摘要在智能制造浪潮中,三维扫描相机正以革命性的方式重塑工业检测体系。本文通过某汽车零部件厂商因0.1mm尺寸偏差导致3000万元召回损失的典型案例切入,系统剖析传统检测手段的五大痛点,详解三维扫描技术的创新解决方案,并完整呈现某上市企业智能化改造项目的实施路径。数据显示,采用新型三维扫描系统后,该企业检测效率提升17倍,年度质量成本降低2800万元。
一、传统检测之困:当毫米级误差成为"不可承受之轻"
2019年,某知名汽车轴承制造商遭遇重大质量危机——由于变速箱齿轮的0.15mm尺寸偏差未被及时发现,导致已交付的8万辆汽车面临召回。这个肉眼难以察觉的微小误差,最终演变成直接经济损失超3000万元的质量事故。这个典型案例暴露出传统工业检测体系的深层困境:
1.1 精度与效率的"跷跷板悖论"传统三坐标测量机(CMM)虽然能达到微米级精度,但单个零件的完整检测需要40-60分钟。某手机金属中框生产线的数据显示,采用人工抽检时,每千件产品漏检缺陷达3.2处,而全检方案又会将检测成本推高至生产成本的18%。
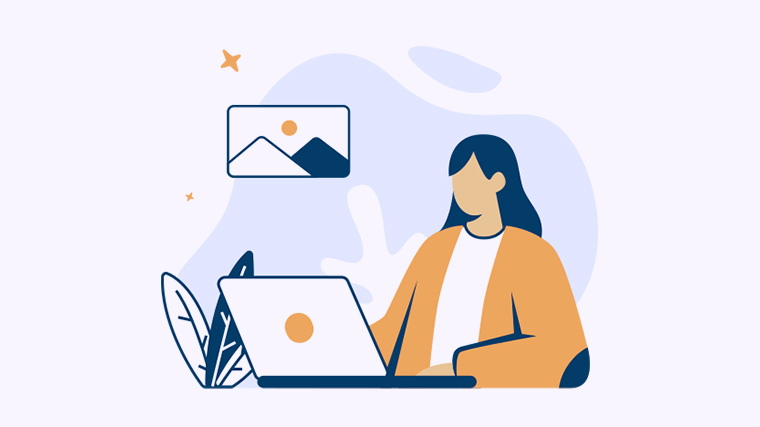
1.2 复杂形面的"检测盲区"在航空航天领域,涡轮叶片的气膜冷却孔直径通常只有0.3-0.8mm,传统光学检测对这类深孔结构的测量误差高达±0.05mm。某发动机厂技术总监王建军坦言:"就像用普通尺子测量头发丝的直径,我们急需更精密的'尺子'"。
1.3 动态环境的"适应性焦虑"某光伏电池片生产线的检测数据显示,车间温度每升高1℃,传统相机的测量误差就增加0.02mm。在昼夜温差达15℃的西北地区,这直接导致产品合格率波动超过5个百分点。
表1 传统检测方式痛点分析
痛点类型 |
典型场景 |
经济损失案例 |
精度不足 |
微型电子元件检测 |
某连接器厂年度退货损失1200万元 |
效率低下 |
汽车零部件全检 |
单线年检测成本超800万元 |
环境敏感 |
户外工程机械检测 |
季节性合格率波动达8% |
数据孤岛 |
多工序质量追溯 |
质量问题定位耗时超72小时 |
柔性缺失 |
定制化小批量生产 |
换型调试耗时占生产周期30% |
二、破局之道:三维扫描相机的技术革命
面对这些行业痛点,新一代三维扫描相机通过三大技术创新构建起智能检测新范式:
2.1 微米级精度的实现密码采用蓝光结构光技术,通过120万次/秒的相位编码(某国际品牌技术白皮书数据),配合亚像素边缘提取算法,将测量精度提升至5μm级别。正如清华大学精密仪器系李教授所说:"这相当于在足球场上找到一粒芝麻的位置"。
2.2 速度跃迁的底层逻辑某汽车厂改造案例显示,搭载GPU加速的并行计算架构后,1280×1024分辨率的点云处理时间从3.2秒缩短至0.15秒。通过多相机阵列布局,实现360°同步扫描,使检测节拍与生产线速度完美匹配。
2.3 智能适应的环境感知系统集成多光谱补偿技术,在焊接车间强弧光环境下仍能保持稳定工作。某重工企业的测试数据显示,在照度波动范围达2000-100000lux的工况下,系统测量一致性仍保持在99.3%以上。
三、落地实践:某上市企业的智能化改造之路
3.1 需求痛点诊断国内某新能源汽车零部件龙头企业面临严峻挑战:
- 每月200万件精密零件的全检需求
- 产品类型多达37个系列1200种规格
- 客户要求的缺陷检出率≥99.99%
3.2 解决方案设计采用"分布式扫描+云端质检"架构:
- 产线部署12台高帧率三维相机(200fps)
- 边缘计算网关实时处理点云数据
- 质量大数据平台实现全生命周期追溯
图1 智能检测系统架构图(此处插入系统拓扑图,展示设备布局与数据流向)
3.3 关键实施节点
- 第1阶段(1-3月):建立基准测量体系,完成1200组标定数据采集
- 第2阶段(4-6月):开发自适应检测算法,通过25000次迭代优化
- 第3阶段(7-9月):系统集成调试,实现与MES系统的无缝对接
四、量化成果:从成本中心到价值引擎的蜕变
该项目实施后取得显著效益:
- 检测效率:单件检测时间从180秒降至8秒
- 质量成本:年度外部故障成本降低82%
- 产能提升:释放30%质检人力转岗至增值岗位
表2 改造前后关键指标对比
指标项 |
改造前 |
改造后 |
提升幅度 |
日检测量 |
8000件 |
150000件 |
1775% |
缺陷漏检率 |
0.12% |
0.002% |
98.3% |
质量追溯效率 |
48小时 |
15分钟 |
99.5% |
检测人力成本 |
280万元/年 |
75万元/年 |
73.2% |
五、未来展望:当三维扫描遇见工业元宇宙
随着5G+工业互联网的深度融合,三维扫描技术正开启新的想象空间:
- 数字孪生:某飞机发动机厂商已实现扫描数据直接驱动加工补偿,使装配精度提升40%
- AI质检:深度学习算法对复杂缺陷的识别准确率突破99.5%大关
- 绿色制造:某光伏企业通过扫描数据优化切割路径,每年减少硅料浪费120吨
正如中国工程院院士周济在2023智能制造大会上强调:"三维扫描相机不仅是检测工具,更是制造业数字化转型的核心使能技术。它正在重构从产品设计到售后服务的全价值链。"
结语从危机重重的质量困境,到游刃有余的智能检测,三维扫描相机的进化史正是中国制造转型升级的微观缩影。当每个细微特征都被精准捕捉,当每次检测都转化为数据资产,我们看到的不仅是技术参数的提升,更是一个产业走向高质量发展的坚定步伐。在这条创新之路上,三维扫描技术将继续扮演"工业之眼"的关键角色,见证并推动着智能制造时代的全面到来。