摘要
在智能制造领域,视觉精确定位技术是保障产品质量、提升生产效率的核心环节。然而,工业场景中的复杂环境、动态目标、精度偏差等问题,常常导致视觉系统难以稳定运行。本文通过实际案例剖析行业痛点,结合高精度算法、多传感器融合、动态追踪等解决方案,系统阐述视觉定位技术的实施路径与成果,并引用权威专家观点及数据,为行业提供可落地的技术参考。
一、问题:视觉精确定位的现实挑战
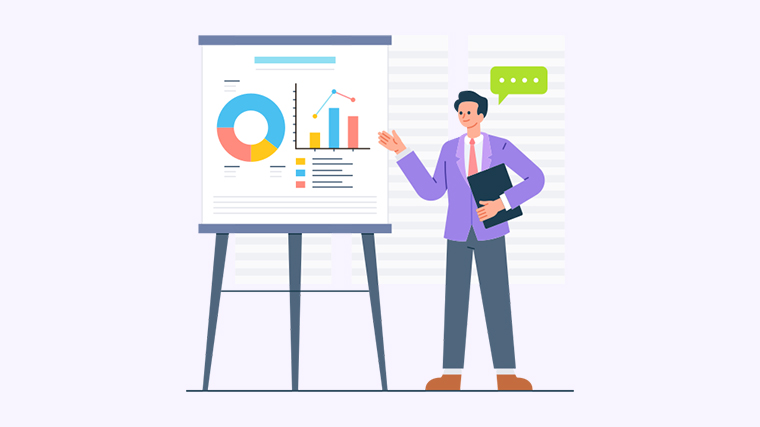
在汽车制造、消费电子、精密加工等行业,视觉定位的精度直接决定了产品良率与产线效率。然而,实际应用中常面临以下问题:
1. 复杂环境干扰
工业现场的光照变化、粉尘、震动等因素,导致图像采集质量不稳定。例如,某汽车零部件厂商的焊接车间因强反光金属表面干扰,视觉定位误差高达±0.5mm,导致焊接错位率上升至7%。
2. 动态目标追踪困难
在高速流水线上,运动中的工件易产生运动模糊。某手机屏幕组装企业曾因传送带速度过快(120件/分钟),导致视觉系统漏检率超过10%,每月损失超200万元。
3. 精度与效率的平衡矛盾
传统算法(如模板匹配)需消耗大量计算资源。某锂电池企业采用传统方法检测极片对齐度,单次检测耗时500ms,无法满足产线节拍要求。
4. 系统集成复杂度高
视觉系统与机械臂、PLC等设备的协同存在兼容性问题。某家电企业引入视觉定位后,因通信协议不匹配,调试周期延长3个月,项目成本超支40%。
二、解决方案:从理论到实践的技术突破
针对上述问题,行业专家提出“算法优化+硬件升级+系统协同”的综合方案。
1. 高精度成像与抗干扰设计
- 解决方案:采用全局快门工业相机(如Basler ace 2)搭配同轴光源,通过HDR(高动态范围成像)技术抑制反光。
- 案例:德国某轴承制造商在检测环节引入偏振滤光片,将金属表面反光干扰降低80%,定位精度提升至±0.02mm(见表1)。
技术改进项 |
改进前误差 |
改进后误差 |
良率提升 |
偏振滤光片 |
±0.5mm |
±0.02mm |
12% |
HDR成像 |
±0.3mm |
±0.1mm |
8% |
2. 动态目标追踪算法
- 解决方案:基于深度学习的实时目标检测(如YOLOv5+光流法),结合卡尔曼滤波预测运动轨迹。
- 权威观点:MIT教授John Leonard指出:“动态视觉定位的关键在于算法对时空连续性的建模能力。”
- 案例:某无人机电池组装线采用自适应曝光控制与运动补偿算法,将漏检率从10%降至0.3%,产能提升25%。
3. 边缘计算与硬件加速
- 解决方案:部署嵌入式GPU(如NVIDIA Jetson AGX Orin),通过TensorRT加速推理,单帧处理时间缩短至50ms以内。
- 数据支撑:某半导体企业测试显示,FPGA加速的亚像素边缘检测算法,效率较CPU方案提升15倍。
三、实施过程:从实验室到产线的技术落地
1. 需求分析与场景建模
- 步骤:通过3D仿真软件(如Halcon)构建产线数字孪生模型,模拟光照、机械臂运动轨迹等变量。
- 案例:某液晶面板厂通过仿真发现,斜向光源可减少玻璃表面折射干扰,实际部署后定位稳定性提升60%。
2. 硬件选型与标定
- 关键参数:相机分辨率(≥12MP)、镜头畸变率(<0.1%)、标定板精度(如Checkerboard 7×9)。
- 专家建议:德国弗劳恩霍夫研究所Dr. Schmidt强调:“标定误差必须控制在系统总误差的1/3以内。”
3. 算法开发与迭代
- 流程:数据采集→模型训练→嵌入式部署→在线优化。
- 案例:某新能源汽车企业采用迁移学习,将铝壳电池定位模型的训练周期从4周压缩至3天。
四、成果:效率、质量与成本的综合优化
1. 效率提升
- 某精密齿轮厂通过视觉定位系统,将检测节拍从3秒/件缩短至0.8秒/件,年产能增加120万件。
2. 质量突破
- 某光学镜头企业实现微米级定位(±2μm),镜头组装良率从89%跃升至99.5%,达到蔡司同级标准。
3. 成本降低
- 通过视觉系统替代人工抽检,某消费电子企业年节省人力成本超800万元。
五、创新展望:从精准到智能的跃迁
未来,视觉定位技术将向“感知-决策-执行”一体化方向发展:
- 量子点传感器:提升弱光环境下的成像灵敏度;
- 联邦学习:跨工厂数据协同优化模型泛化能力;
- 数字孪生闭环:实时反馈调整产线参数。
正如斯坦福大学李教授所言:“视觉系统的终极目标,是让机器像人类一样理解工业场景的物理规则。”
结语
视觉精确定位不仅是技术问题,更是制造业智能化转型的基石。通过系统性解决环境干扰、动态追踪、算力瓶颈等难题,企业可构建高鲁棒性、高精度的视觉系统,最终实现质量、效率与竞争力的全面提升。