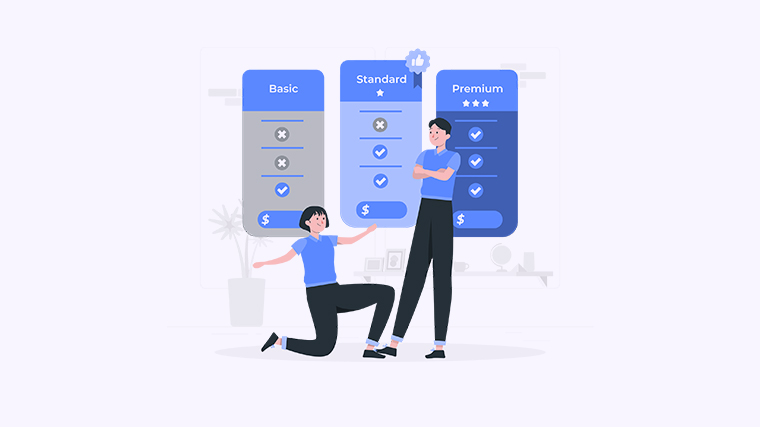
光阳集团为节能减排,提高生产效率,对耗能大、排污超标严重的锻造加热工艺实现彻底变革,淘汰锻造车间所有燃煤炉窑,积极采用当代先进技术,引进安装两座国内先进的环保全煤气发生炉和建造四座燃煤气炉窑,并已于8月初点火开工正式投入使用。经一个多月的运行,新煤气发生炉技术性能安全可靠,节能减排效果明显,排污指标大大低于国家规定标准。
光阳集团前身——华丰锻压厂,创立于1993年,专业加工轴承套圈锻件,一直使用燃煤炉窑加热套圈棒料,不仅浪费燃料,而且排污严重超标,对自然生态环境和生产生活环境造成严重危害,近几年,虽几经改造,但仍未从根本上改变排污超标状况,炉窑排放的有毒有害气体严重侵害工人的身体健康;浓重的黑烟粉尘致使在几米内相互不见人,严重的影响车间安全生产;甚至公司遇有上级环保部门检查,锻造车间不得不关门停产,严重影响公司生产任务的完成。面对这种落后的生产工艺,公司领导转变观念,树立科学发展观,以对国家负责、对子孙后代负责、对员工负责的责任感,采取果断措施,拆除锻造车间所有直接燃煤炉窑,引进安装国内先进的环保型全煤气发生炉,以其当代先进的新设备、新技术、新工艺,推动锻造生产发展。
据了解,公司采用的全煤气发生炉,是在我国目前制造和使用的煤气发生炉基础上,经更新改造而研制成功的最新产品。该产品是以空气和水蒸汽混合为气化剂的煤气发生炉,是一种新型的以煤为原料,煤转气为一体的独立供热燃烧装置,使消烟、除尘、脱硫一步到位,热效率高。用热煤气来代替煤的直接燃烧,改变了传统的加煤及燃烧方式,既节省能源,又减少烟尘对大气的污染,大大降低了劳动强度,提高工作效率,放宽使用煤种,减少运行成本,从根本上解决了黑烟污染问题。
公司采用的煤气发生炉外罩水套,自产蒸汽可直接通入煤气炉做气化剂使用。其工作原理是:煤的气化是原料煤在煤气发生炉内经过复杂的物理和化学反应,生成煤气,排除炉渣的过程。煤通过自动提升斗从炉的顶端进入炉内,气化剂(即空气和蒸汽混合物)从炉底通过纵横布风均匀的炉栅进入炉内,原料煤与气化逆向接触,进行热化学反应。随着煤气炉的正常运行,炉内自然形成渣层、氧化层(火层)、还原层、干馏干燥层、空气层。其中氧化层是气化过程中的重要反映区域之一,主要是进行放热反应;还原层是赤热的二氧化碳、水蒸气与碳表面进行热化学反应生成CO、H2的反应区域,(主要是吸热反应);干馏干燥层主要反应是C+2H2→CH4,同时析出雾状焦油气与煤气组合,使煤气热值得到提高。反应生成混合发生炉煤气,经重力、旋风两级除尘,由主、支管路送到窑、炉前燃烧器。炉窑经开启闸门引风,进行残余气体置换后,点燃煤气,炉窑开始正常加热工作。
该设备密封程度非常好,凡是需密封的部位,全部采用水封,既不透气密封程度高,又安全可靠。顶盖采用两种不同的耐火保温材料。加煤自动提升,采用双种罩加煤,自动水封,达到三次密封,炉底灰盘亦用水密封,每加一斗煤开启电钮转动灰盘排渣一次,保持炉内总高度不变,同时松动渣层,使气化剂均匀布入炉内。
据了解,全煤气发生炉,具有独特的设备装置,换热器装置采取高压喷流辐射方式,充分回收烟道热气量。换热器的回收温度达到300—500度,节能效率达10%—25%。独特的燃烧器为多孔细流、高压热脏煤气燃嘴,是以未经过处理的热脏发生炉煤气为燃料,借助高压喷流辐射式换热器所产生的高温在300—500度的高压热气,以多流股旋向喷出。高压热气与煤气充分混合,使煤气与空气混合均匀,火燃喷射能力强,容易获得均匀的高温燃区,实现钢材快速加热,提高了加热质量,节约了能耗。另外,机修车间又为炉窑制作了自动上料机,既减轻了员工的体力劳动,又缩短炉门开启时间,进一步实现保温节能。
公司采用的煤气发生炉炉膛直径为1.8米,炉膛截面积为2.54平方米,燃料耗量500—700kg/n;煤气产量1500——2100M3/n;煤气热值5020—5670(K)/m3;煤气出口压力Pа≦980;煤气出口温度(℃)400—550。
全煤气发生炉投入使用后,节能减排效果十分明显,经测量,煤气发生炉排放的烟(粉)尘浓度为100Mg/m3、烟气黑度(林格曼级)低于1级,完全优于国家规定标准。对煤炭质量要求不高,而且燃烧充分,节能达10%左右。现在,锻造车间的空气环境得到了根本的改变,几乎见不到烟尘,工人的脸变白了,衣服也干净了,心情也变得更愉悦了。