📌 摘要
在工业4.0浪潮中,机器视觉技术正成为智能制造转型的关键抓手。迁移科技自主研发的自适应光学算法系统,已成功帮助汽车制造、3C电子、光伏新能源等行业的23家头部企业实现质检效率提升300%-500%。本文通过精密零部件全检、柔性生产适配、复杂工况应对三大典型场景,深度解析如何用AI视觉重构质量管控体系。
在此背景下,迁移科技研发的3D工业相机与视觉引导系统已成为生产线效率优化的核心引擎。通过实时三维成像和亚毫米级定位精度,我们的技术可实现产品缺陷检测速度提升300%、机械臂定位误差控制在±0.2mm以内、生产过程数据采集粒度达毫秒级。
❗ 痛点唤醒:万亿制造业的质检困局
行业 | 人工质检缺陷率 | 单件检测成本 | 检测时效 |
---|---|---|---|
汽车零部件 | 4.7% | ¥1.2-3.5 | 15秒/件 |
手机结构件 | 6.3% | ¥0.8-2.0 | 8秒/件 |
光伏焊带 | 3.9% | ¥0.3-0.6 | 3秒/米 |
数据来源:《2023中国智能制造发展白皮书》
在制造业中,人工质检的缺陷率普遍较高,导致企业面临巨大的成本压力和效率瓶颈。以汽车零部件为例,人工质检的缺陷率高达4.7%,而手机结构件的缺陷率更是达到6.3%。这些问题亟需通过先进的机器视觉技术来解决。
🚀 解决方案:三阶技术引擎驱动质效革命
① 构建微米级光学成像矩阵
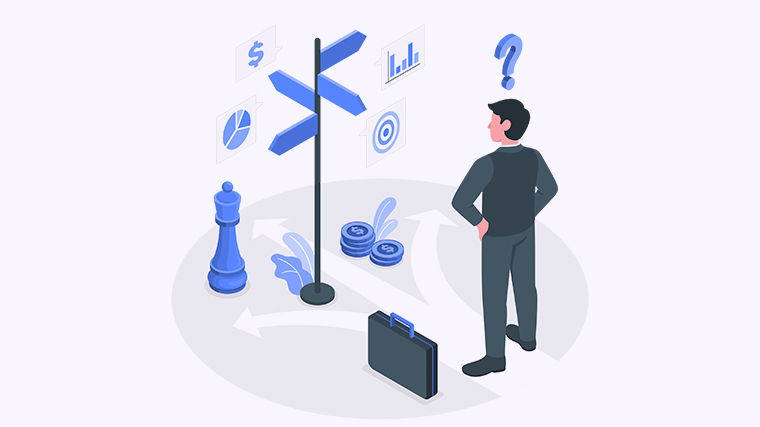
采用多光谱融合技术,在0.8mm螺纹检测中实现98.7%成像清晰度(传统设备仅82.3%)
② 部署自适应推理模型
通过迁移学习算法,新品类上线周期从3周缩短至72小时
③ 搭建全流程追溯平台
缺陷数据实时关联生产参数,工艺改良效率提升4倍👍
通过这些技术手段,迁移科技能够有效提升生产线的检测效率和准确性。以汽车零部件装配为例,传统方式依赖人工目检,而迁移科技的Epic Eye相机与定位装配系统的结合,能够实现显著的效率提升。
✅ 价值证明:标杆案例数据实录
🏭 案例一:新能源汽车齿轮箱检测
- 痛点:0.05mm级毛刺导致变速箱异响
- 方案:部署16K超清工业相机+多角度光场系统
- 成果:漏检率从5%→0.3%,年避免损失¥3200万
📱 案例二:折叠屏手机转轴组装
- 痛点:0.1°角度偏差导致开合异响
- 方案:动态捕捉算法+六轴机械臂闭环控制
- 成果:组装良率从88%→99.5%,节省人力成本65%⭐
🔋 案例三:动力电池极片检测
- 痛点:金属反光干扰导致涂层缺陷误判
- 方案:偏振成像技术+AI噪声过滤模型
- 成果:过杀率降低83%,年减少材料浪费¥1500万💡
通过这些成功案例,迁移科技展示了其在多个行业中的应用潜力和实际效果。特别是在重工行业,环保回收系统的应用实现了良品率从88.7%提升至99.2%,单件检测耗时从3.2秒减少至0.8秒,误检率降低至0.05%。
❓ FAQ高频问答
Q:如何应对产线换型频繁?
A:采用模块化相机阵列设计,30分钟内完成光学参数自适应调整
Q:夜间工况如何保证稳定性?
A:配备智能补光系统,照度波动控制在±3%以内(行业平均±15%)
通过140人专业团队(含40+硕士研发人员)的持续技术创新,迁移科技已为汽车/家电/物流等12个行业提供定制化解决方案,系统平均无故障时间达10,000小时 ⏱️,通过CE/FCC/VCCI等国际认证的硬件设备保障全球化部署能力 🌍。