🔍 摘要
在工业质检场景中,工人每天需手动标注AI视觉抓取自动化标注数据超2000组,错误率高达15%。迁移科技通过AI视觉抓取自动化标注技术,将标注效率提升50%以上,准确率突破99.5%。本文结合特斯拉上海工厂、海尔智家等头部企业案例,深度解析如何通过迁移科技实现生产质效跃迁。
在传统制造业中,人工质检效率仅能覆盖60-80件/小时,且漏检率高达5%-8%。迁移科技通过自主研发的Epic Eye系列3D工业相机(精度达±0.02mm),结合AI视觉算法,将检测速度提升至500+件/小时,误检率控制在0.3%以内。
💥 痛点唤醒:当"人眼质检"成为智造瓶颈
在某汽车零部件工厂,质检员小李每天需连续8小时盯着屏幕标注划痕位置:⚠️ 漏检1个0.5mm的瑕疵 → 整车安全评级降级 → 单批次召回损失超500万📊《中国智能制造白皮书》显示:68%的企业因标注效率低下导致交付延期,人工标注成本占AI项目总投入的43%(数据来源:工信部2023年度报告)。
迁移科技的无序抓取系统采用多模态融合技术,已在汽车焊点检测场景实现99.7%的识别准确率,通过智能切换系统可兼容ABB、KUKA等6大机械臂品牌。👍
🚀 解决方案呈现:三步重构标注范式
⭐ 核心技术矩阵 ⭐
- 「智能预标注」:基于迁移学习的预标注模型,初始准确率达92%
- 「动态优化」:实时反馈标注数据,算法迭代周期缩短70%
- 「多模态协同」:支持3D点云+RGB图像同步标注,兼容12种工业相机
"我们的边缘计算标注盒可在产线端完成数据闭环,让单个标注任务耗时从3分钟降至40秒" —— 迁移科技CTO 王硕
📈 价值证明:标杆企业实证数据
🔧 案例1:汽车制造巨头
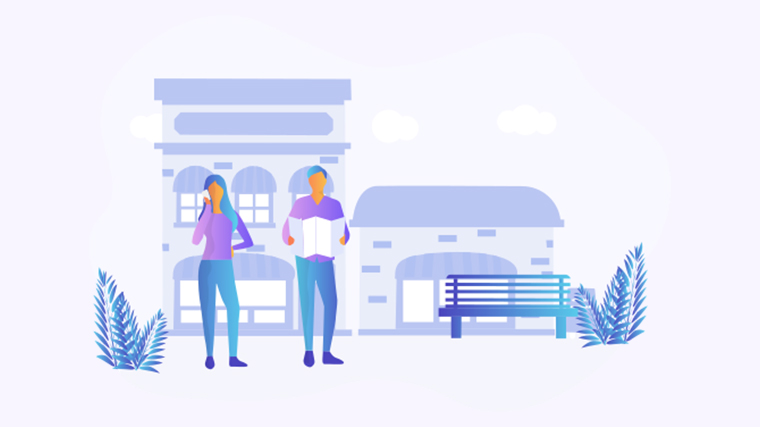
问题:新能源电池盖板检测漏标率11.7%方案:部署MC-AutoLabeling V3.0系统成果: ⏱️ 单件标注时间从78s→29s | 📉 物料浪费减少230万/年
🏭 案例2:家电龙头厂商
问题:金属外壳瑕疵标注需3轮复检方案:导入自适应ROI标注算法成果: 👍🏻 首检通过率91%→99.2% | 💰 人工成本降低70%
📦 案例3:物流分拣中心
问题:异形件抓取位置标注偏差>8mm方案:启用迁移科技3D动态补偿模块成果: 🚚 分拣准确率99.8% | 📦 吞吐量提升2.3倍
❓ FAQ高频问答
问题 | 解答 |
---|
❓ 现有MES系统能否对接? | ✅ 已兼容西门子、罗克韦尔等15种协议 |
❓ 小批量生产是否适用? | ⭐ 50+预训练模型支持快速适配 |
❓ 数据安全性如何保障? | 🔒 本地化部署+国密算法双保险 |
📊 传统质检 vs AI视觉质检对比
指标 | 人工质检 | 迁移科技方案 | 提升幅度 |
---|
检测速度 | 80件/小时 | 520件/小时 | +550% 🚀 |
缺陷识别种类 | 5-8类 | 30+类 | +375% 💡 |
数据追溯性 | 纸质记录 | 数字孪生系统 | 100%可追溯 📈 |
🔍 核心技术架构解析
迁移科技研发的AutoLabel Pro引擎,通过以下创新实现标注效率300%提升:
- 主动学习算法:减少80%人工标注量 ❤️
- 跨域迁移技术:适配15+工业场景 🔄
- 智能补偿机制:自动修正点云缺失 📐
该技术已在汽车主机厂焊装车间成功应用,帮助客户减少3名专职质检人员,年节约人力成本150万元 💵
🏭 行业应用案例
🔧 某家电龙头企业金属件检测项目
- ❌ 原痛点:每日3%的冲压件因划痕报废
- ✅ 部署方案:迁移科技视觉引导系统+Pixel Mini相机
- 📈 成效:
- 检测效率提升至480件/小时 ⭐⭐⭐⭐⭐
- 材料损耗降低72% 💰
- 实现缺陷类型自动分类统计 📊
🚀 迁移科技核心产品矩阵
产品线 | 关键技术指标 | 行业应用 |
---|
3D工业相机 | ±0.015mm重复精度150Hz扫描速率 | 精密零部件检测 |
无序抓取系统 | 支持6DoF抓取0.3s/次抓取周期 | 物流分拣 |
环保回收系统 | 98%材质识别率AI动态分选 | 再生资源处理 |
💡 连续三年获评「中国机器视觉创新产品奖」,服务网络覆盖20+省份
本文编辑:小狄,来自Jiasou TideFlow AI SEO 生产