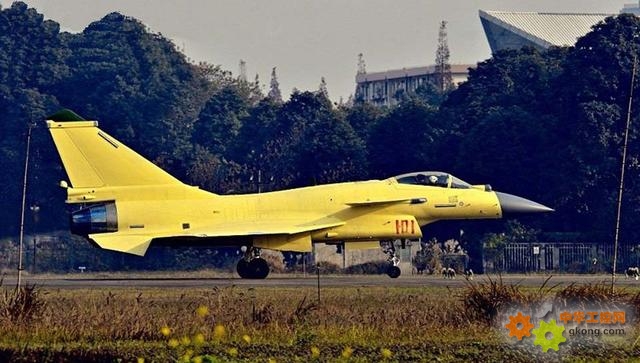
资料图:中国歼10B量产型曝光。中国航空工业近年已推出多款新型战斗机
中国航空制造离工业4.0有多远?
“工业4.0”是在2013汉诺威国际工业博览会上最令人关注的热词,其概念于2011年在德国举行的工业设备展会“Hannover Messe 2011”上提出这项由德国联盟教研部与联邦经济技术部联手推动的战略性项目,被视为提振德国制造业的强力催化剂,被有识之士认为将是全球制造业未来发展的方向。
“工业4.0”项目主要由两大部分构成,一是“智能工厂”,即重点研究智能化生产系统及过程,以及网络化分布式生产设施的实现;二是“智能生产”,主要涉及整个企业的生产物流管理、人机互动以及3D技术在工业生产过程中的应用等。信息通信技术(ICT)是实现“工业4.0”的关键技术,具体包括联网设备之间自动协调工作的M2M(Machine to Machine)、通过网络获得的大数据的运用、与生产系统以外的开发/销售/ERP(企业资源计划)/PLM(产品生命周期管理)/SCM(供应链管理)等业务系统联动等等。智能工厂或者“工业4.0”,是从嵌入式系统向信息物理融合系统(CPS)发展的技术进化。
信息物理融合系统(CPS),包括自主交换信息的智能机器、存储系统和生产设施,它们可以独立运行和相互控制。这种系统从根本上改善了工业过程,包括制造、工程、材料使用、供应链和生命周期管理。智能工厂或者“工业4.0”,是从嵌入式系统向CPS发展的技术进化,通过通信网络,将工厂内所有设备互联,以实现信息物理高度融合。它作为未来第四次工业革命的代表,正不断向实现物体、数据以及服务等无缝连接的互联网(物联网、数据网和服务互联网)的方向发展。德国投入了2亿欧元,已在制造业的所有领域中实施了该项目的研究。
未来的生产系统,以及智能工厂的产品、资源及处理过程因CPS的存在,将具有非常高的实时性,同时在资源、成本节约中颇具优势。智能工厂将按照重视可持续性的服务中心的业务来设计。由于智能工厂具有服从性、灵活性、自适应性和可学习等特征,其具有的容错能力、风险管理能力,通过可实时应对的灵活生产系统,实现生产工程的彻底优化。智能工厂的设备将基于自动观察生产过程的CPS的生产系统的灵活网络来实现高级自动化。同时,生产优势不仅在特定生产条件下一次性体现,也可以实现多家工厂、多个生产单元所形成的世界级网络的最优化。
IT创新对航空制造业的影响
进入21世纪后,随着IT技术突飞猛进的发展,我国航空制造业在产品设计、协调依据、工艺规划设计与管理、零件制造、装配、产品检测、物料配送与供应链管理、售后服务等覆盖产品全生命周期的各个环节都发生了革命性的改变。随着数字化技术的不断发展和深入应用,国内航空产品设计经历了从二维手工制图到全三维数字化产品定义,从“抛砖头”的串行设计到面向制造的并行协调设计的演进。产品协调逐步从模线——样板——标准样件的模拟量协调过渡到全三维数字量协调模式。曾于20世纪60年代红极一时的样件制造逐渐被时代淘汰。工艺设计逐步从二维离散式手工编制向基于知识的全三维结构化自动工艺设计方向演进,工艺仿真技术的应用打破了“设计-制造-评价”和“实物验证”这一传统模式,不需要实际产品作支持,有效地解决了传统的二维装配工艺设计周期长、需要实物验证、效率低的企业制造瓶颈问题,从而提供了三维工艺设计的环境,确保工艺工程师、工装设计师尽早地参与到产品设计研发中去,与设计人员并行开展工作,及早发现在装配过程中的各种干涉问题,并将这些信息反馈给设计人员,结合人机工效评估结果对工艺方法、工装结构和生产线布局等进行修改和优化,在产品上游设计阶段即可消除潜在的装配冲突与缺陷、评价产品的可装配性,帮助企业拥有“面向制造的设计”和“面向维护的设计”,实现真正意义上的数字化并行工程。
在零件制造方面,机械加工已经实现依据产品三维设计模型快速编程和仿真,部分车间甚至建立了车间物联网,依据设备的使用情况和需求自动排产。钣金成型技术也由手工成型逐步向柔性多点模精确成型发展。应用仿真技术可以提前预判零件的成型工艺性,采用回弹补偿技术,降低零件返修率,缩短零件制造周期30%以上。导管制造也由机上打实样的传统导管制造工艺方法发展到采用数控弯管机、测量机等先进设备进行管类零件的弯曲成型及检验的数字化制造工艺技术。复合材料制造也从按样板手工铺叠发展到直接按三维模型进行数控下料、自动铺叠的先进制造工艺。飞机装配模式也逐步从大型复杂刚性工装“一对一”手工装配模式逐步向自动化系统“一对多”柔性装配模式发展。IT技术的广泛应用使企业管理逐步由粗放型向精细化管理转变,物料配送和供应链管理发生了根本性改变,例如标准件配送和采购逐步由“干一备三”的大批量库存、年终盘点、手工计数领用的传统模式向标准件自动拣选、按需采购、零库存或适度备货的模式转变。企业领导者可以通过强大的信息化系统应用,及时准确地了解企业各个关键环节的进展情况和存在的问题,大大提高了办公效率。IT技术创新使我国航空制造业进入快速发展的时代,新机研制周期不断缩短,新式航空武器装备呈现出井喷式的态势。然而,我国的航空制造业还远远未达到工业4.0的水平,我们必须正视现实,认清形势,迎头赶上。
中国航空制造业的工业4.0之路
构成工业4.0的基础包含两个方面,即高度自动化和信息化。“十一五”以来,我国在国防工业基础技术研究上加大了投入力度,逐步掌握了如多点模成型、自动制孔、柔性装配和大部件自动对接等航空制造的关键技术,也在局部点上形成了示范应用的效应。但与发达国家相比,我们的自动化水平还有巨大的系统化差距,我们仅解决了高端国产化的设备问题,大量的先进科研成果和发明专利还在高校、科研院所被束之高阁,没有转化成生产力。原理样机距离工程化应用还有很长的距离。在国内航空制造企业,在生产线上的高端装备多是进口设备,这说明我国航空制造业的基础技术还很薄弱,自动化水平相对较低,较长时间内如何快速实现自动化/智能化装配仍是我们面临的主要问题。
如今的云计算、大数据、移动互联网等新技术为两化融合提供了有力支撑。随着我国航空制造业信息化应用技术水平快速提升,逐步构建起实时广泛的物联网络平台和灵活动态的基础信息架构,以支持航空制造企业高度协同的设计制造、高效统一的运营管理和随需而动的智能决策发展需求,实现生产线的信息化集成管理。
国家两化融合创新推进联盟理事长杨海成在发表“两化融合的新技术与应对策略”主题演讲时指出:当前制造业在信息化的浪潮下面临全球化、精益化、协调化、服务化、绿色化、智能化等特征的变化,不仅改变了产品本身,也改变了产品的制造流程,改变了整个制造业的革命。我国还是制造大国而不是强国,从低端制造到高端制造,首先是信息高技术的发展,生产性制造转向服务性的制造,拉长产品的服务周期,提高产品的价值。新一代的集成协同技术实现企业内外部资源的协同,云计算技术与制造技术的结合,使制造业的资源实现更大的共享,两化深度融合也许可以让我国的航空制造业实现弯道超车。
实现工业4.0,必须解决好以下四个方面的问题:
安全和保密问题。这就要求必须满足两个条件:一是确保生产设施和产品本身对人或环境不造成任何危险;二是防止数据被滥用和未经授权的访问。军工企业由于其特殊性,安全保密的问题是不可逾越的红线。在目前国家保密法的规定框架内,保密要害部位不能存在任何的无线通信设备,保密信息系统的软件防护也有十分严格的限制,因此,实现航空工业技术发展,必须妥善处理好保密安全问题是当务之急。
标准化和参考架构。在漫长的信息化发展进程中,企业发展前期很难在可持续发展的信息化规划下构建信息化系统,通常情况是对需求迫切的部门,先在相对独立的业务流程中开发出一套信息化系统,而导致遗留的信息孤岛。因此,随着工厂与工厂内外的很多事物和服务连接起来,通信手段及数据格式等很多事物必须统一IT架构,制定共同标准,而且需要一个参照架构来为这些标准提供描述并促进标准的实现。
复杂系统的管理。随着生产系统与其他系统连接起来,整个系统变得复杂,管理变得越来越困难。制造系统正在日益变得复杂,适当的计划、描述和说明模型可以为这些复杂系统提供管理基础。工程师们应该为了发展这些模型而进行更多的方法创新和工具应用。
通信基础设施的建设。要购置可用于工业用途的、可靠性高的通信基础设施和通讯网络是工业4.0的关键要求。
工业4.0的出现,必将从根本上改变企业的组织和管理,以及人们的工作方式和职业诉求。企业的可利用资源可以面向全球,原材料变为产品的过程更加多产和高效。