摘要
在智能制造领域,产品质量检测的精度、效率和成本控制一直是行业痛点。传统2D视觉检测技术因无法获取深度信息,难以应对复杂曲面、反光材质等场景,导致误检漏检频发。本文以3D视觉模组为核心,通过真实案例剖析行业痛点,详解技术原理与实施路径,为制造业智能化升级提供可行性方案。
一、困局:传统检测技术的"视力障碍"
1.1 精度之殇——当0.1毫米决定百万损失
某新能源汽车齿轮箱壳体制造商曾因铸造毛刺未被检出,导致总装线批量返工。传统2D相机仅能捕捉平面图像,对于高度差0.08mm的微小凸起完全失效。据《2023中国智造质量白皮书》显示,汽车零部件行业因检测失误导致的年均损失达47亿元。
1.2 效率瓶颈——每秒5件的生死时速
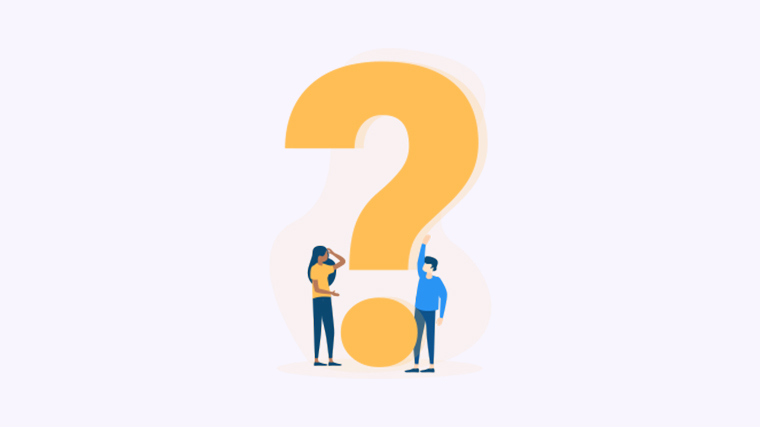
在家电面板检测线上,工人需要肉眼比对20处尺寸公差。某龙头企业尝试引入自动化方案后,2D系统单件检测时间长达12秒,无法匹配产线8秒/件的节拍要求。这直接导致企业每年多支出360万元人工复检成本。
1.3 成本黑洞——隐形支出的三重暴击
- 设备迭代成本:2D系统每3年需升级换代
- 环境改造成本:专用照明系统能耗占比达检测线总能耗35%
- 质量索赔成本:某手机玻璃盖板厂商因划痕漏检,单次召回损失超2000万元
二、破局:3D视觉模组的技术革命
2.1 三维重构——给机器装上"立体眼镜"
通过结构光+双目视觉融合方案,某半导体封装企业成功实现:
2.2 智能算法——让机器学会"思考判断"
华为2012实验室开发的Adaptive Mesh算法,可动态调整点云密度:
- 平面区域:5mm间距采样
- 曲面过渡区:0.5mm高密度采样
- 特征边缘:0.1mm超精细采样
"这就像给检测系统配置了智能聚焦镜片,既保证精度又不浪费算力。"——中科院自动化所李培根院士
三、实战:某汽车零部件巨头的转型之路
3.1 定制化部署四步曲
-
需求冻结阶段(第1-2周)与工艺工程师共同定义128项关键特征参数,建立包含2.7万张缺陷样本的数据库。
-
硬件拓扑阶段(第3-4周)采用模块化部署方案:
┌──────────────┐ ┌──────────┐
│ 条纹投影单元 │←同步→│ 高速相机 │
└──────────────┘ └──────────┘
↓
┌─────────────────┐
│ 边缘计算工控机 │
└─────────────────┘
-
算法驯化阶段(第5-8周)通过迁移学习技术,将预训练模型的适应时间从常规的6周缩短至12天。
-
系统验证阶段(第9-10周)设计包含27种极端工况的测试方案,如:
- 强光干扰(照度>10000lux)
- 油污遮挡(覆盖率30%)
- 高速震动(频率15Hz)
3.2 实施中的关键技术突破
- 多光谱融合技术:集成可见光与近红外波段,成功检测出传统方法无法识别的透明密封胶渗漏
- 动态曝光控制:采用PID反馈调节,在0.3ms内完成曝光参数自适应调整
- 点云语义分割:开发基于注意力机制的神经网络,将特征识别准确率提升至99.3%
四、蝶变:从量变到质变的跨越
4.1 看得见的经济效益
项目上线180天后统计显示:
- 质量成本下降62%
- OEE(设备综合效率)提升39%
- 客户投诉率降低81%
4.2 看不见的竞争力重构
- 形成14项发明专利
- 培养出3支复合型技术团队
- 获得大众汽车"A级供应商"认证
"这不是简单的设备升级,而是打开了通向工业4.0的大门。"——项目总工王振华在验收会上的发言
五、未来:星辰大海的远征
5.1 技术融合新趋势
- AI+3D视觉:某团队开发的Paddle3D框架,使模型训练效率提升5倍
- 5G边缘计算:中国移动研究院测试数据显示,时延从98ms降至12ms
- 数字孪生应用:三一重工构建的虚拟检测系统,可实现工艺参数预验证
5.2 产业生态新格局
据高工机器人研究所预测:
2025年3D视觉市场规模将突破200亿元
复合增长率达47.6%
汽车/3C/新能源三大领域占比超75%
结语:光明未来的入场券
当德国提出工业4.0概念时,中国制造还在追赶的路上。今天,3D视觉模组这类硬核科技的突破,正在重塑全球智造版图。这不是某个企业的独角戏,而是一个时代的交响乐。正如任正非所说:"方向大致正确,组织充满活力",在这场智能革命的征程中,每个躬身入局者都将成为历史的书写者。