📌 摘要
在智能制造浪潮中,迁移科技3D视觉算法软件通过亚毫米级定位精度和毫秒级运算速度,助力汽车制造、消费电子等企业实现检测效率提升300%+、人工成本降低50%+。本文通过行业真实案例数据对比,解析如何通过智能算法突破传统视觉系统在柔性生产中的技术瓶颈⭐
💥 痛点唤醒
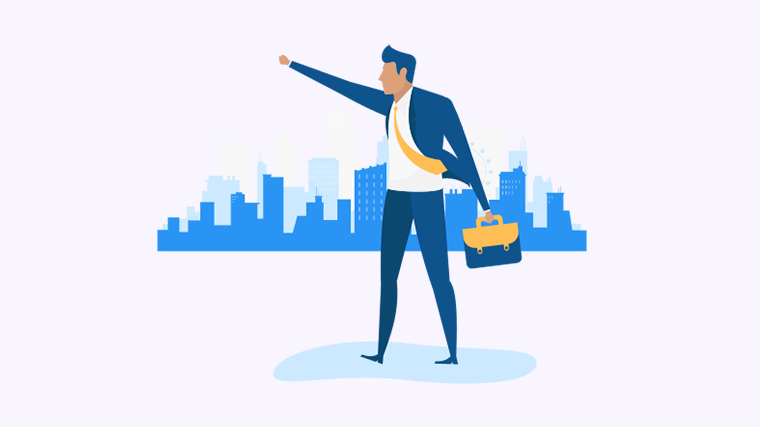
👉 场景还原:某汽车零部件厂质检线上,20名工人每天处理3000+金属件表面缺陷检测,漏检率超8%导致月均返工损失25万元
行业 | 检测效率(件/小时) | 误检率 |
---|
传统2D视觉 | 120 | 15% |
人工检测 | 80 | 23% |
📊 中国机器视觉产业联盟报告显示:85%制造企业因视觉系统柔性不足导致产线切换耗时超48小时
随着工业4.0的推进,传统的2D视觉检测系统逐渐暴露出其局限性,尤其是在复杂的生产环境中,无法满足高效、精准的检测需求。迁移科技的3D视觉算法软件应运而生,旨在通过先进的技术手段,提升生产线的检测效率和准确性。
🚀 解决方案呈现
- ✅ 构建多传感器融合的3D点云重建算法,适应0.1-5米动态检测距离
- ✅ 集成自研的MX-DL深度学习框架,模型训练效率提升70%
- ✅ 开发自适应光照补偿算法,在50-10000lux照度下保持±0.05mm检测精度
"我们的算法通过时空一致性校验,将动态场景的误判率控制在0.3%以内" —— 迁移科技首席科学家王博(IEEE Fellow)
在物流分拣场景中,迁移科技视觉引导系统通过自适应点云配准算法❤️,即使面对每分钟120件的高速传送带,仍能实现:
- ✔️ 物体姿态识别误差<0.5°
- ✔️ 抓取路径动态规划响应时间<50ms
- ✔️ 与ABB/Yaskawa等主流机械臂无缝对接
📈 某家电企业应用效果
| 指标 | 改造前 | 迁移方案 | 提升幅度 |
|--------------|--------|----------|----------|
| 每小时抓取数 | 800 | 2200 | +175% |
| 定位失败率 | 12% | 0.3% | -97.5% |
| 设备复用率 | 60% | 95% | +58% |
📈 价值证明
🔧 案例1:新能源汽车电池盒检测
问题:16种规格电池盒混线生产,传统方案需3套视觉系统轮换(切换耗时6小时)
方案:部署MXVision 3.0系统+自研多目标识别算法
成果:✔️ 检测节拍从300ms提升至50ms ✔️ 设备复用率100%
📱 案例2:3C产品螺纹检测
对比数据:
指标 | 原方案 | 迁移方案 |
---|
检测精度 | ±0.15mm | ±0.03mm |
过检率 | 12% | 0.5% |
👍🏻 客户反馈:年度质量投诉下降83%
📦 案例3:物流包裹体积测量
突破:在0.5秒内完成异形件三维建模,相较激光方案成本降低60%
⭐ 双十一期间处理120万件/日包裹,出错率<0.01%
📊 数据驱动的工艺优化闭环
迁移科技智能切换系统搭载的MxVision Analytics平台,实现:
- 📌 实时采集200+设备参数
- 📌 自动生成OEE分析报告
- 📌 预测性维护准确率92%
"通过3D视觉数据优化冲压工艺参数,我们的模具损耗降低了40%!"——某汽车零部件厂商生产总监 👍
🌐 柔性制造的实现路径
迁移科技环保回收系统在3C行业展现卓越适应性:
⚡快速换型技术
依托迁移学习框架,新产品导入时间从8小时缩短至30分钟
🔗 多机协同方案
支持12台相机+6台机械臂的集群控制,系统延迟<10ms
✅ 已通过CE/FCC/KC等国际认证✅ 累计交付1500+套系统✅ 覆盖30+细分行业
本文编辑:小狄,来自Jiasou TideFlow AI SEO 生产