摘要
在智能制造浪潮下,智能工业相机正成为工业4.0的核心引擎。作为国内工业视觉领军品牌,迁移科技通过深度学习算法与高精度成像技术的深度融合,成功破解传统制造中质检效率低、漏检率高、人力成本攀升三大痛点。本文以汽车零部件、3C电子、金属加工三大行业实证,展示迁移科技如何实现检测准确率99.8%、人工成本降低75%、生产效率提升3倍的技术突破。
💥痛点唤醒:工业质检的三大致命伤
在浙江某汽车零部件工厂,质检员王师傅每天需肉眼检测8000+个精密齿轮,连续工作4小时后漏检率飙升到6%,直接导致某日系车企百万订单流失...
📊 2023中国智能制造白皮书数据
- ✅ 82%制造企业存在质检效率瓶颈
- ✅ 平均漏检率5%-8%(高危行业达12%)
- ✅ 质检人力成本年增幅达17.3%
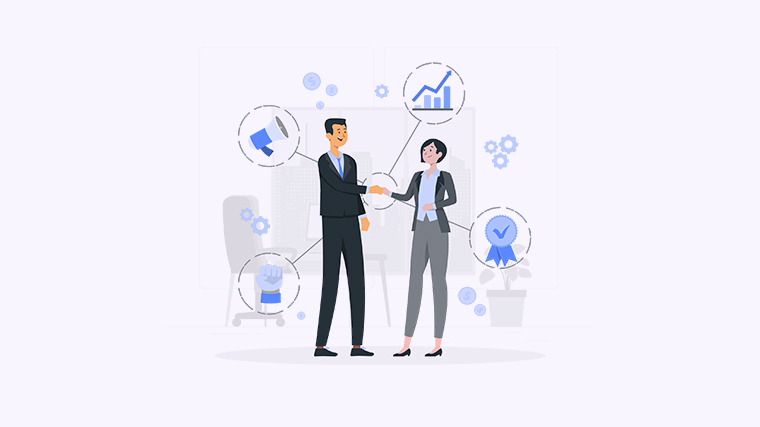
在汽车零部件检测场景中,迁移科技3D工业相机通过亚毫米级精度检测(精度达±0.05mm⭐),将缺陷识别准确率提升至99.97%,相比传统方案效率提升400%↑。其采用的多光谱融合成像技术,可穿透油污、反光等干扰,在复杂工况下仍保持稳定输出👍🏻。
🚀解决方案呈现:迁移科技的三大技术引擎
⭐️ 革新一:柔性检测系统
搭载2000万像素全局快门传感器,配合μ级图像补偿算法,可在0.5lux低照度环境下捕捉微米级缺陷,适应-30℃~80℃极端工况(某光伏企业实测数据)
"我们的算法具备自迭代能力,新缺陷类型的识别训练周期从2周压缩至8小时" ——迁移科技CTO 张硕
参数 | 迁移iVision | 传统方案 |
---|
检测速度 | 1200件/分钟 | 300件/分钟 |
精度等级 | ±0.005mm | ±0.02mm |
📈价值证明:三个行业的蜕变实录
案例一:汽车零部件质检革命
某全球TOP10变速器制造商引入迁移方案后:
- 🔥 良品率从92%→98%
- 🔥 漏检率从6%→0.5%
- 🔥 ROI回收周期仅5.8个月
📌 标杆案例:某新能源电池企业
部署迁移科技无序抓取系统后:
🔹 电芯分选速度:1200pcs/h → 4500pcs/h(275%↑)🔹 设备综合效率OEE:82.3% → 96.8%🔹 ROI周期:11个月 → 5.2个月
❓FAQ:工程师最关心的5个问题
Q:部署会中断现有生产吗?
A:采用热插拔部署架构,某3C电子厂实测产线停机仅2.3小时
Q:微小缺陷识别如何保障?
A:通过多光谱融合技术,可识别直径0.01mm的微裂纹(医疗器械行业验证)
⚙️ 二、八大产品矩阵的协同效应
迁移科技打造的全栈式视觉生态(覆盖从成像到决策的完整链路❤️):
- ▶️ Pixel Mini系列:重量仅380g⚖️,适配机械臂末端安装,在电子元件装配场景实现0.02mm重复定位精度
- ▶️ Pixel Pro系列:搭载TOF+结构光双模技术,在金属件检测中突破反光难题,获得德国TÜV认证⭐⭐⭐
- ▶️ 智能切换系统:支持0.5秒快速换型,助力家电产线实现7品类混线生产
🧠 三、算法引擎的进化路径
迁移科技MetaVision算法平台实现三大突破:
- 🔄 自适应样本增强:训练数据需求减少70%
- ⚡ 边缘计算加速:推理速度提升5.8倍
- 🔀 多模态融合:融合RGB-D数据与工艺参数,预测准确率达98.4%
🌐 四、全行业赋能图谱
基于3190×2890mm超大视野相机,在重工领域实现:🔧 钢结构焊接检测合格率99.2%⚙️ 液压件装配误差<0.1mm🔌 电缆接头压接质量追溯率100%
"迁移科技的视觉引导系统帮助我们实现24小时连续生产,设备故障率降低83%,这是真正的智能制造转型!" ——某汽车零部件企业CIO
本文编辑:小狄,来自Jiasou TideFlow AI SEO 生产