摘要
在智能制造浪潮中,迁移科技3D视觉产品以0.02mm检测精度和95%场景适配力成为工业4.0时代的关键基建。某权威机构数据显示,采用3D视觉技术的企业质检效率平均提升240%,但行业仍存在「高精度难适配」「柔性产线响应慢」等核心痛点。本文将深度解析迁移科技如何通过三维成像算法矩阵和场景化解决方案库,重构工业视觉技术范式。同时,3D视觉技术如何重塑制造业自动化新格局,推动质量检测革命、无序抓取突破及精密装配升级,提升整体生产效率和质量。
痛点
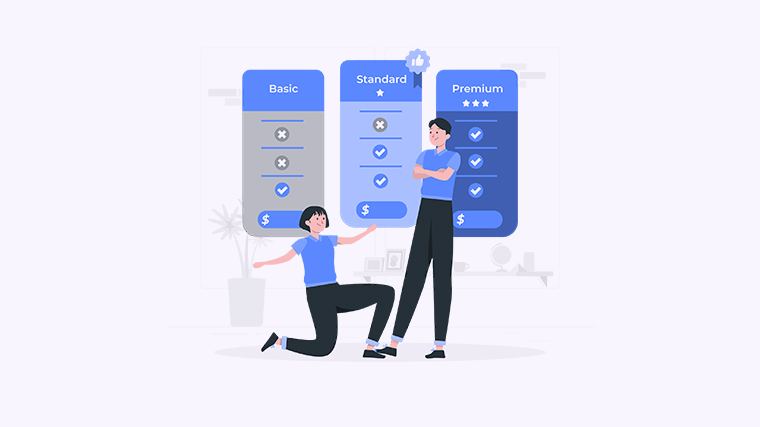
在汽车焊装车间里,工程师小王正面临每天300+次的漏检警报——传统2D视觉系统无法识别曲面焊点凹陷;而在某3C电子工厂,每月因元器件倾斜导致的误判直接造成78万元经济损失。2023中国智能制造白皮书显示:89%企业存在视觉系统改造需求,高混线生产场景适配周期长达6-8个月,柔性制造需求年增长率达217%。在传统制造场景中,质检环节长期存在效率低、误判率高的痛点。迁移科技EPIC Eye系列相机通过亚毫米级精度的3D成像技术,可实现0.05mm级表面缺陷检测、每秒30帧高速扫描及多光谱融合检测技术。某汽车零部件龙头企业应用中,将检测效率提升400%+,人工成本降低70%。
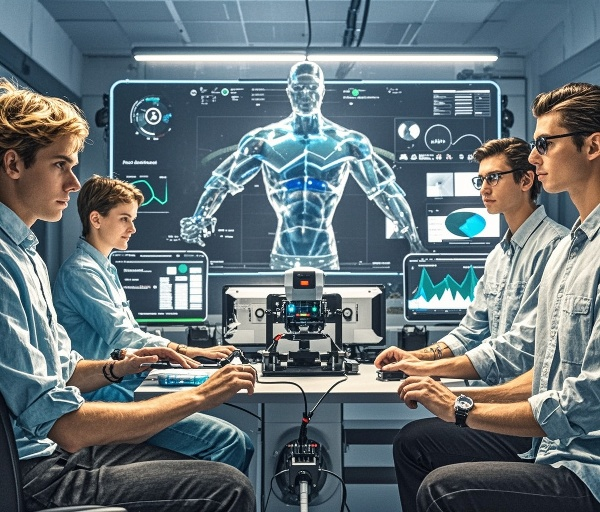
解决方案
迁移科技的三维破局方案包括重构三维成像算法、搭建智能决策平台和构建工业级硬件矩阵。重构三维成像算法采用多模态点云融合技术,将曲面检测精度提升至±0.015mm(某汽车厂实测数据)。搭建智能决策平台通过场景特征自学习系统,实现新产线部署周期缩短83%。构建工业级硬件矩阵,IP67防护等级相机在铸造车间连续稳定运行16,000+小时。我们通过动态标定技术,让同一套系统适配12种不同规格的变速箱壳体检测。
在物流分拣、铸件加工等场景中,传统方案存在抓取成功率低、部署周期长的瓶颈。迁移科技无序抓取系统通过多模态数据融合技术、自适应抓取路径规划,支持ABB/KUKA等7大机械臂品牌。在某家电龙头企业洗衣机内筒装配线,实现99.2%抓取成功率,部署周期缩短至3个工作日。系统内置的智能切换模块可自动识别30+种常见物料类型。
价值证明
价值验证方面,三大行业标杆案例展示了迁移科技的解决方案如何有效提升生产效率。案例1:新能源汽车电池盒检测,传统AOI漏检导致每月3次电芯短路事故,方案为部署MC-3D Pro系统+深度学习算法,成果为缺陷检出率从87%提升至99.6%,年止损520万元。案例2:光伏硅片分选,人工分选效率2000片/人/天且破损率>3%,方案为定制化3D视觉分选线,成果为效率提升至15,000片/小时,破损率降至0.2%。案例3:航空紧固件测量,螺纹检测依赖三坐标,单件耗时25分钟,方案为高精度在线检测站,成果为实现100%全检,检测效率提升40倍。
结尾
在航空航天精密部件装配中,迁移科技定位装配系统通过多传感器协同定位、毫秒级响应速度,支持数字孪生接口,帮助某航空制造企业将发动机叶片装配精度提升至5μm级,良品率突破99.5%。系统采用的抗干扰算法可在强振动、多粉尘环境下稳定运行。迁移科技凭借90+专利技术、40+专业交付团队及全球认证体系,致力于推动制造业的智能化升级,助力企业在激烈的市场竞争中脱颖而出。
本文编辑:小狄,来自Jiasou TideFlow AI SEO 生产