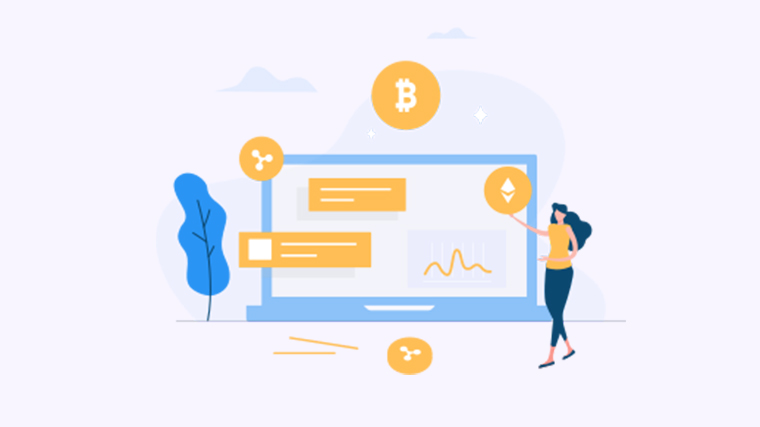
在现代汽车制造工业中,车门内板的上料过程对生产效率与产品质量至关重要。为了提高生产线的自动化水平,减少人工干预,同时确保上料的精准性和高效性,我们提出了视觉引导车门内板上料的解决方案。
客户痛点
冲压成型的工件具有种类极多、尺寸差异大、结构复杂等特性。生产中还存在精度要求高、车型新增快、工装维护成本高等问题,导致人工或是机器人固定轨迹抓取上料的方式都难以满足汽车实际生产需求。
智能凭借卓越的技术实力,成功助力众多汽车主机厂和零部件厂实现柔性自动化。以某知名大型汽车零部件厂为例,该厂在车门内板的上料环节采用了智能提供的创新解决方案,融合了AI、3D视觉和工业机器人技术。自引入该方案并投入生产以来,该产线的生产质量和效率均实现了显著的提升。具体而言,单线产能更是实现了超过两倍的增长,真正实现了全自动化生产的目标。
项目概述
该企业每日需处理大量车门内板,涉及复杂的加工流程。在原有生产方式中,工人们负责将内板从料架搬运至激光房焊接夹具,完成激光焊接后再手动搬运至下一工位。然而,随着生产规模的日益扩大,传统的人工作业模式在质量和效率上逐渐暴露出局限性,难以满足企业不断增长的生产需求。
项目亮点
1、精准识别与抓取技术的运用,显著提升了车门内板的生产质量
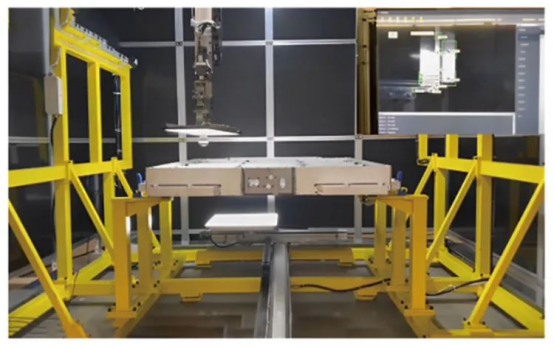
机器人高精度识别
在此项目中,我们采用了高精度的3D视觉系统,专门针对车门内板上精加工的主定位与辅定位销孔进行拍照。系统通过捕捉销孔位置的精确信息,确保插销抓取过程的准确无误。由于销孔孔径较小且工件表面存在反光现象,这对3D视觉系统的识别能力提出了极高的要求。
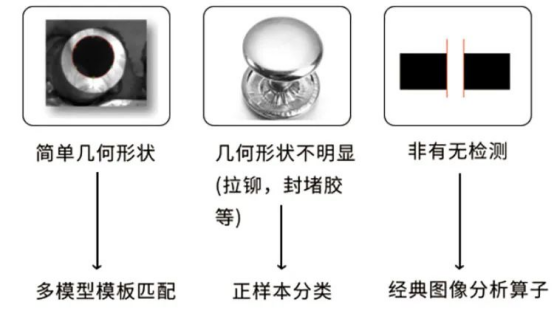
3D视觉系统
3D相机的运用,能够精准捕捉车门内板上小孔径销孔的详细特征,生成完整、精确且细致的点云数据,为后续的自动化处理提供了坚实的数据基础。 智能3D视觉系统能够引导机器人精准抓取,避免挤压、剐蹭造成车门内板形变、损伤,提升车门内板生产质量。
2、高柔性化,助力客户降本增效
在项目现场,由于同一批次的车门内板存在四种不同类型,包括左前门、右前门、左中门和右中门,每种内板都存放在特定的料架上。由于这些不同种类的内板销孔位置存在差异,因此对我们的3D视觉系统在适应性和灵活性方面提出了相应的挑战。我们的3D视觉系统需要能够精准识别不同内板的特征,并灵活调整识别参数,以确保准确捕捉各种类型内板的销孔位置信息。
3、高效率、高稳定性,更好实现生产全流程衔接
汽车生产车间规划布置不仅要从精度保证、生产效率、配送物流等多方面考虑,也需要考虑厂房环境、工位布局等现有条件。实现高效稳定生产、更好衔接各个生产流程也是汽车厂商格外关心的问题。智能3D视觉系统具有如下优势:
3D视觉系统通过精准定位两处销孔,有效引导机器人进行高效抓取,显著提升了生产线的作业效率。此外,智能自主研发的智能碰撞检测及轨迹规划算法,能够智能选择最佳的机器人运动路径和进入角度,有效规避料架干涉可能引发的碰撞,防止内板变形,进一步保障了生产过程的稳定性和产品质量。
智能的3D视觉产品具备卓越的环境适应性,即便在复杂多变的环境光干扰下,也能实现对各类物体的高质量成像。同时,它还能在粉尘、震动、潮湿、电磁干扰、高温等恶劣环境中保持长期稳定运行,为汽车制造行业的自动化生产提供了可靠的技术支持。
智能3D视觉系统可引导机器人精准抓取,具备生产效率高、稳定性高,且快速适应产品换型等诸多优势,能够切实满足众多车企对于高效率、高质量、安全性与成本控制等方面的要求。