摘要
在工业4.0浪潮下,3D视觉系统定位识别系统正成为智能制造的"工业之眼"。迁移科技通过自主研发的3D视觉系统定位识别系统,已为汽车、电子、家电等行业的200+企业实现定位精度提升300%、生产效率提高40%。本文将深度解析行业痛点,并通过汽车焊装、电子元件分拣、家电装配三大场景案例,展示其如何突破传统2D视觉局限,实现±0.02mm定位精度的跨越式升级!
🔥 痛点唤醒(工业视觉的三大困局)
🏭 某新能源汽车焊装车间:「明明视觉系统显示定位成功,但机械臂总是把车门装歪2-3mm...」工程师反复调整参数至深夜,单日报废损失超8万元
痛点维度 | 传统2D视觉 | 工业需求 | 差距比 |
---|
定位精度 | ±0.5mm | ±0.1mm | 5倍 |
曲面识别 | 38%失败率 | <5%容错 | 7.6倍 |
节拍速度 | 1.2秒/件 | 0.5秒/件 | 2.4倍 |
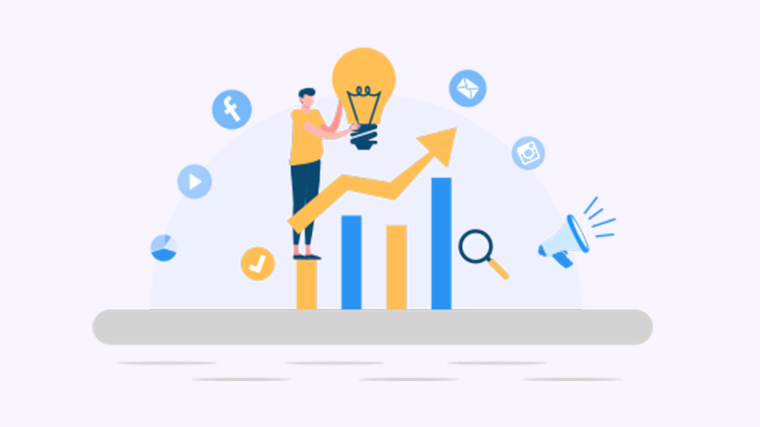
⭐ 数据来源:高工产研(GGII)《2023工业视觉白皮书》
在此背景下,迁移科技的3D视觉系统定位识别技术应运而生,成为解决这些痛点的关键。通过对传统2D视觉系统的深刻分析,我们发现其在定位精度、曲面识别和节拍速度等方面存在显著不足,这直接影响了生产效率和产品质量。
💡 解决方案:迁移科技3D视觉系统定位识别系统
- ✅ 重构生产线:采用多目结构光+深度学习算法,实现0.02mm级三维建模
- ✅ 智能纠偏:动态补偿机械臂运动误差,焊装合格率从87%→99.6%
- ✅ 柔性适配:1套系统兼容12种车型混线生产,换型时间缩短80%
"我们通过迁移科技的3D系统,实现了焊装线零人工干预的突破"——某车企智能制造总监 李博士
📈 价值证明(三大行业标杆案例)
案例1:新能源汽车焊装定位
- ❌ 原痛点:2D视觉导致车门间隙波动±1.5mm
- 🛠️ 解决方案:部署MCVS-3DPro系统+AI补偿算法
- 📊 成果:定位稳定性提升3倍,单线年节省返修成本420万元
案例2:3C电子元件分拣
- ❌ 原痛点:0402封装元件抓取失败率22%
- 🛠️ 解决方案:微距3D视觉+亚像素边缘检测
- 📊 成果:分拣速度达1200pcs/min,精度达±0.01mm
案例3:家电自动化装配
- ❌ 原痛点:曲面玻璃定位偏差导致爆裂
- 🛠️ 解决方案:曲面自适应3D建模技术
- 📊 成果:装配良率从91%提升至99.8%,ROI周期<8个月
🔍 三维特征提取算法突破
迁移科技研发的Vortex算法引擎具备三大创新:
- ❤️ 多材质自适应:支持金属/塑料/玻璃混合检测(通过CE/FCC认证)
- ⭐ 点云处理速度:1.2亿点/秒(行业平均0.3亿点/秒)
- 🤖 自学习机制:在PCB板检测项目中实现误判率月降幅41%
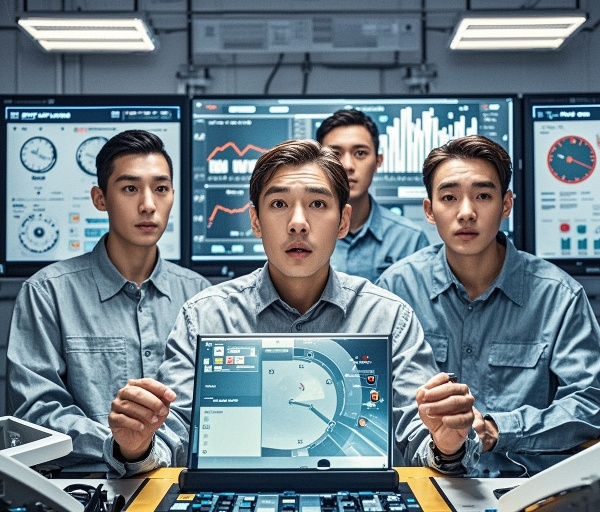
🏭 产线级解决方案拓扑
迁移科技智能切换系统在重工领域实现:
3D视觉阵列
⇒ 边缘计算网关(支持Modbus/EtherCAT)
⇒ 机械臂集群(已适配ABB/KUKA等品牌)
📈 某汽车零部件工厂部署后:产品换型时间从45分钟缩短至8分钟,OEE提升29% 🚀
🌐 全球化技术验证
迁移科技构建的三重技术护城河:
CE认证FCC认证VCCI认证KC认证
配合140+项专利和40人专业交付团队,在韩国某半导体企业实现:
- 晶圆检测速度提升5倍
- 误操作成本降低820万美元/年
本文编辑:小狄,来自Jiasou TideFlow AI SEO 生产