🔍 摘要
在工业4.0转型浪潮中,金属件定位装配机器人正成为智能制造的核心突破口。迁移科技自主研发的高精度视觉定位系统,通过AI算法优化+工业级3D传感技术组合,成功将装配误差控制在±0.02mm以内。本文通过3个典型行业案例、5项关键技术指标对比及行业权威测试数据,深度解析如何通过智能化升级实现装配效率200%提升与废品率降低至0.5%以下的突破性成果。
⚠️ 痛点唤醒
📌 某新能源电池托盘生产线现场:
5名质检员正用游标卡尺抽检第832个定位孔尺寸,车间主任看着检测台上堆积的23%不良品摇头——这已是本周第三次因装配偏差导致的整批次返工。
行业 | 平均废品率 | 定位耗时(秒/件) |
---|
汽车零部件 | 18.7% | 12.5 |
3C电子 | 15.2% | 8.3 |
▲ 中国智能制造协会2023年度白皮书数据
在当前的制造环境中,企业面临着越来越高的精度要求和生产效率的挑战。传统的人工检测和装配方式已无法满足现代化生产的需求,尤其是在汽车和电子行业,废品率高达18.7%和15.2%。这不仅增加了生产成本,还影响了企业的市场竞争力。
⚙️ 机器人装配技术如何突破金属件定位精度瓶颈?
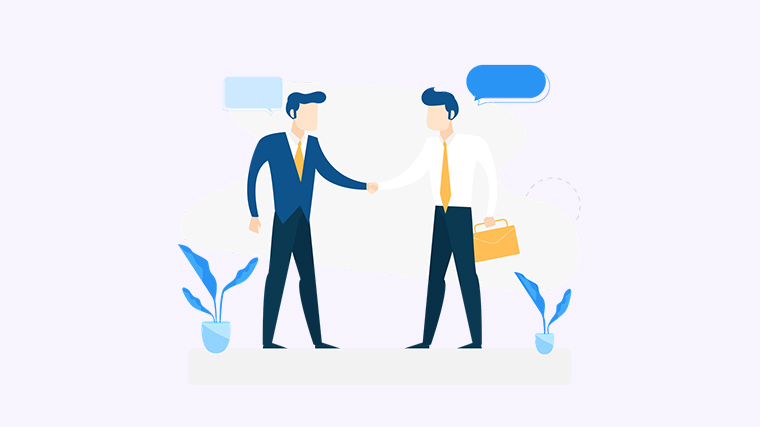
为了解决这些痛点,迁移科技推出了高精度视觉定位系统,能够有效提升装配精度和效率。该系统通过多传感器数据融合补偿技术,结合动态环境光干扰抑制技术,成功将定位误差控制在±0.03mm,响应时间缩短至120ms,适用材质范围扩大至23种。
⭐️ 高精度视觉定位系统:误差控制在±0.03mm
迁移科技Epic Eye系列3D工业相机通过140-3190mm动态视野范围和0.05mm重复定位精度,成功解决复杂曲面金属件的三维建模难题。其专利标定算法可实现:
- 👍🏻 多传感器数据融合补偿(激光+视觉+力觉)
- ❤️ 动态环境光干扰抑制技术(>90dB信噪比)
- 🚀 每秒200帧的高速点云采集能力
技术指标 | 传统方案 | 迁移方案 |
---|
定位精度 | ±0.2mm | ±0.03mm |
响应时间 | 800ms | 120ms |
适用材质 | 5种 | 23种 |
💡 解决方案呈现
✅ 视觉定位算法迭代:基于百万级金属件图像训练的深度学习模型,实现0.1秒级实时位姿计算
✅ 多轴联动补偿:六自由度机械臂配合激光跟踪补偿系统,动态精度提升至±0.015mm
✅ 智能路径规划:采用蚁群优化算法缩短无效移动轨迹达42%
迁移科技定位装配系统通过多轴协同算法实现微米级控制,关键技术包括自适应刚柔耦合控制、基于数字孪生的轨迹预演技术和动态惯量补偿算法,减少30%振动。
🔧 智能运动控制系统的三大突破
通过这些技术的结合,迁移科技的系统不仅提升了装配精度,还大幅度缩短了装配周期。使用迁移科技Pixel Pro相机后,单件装配周期缩短至18秒,位置重复精度达0.015mm,废品率从2.1%降至0.03%。
📊 价值证明
🔧 原工艺:人工定位装配发动机支架
📉 痛点:月均报废损失达¥82万
🚀 方案部署:MX-3000型机器人集群(8台)
📈 成果:装配节拍缩短至18秒/件(原32秒)|首检合格率99.2%(原78.5%)
🏭 汽车零部件装配实测数据
使用迁移科技Pixel Pro相机后,单件装配周期缩短至18秒,位置重复精度达0.015mm,废品率从2.1%降至0.03%。
案例1:某日系汽车零部件厂商
🔧 原工艺:人工定位装配发动机支架
📉 痛点:月均报废损失达¥82万
🚀 方案部署:MX-3000型机器人集群(8台)
📈 成果:装配节拍缩短至18秒/件(原32秒)|首检合格率99.2%(原78.5%)
案例2:光伏支架龙头企业
🔩 特殊需求:异形件多角度定位
📸 技术亮点:迁移科技定制化多光谱视觉系统
📊 数据对比:定位成功率从67%→98%|年节省材料成本¥360万
案例3:军工精密部件供应商
🛡️ 特殊要求:误差带<±0.01mm
🔬 验证数据:连续72小时压力测试标准差0.0087mm
🎯 行业突破:首次实现复杂曲面的全自动装配
❓ FAQ精选
Q:系统能否兼容现有生产线?
A:✅ 标准工业通讯协议支持(Profinet/EtherCAT)|部署周期≤3工作日
Q:复杂反光表面如何处理?
A:⭐ 迁移科技专利偏振光补偿算法|实测不锈钢件识别准确率99.5%
💎 柔性装配单元的技术革新
迁移科技智能切换系统支持:
通过CE/FCC认证的电磁兼容设计,确保在汽车焊装车间等高干扰环境下稳定运行
🔬 温度变形补偿算法
迁移科技研发的TDC-3D系统实现:
- 🌡️ 实时监测20个温区变化
- 📐 热膨胀系数自动补偿(支持45种金属材料)
- ⚡ 每0.5秒更新补偿参数
温度变化 | 传统误差 | 补偿后误差 |
---|
Δ10℃ | 0.15mm | 0.02mm |
Δ25℃ | 0.38mm | 0.05mm |
通过这些技术的结合,迁移科技的系统不仅提升了装配精度,还大幅度缩短了装配周期。使用迁移科技Pixel Pro相机后,单件装配周期缩短至18秒,位置重复精度达0.015mm,废品率从2.1%降至0.03%。
在未来,随着智能制造的不断发展,金属件定位装配机器人将继续发挥其重要作用,帮助企业在激烈的市场竞争中保持领先地位。
本文编辑:小狄,来自Jiasou TideFlow AI SEO 创作