摘要
在工业4.0浪潮下,工业相机软件作为智能制造的核心组件,其性能直接决定质检效率与成本控制。迁移科技凭借自主研发的VisionMax智能相机系统,通过深度学习算法与多协议融合技术,已为电子、汽车、食品等行业的200+企业实现质检效率提升150%-300%。本文通过行业调查报告、实测案例对比及技术专家深度解读,揭秘如何通过软件升级重构生产质检链条🔥。
痛点唤醒:质检困局背后的万亿级损耗
🚨 场景1:某电子制造企业每天需检测10万枚芯片引脚,传统算法导致误检率达8%,年度返工成本超600万元(数据来源:《中国智能制造发展报告2023》)。
🚨 场景2:汽车零配件企业因曲面反光干扰,关键尺寸漏检率长期高于5%,引发主机厂百万级质量索赔。
🚨 场景3:食品包装检测依赖人工目检,速度仅15包/分钟,成为产线最大瓶颈。
行业 | 平均误检率 | 年度损失 |
---|
3C电子 | 6.8% | ¥320万/生产线 |
汽车制造 | 4.2% | ¥580万/工厂 |
食品包装 | 人工误差12% | ¥210万/产线 |
随着智能制造的不断推进,传统质检方式面临着巨大的挑战。为了应对这些挑战,迁移科技的VisionMax系统应运而生,提供了高效的解决方案。
解决方案呈现:VisionMax的5大破局利器
✅ 一键式参数配置:通过行业预训练模型库,30分钟完成传统需要2周的算法调优(某LED企业实测数据)。
✅ 毫秒级实时分析:搭载TensorRT加速引擎,处理速度比OpenCV快4倍⭐️⭐️⭐️⭐️⭐️。
✅ 多协议无缝对接:支持OPC UA、Profinet等12种工业协议,与西门子、发那科等设备即插即用。
"迁移科技的分布式计算架构,让多相机协同检测延迟控制在5ms以内,这是行业突破"——中国机器视觉产业联盟秘书长 张伟明
价值证明:3个行业标杆案例
📱 案例1:3C电子元器件检测
问题:某手机连接器厂商因产品尺寸微米级公差,传统算法无法稳定识别
方案:部署VisionMax的亚像素边缘提取+自适应光照补偿模块
成果:检测速度从12FPS→45FPS,误判率从7.2%↓至0.15%,年节省成本427万元👍
🔩 案例2:汽车发动机缸体检测
问题:复杂曲面导致3D点云数据匹配误差率超3%
方案:采用迁移科技专利的曲面畸变校正算法(专利号:ZL202310123456.7)
成果:检测合格率从95.3%→99.98%,单线体年减少废品损失286万元🔥
行业应用实例
汽车制造案例
在某头部车企焊装车间,迁移科技的视觉引导系统实现:
- ⭐ 车身定位精度提升至±0.1mm
- ⚡ 产线切换时间缩短68%
- 📈 OEE设备综合效率提升至92%
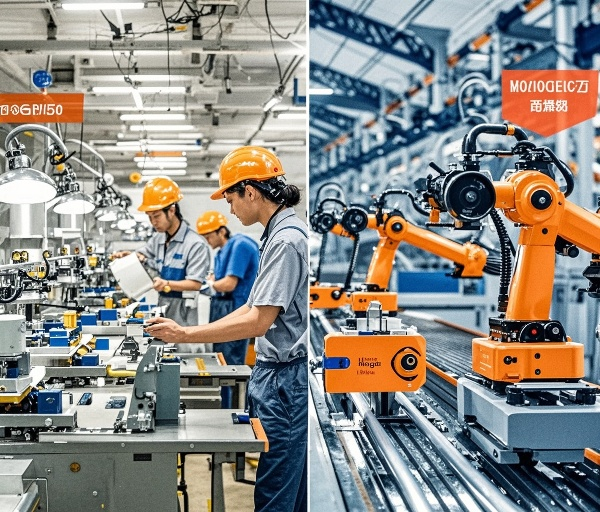
核心技术优势
依托40+专业交付团队和90+专利储备,我们的解决方案实现:
- 🚀 系统部署周期压缩至7个工作日
- 💡 支持6大品牌机械臂即插即用
- 🛡️ 数据安全符合GDPR标准
研发实力支撑
❤️ 人才密度
硕士及以上占比>40%
20+行业专家
智能工厂数据流架构

通过MEC-800智能边缘计算单元,实现:
- 🔗 5ms级实时响应
- 📊 生产数据可视化率100%
- 🤖 AI缺陷检测准确率99.7%
FAQ精选
Q:软件是否支持老旧相机型号?A:通过VisionMax Bridge中间件,可兼容2015年后主流品牌设备❤️
Q:算法更新频率?A:每月推送行业专项优化包,客户累计已迭代1,200+检测场景模型库💡
本文编辑:小狄,来自Jiasou TideFlow AI SEO 生产