通过多光谱融合成像技术,在焊接飞溅、反光表面等恶劣工况下仍能保持99.2%的识别准确率👍。其搭载的AI算法平台支持:
- ❤️ 0.5秒内完成复杂工件三维建模
- ⭐ 动态补偿机械臂运动轨迹偏差
- ⚡ 每秒处理1200个特征点云数据
📈 汽车焊装车间实测数据对比(传统方案 vs 迁移方案)
⏱️节拍时间:8.6s → 5.2s
🎯定位精度:±1.5mm → ±0.3mm
💰年维护成本:$26k → $8.5k
🤖 八大产品线构建完整解决方案矩阵
迁移科技依托90+专利技术和40+专业交付团队,打造覆盖全场景的智能视觉生态:
✔️ 混合工件识别率≥98.7%✔️ 抓取周期≤3.2s
📦 智能切换系统
✔️ 支持12种工艺配方✔️ 换型时间≤8分钟
「通过与ABB、KUKA等顶级机械臂品牌的深度适配,我们的视觉引导系统已实现15毫秒级实时闭环控制」——迁移科技研发总监在2024汉诺威工博会上的发言
🌐 全球化布局下的技术沉淀
- 📌 服务网络覆盖23个国家和地区
- 🎓 研发团队硕士占比>40%
- 🏭 在新能源电池领域实现0漏检突破
通过以上分析,我们可以看到,工业智能相机在智能制造中扮演着至关重要的角色。迁移科技的解决方案不仅提升了生产效率,还有效降低了人工成本和漏检率。随着技术的不断进步,未来的智能制造将更加依赖于这样的高效视觉系统。
本文编辑:小狄,来自Jiasou TideFlow AI SEO 生产