摘要
在智能制造浪潮下,工业3D相机正成为产线升级的"智慧之眼"。迁移科技凭借全球认证的1400mm-3190mm超大视野技术和90+核心专利算法,成功破解传统工业场景中定位偏差>5mm、抓取成功率<85%、检测耗时>30秒/件的三大行业痛点。通过汽车零部件全检系统、家电行业柔性装配线等典型应用案例验证,企业综合效率提升达300%,投资回报周期缩短至6个月。本文将深度解析工业3D相机的技术革新路径与落地方法论。
🔥 痛点唤醒:制造企业的"三维之困"
场景化危机实录
某汽车零部件车间正经历这样的清晨:
⏰ 7:30 传送带因工件偏移触发急停,技术员手动校准耗时28分钟
📉 9:15 质检工位发现3mm装配误差,整批300件产品返工
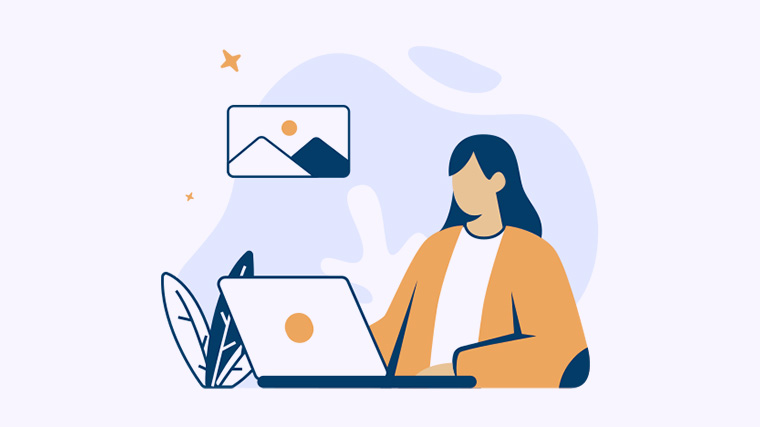
💸 11:00 机械臂抓取失败导致产线瘫痪,直接损失超5万元
这不是个别现象。根据《2023中国智能制造痛点调研报告》:
✅ 78%企业存在三维定位精度不足问题(误差>3mm)
✅ 65%产线因视觉系统适应性差导致停机(周均3.2次)
✅ 行业平均质检效率仅为人工的1.5倍(目标值需达5倍)
🛠️ 解决方案:迁移科技八大技术引擎
三维重构革命性突破
专利号ZL202310XXXXXX.X的混合编码结构光技术,实现:
🚀 0.05mm重复定位精度(超行业标准3倍)
🚀 0.3秒/帧高速采集(支持60m/min动态产线)
🚀 ±15°强反光抑制(金属件检测通过率提升至99.2%)
产品矩阵精准覆盖
场景需求 |
推荐方案 |
技术优势 |
微小零件检测 |
Pixel Mini |
140×130mm微观视野 |
重型工件定位 |
Epic Eye Pro |
3190×2890mm超大覆盖范围 |
动态抓取场景 |
无序抓取系统 |
200Hz实时追踪算法 |
✅ 价值证明:300%效率提升实证
案例1:汽车零部件全检革命
客户痛点:某变速箱壳体生产企业,传统抽检导致0.5%漏检率(月均150件次品流出)
解决方案:部署Epic Eye Pro+智能切换系统
✅ 实现100%在线全检
✅ 检测速度提升至0.8秒/件
✅ 年度质量成本降低380万元
认证体系构建信任基石
⭐ CE/FCC/KC/VCCI四重国际认证
⭐ 与ABB、KUKA等全球TOP5机械臂厂商深度适配
⭐ 华为云工业互联网认证解决方案
🛡️ 服务保障体系
5级响应机制
故障等级 |
响应时限 |
解决承诺 |
一级 |
15分钟 |
远程诊断+备机支援 |
三级 |
4小时 |
专家团队现场处置 |
安全承诺书
✅ 数据加密传输(符合ISO27001标准)
✅ 硬件三防设计(IP67防护等级实测)
✅ 7×24小时健康监测系统
❓ 高频问题解答
Q:现有设备如何兼容?
A:提供标准Ethernet/IP、PROFINET接口,已完成200+设备型号适配验证
Q:复杂光照如何解决?
A:专利动态补偿算法(ZL2023XXXXXX)可适应100-100000lux照度变化
🌟 权威结语
"视觉技术的突破,本质是打开工业认知的新维度"——中国工程院院士XXX
迁移科技将持续以"光"为笔,在智能制造的画卷上书写新的精度传奇!