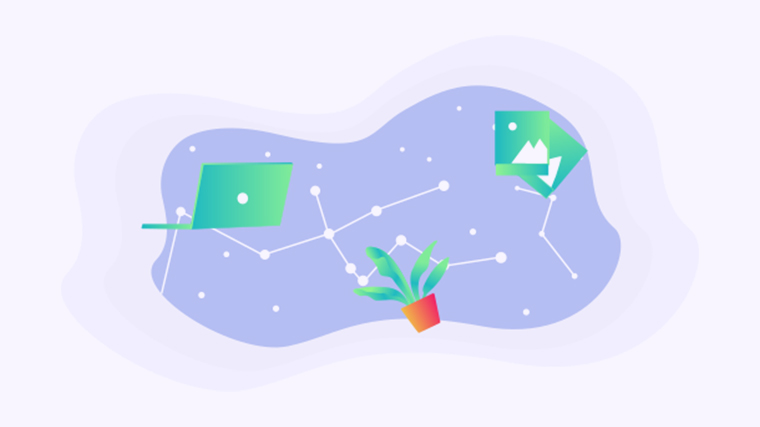
20世纪70年代以来,以计算机信息技术为基础的高新技术得到迅猛发展,这也为传统的制造业提供了新的发展机遇,意味着
传统制造业将要更新换代。计算机技术、信息技术、自动化技术等与传统制造技术相结合,形成了先进制造技术概念,它已越来越受到世界各工业化国家的重视,人们对它的内涵的认识也越来越清晰。
我国当前先进制造技术的应用 先进制造技术已在我国得到了广泛的使用,下面介绍应用比较成熟的先进制造技术。 计算机辅助设计技术(CAD)。进入20世纪90年代之后,CAD技术走上了商品化、产业化和全面推广应用的新阶段。应用CAD技术已成为提高市场应变能力和技术创新能力的重要手段。 精密成型技术。精密铸造技术重点发展了熔模精密制造、陶瓷型精密铸造、金属型铸造、消失模铸造等技术。精密塑性成型技术重点发展了精冲技术、超塑成型技术、冷挤压技术和成型轧制等技术。 超精密加工技术。我国超精密加工技术起步较早,但直到20世纪80年代才取得了较大发展。 数控技术。我国数控技术经过1981-1985年的技术引进、1986-1990年的消化吸收和1991-1995年开发自主版权的数控系统3个阶段的发展,已建立了2个具有自主版权的数控平台,即以PC机为基础的总线式、模块化、开放型中处理器平台和多处理器平台。开发出了4个具有自主版权的基本系统:中华Ⅰ型、航天Ⅰ型、蓝天Ⅰ型、华中Ⅰ型。并在此基础上开发了数控车床和加工中心6个电信系统及针对数控磨齿机、电加工
机床、三坐标测量机等特定功能要求的16种派生系列,这就为我国实现数控
机床的产业化奠定了基础。 计算机集成制造(CIMS)。计算机集成制造研究范围覆盖了系统集成技术、CAD/CAM、管理决策信息系统、质量系统工程和数据库等,开展了系列关键技术的研究,包括复杂工业系统的模拟设计、异构环境的信息集成,基于STEP的CAD/CAM集成系统、并行工程构架和应用集成平台。 分散网络化制造(DNM)。生产在地域上的分散性,要求分散网络化制造。建立分散网络化制造系统,可以推出更高质量、更低成本的新产品,综合利用不同企业的现有设计能力和制造资源,把它们迅速组合成为一种没有围墙的、超越时空约束的、靠信息传输手段联系的、统一指挥的经营实体。
先进制造技术的发展趋势 近二三十年先进制造技术的进展和未来的发展趋势主要有如下几个方面:1.常规制造工艺的优化,保持原有工艺原理不变,通过改善工艺条件,优化工艺参数来实现。2.新型加工方法的发展,新能源的引入、新型材料的应用、产品特殊功能的要求等都促进了新型加工方法的形成与发展,如激光加工技术、电磁加工技术、超塑加工技术以及复合加工技术等。3.专业、学科间的界限逐渐淡化、消失,在制造技术内部冷热加工之间,加工过程、检测过程、物流过程、装配过程之间,设计、材料应用、加工制造之间,其界限均逐渐淡化,逐渐走向一体化。4.工艺设计由经验走向定量分析。5.信息技术、管理技术与工艺技术紧密结合。微电子、计算机、自动化技术与传统工艺及设备相结合,形成多项制造自动化单元技术,经局部或系统集成后,形成了不同档次的自动化制造技术系统,使传统工艺产生显著、本质的变化,极大地提高了生产效率和产品质量。
数字化制造是先进制造的核心技术 随着信息时代的来临,全球进入了数字化时代。数字化时代的主要特征是数字化技术在生产、生活、经济、社会、科技、文化、教育和国防等各个领域的应用不断扩大并取得日益显著的效益。 数字化技术和各种专业技术相融合形成了各种数字化专业技术,如数字化制造技术、数字化设计技术、数字化视听技术。相对传统的制造技术,数字化制造技术是一项融合数字化技术和制造技术,且以制造工程学为理论基础的重大的制造技术革新,是先进制造技术的核心,有广阔的应用前景。 数字化制造是在计算机网络技术与制造技术不断融合、发展和应用的基础上诞生的,其内涵为:以CAD/CAM/CAE为一体的技术,以MRP、MIS、PDM为主体的制造信息支持系统,数字控制制造技术。
数字化制造包括以下几个关键技术: 制造过程的
建模与仿真。制造过程的
建模与仿真是在计算机上用解析或数值的方法表达或建模制造过程,建模通常基于制造工艺本身的物理和化学知识,并为实验所验证。目前,仿真与建模已成为推进制造过程设计、优化和控制的有效手段。仿真和建模最重要的工作是优化工艺参数以确保用最高的质量价格比制造符合设计要求的零件。 网络化敏捷设计与制造。利用快速发展的网络技术,提高企业对市场的响应速度。美国企业已经开始应用这项技术并取得了明显的效益。我国企业技术与国际接轨就必须在此领域开展研究。 网络化敏捷设计与制造重点发展领域应包括:敏捷信息基础结构(合作企业模型,中国企业信息基础结构及其标准,跨企业的敏捷设计与制造的信息基础结构及其集成方法,基于供应商的设计与制造,面向设计的合作支持技术,跨企业合作管理技术和使能技术),敏捷产品设计技术,敏捷工艺设计技术,基于网络的研究开发,敏捷生产技术。 虚拟产品开发。虚拟产品开发有四个核心要素:数字化产品和过程模型、产品信息管理、高性能计算与通信、组织/管理的改变。