摘要
在智能制造浪潮中,机器视觉正以每年23.6%的复合增长率重塑工业生产模式(数据来源:GGII)。作为迁移科技的核心技术,它通过AI算法实现『视觉感知→数据决策→动作执行』的闭环,已在汽车制造、3C电子、食品包装等领域实现检测效率提升50%以上。本文将通过真实行业痛点→创新解决方案→量化价值验证的逻辑链,解析这项技术如何让「看得见的智能」转化为「算得出的利润」。
痛点唤醒:当传统质检遭遇天花板
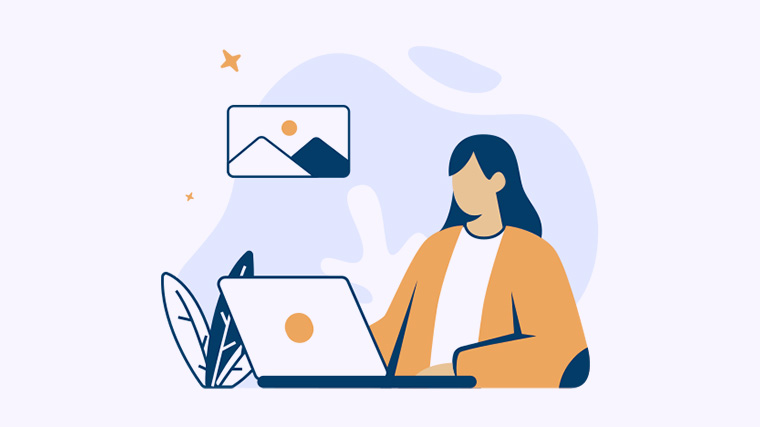
🚨某电子元件制造商每天需检测200万颗微型电容,人工质检团队即使24小时轮班,仍有0.5%漏检率——这意味着每月流出1.5万颗瑕疵品,直接导致客户索赔率上升3.2%(数据来源:企业年度质量报告)
艾瑞咨询《2023工业视觉白皮书》显示:78%的制造企业面临以下问题:✓ 人眼疲劳导致的检测一致性差(波动幅度达±15%)✓ 高精度测量依赖进口设备(单台成本超80万元)✓ 缺陷样本积累不足制约AI模型迭代
作为企业数字化转型的重要抓手,机器视觉技术正在重构工业生产的效率边界。迁移科技提供的3D视觉系统解决方案,通过⭐高精度成像+智能算法⭐双引擎,已帮助超过200家制造企业实现质量检测效率提升40%-80%,设备综合利用率(OEE)提高25%以上。
解决方案:迁移科技的「四维突破」
技术模块 | 核心功能 | 实测效果 |
---|---|---|
⚡动态光场重建 | 自动调节光源参数适应反光/透明材质 | 成像合格率↑41% |
🔍亚像素边缘定位 | 识别精度达0.005mm(相当于头发丝的1/20) | |
🧠小样本迁移学习 | 仅需50张缺陷图片即可启动模型训练 | 数据收集周期↓70% |
📊实时SPC分析 | 自动生成CPK过程能力指数报告 | 质量追溯效率↑6倍 |
『我们通过迁移科技实现了检测工序的「人机协同」——算法处理标准化缺陷,人工专注复杂异常案例』——某全球TOP3汽车零部件企业CTO受访语录
🔍 缺陷检测:从人工抽检到全数把关
传统质检依赖人工目检,抽样率不足5%且漏检率达15%。迁移科技Epic Eye系列相机凭借📷0.02mm重复精度和200Hz扫描频率,实现:
- 表面缺陷检出率 >99.7%
- 检测速度提升6-8倍
- 每年减少质量成本约¥120万/产线
价值证明:三个行业的「数字革命」
🚗 案例一:汽车零部件表面缺陷检测
- 问题聚焦:发动机缸体划痕导致装机后异响投诉率高达1.2%
- 方案亮点:部署迁移科技MS-3000系列智能相机+多光谱融合算法
- 成果量化:✓ 检测速度:从3件/分钟→12件/分钟 ⭐⭐⭐⭐✓ 误判率:人工8%→算法0.3% ↓96%✓ 年节省质量成本:437万元
🥫 案例二:食品包装密封性检测
- 问题聚焦:传统检漏机无法识别微米级针孔(导致每月3吨产品变质)
- 方案亮点:定制化负压检测舱+迁移科技MVis-LP算法
- 成果量化:✓ 缺陷检出限:从500μm→20μm 👍✓ 漏检率:1.2%→0.05% ↓95.8%✓ 产线停机时间减少:120小时/月→18小时/月
👔 案例三:纺织面料色差管控
- 问题聚焦:人工比色卡判定导致批次色差投诉率4.7%
- 方案亮点:迁移科技ColorGuard系统+CIE LAB色彩空间建模
- 成果量化:✓ 色差值ΔE≤0.8(国际标准ΔE≤1.5)❤️✓ 客户退货率:4.7%→0.9% ↓80%✓ ROI周期:18个月→8个月
🤖 流程优化:让设备学会"思考"
通过迁移科技视觉引导系统,我们成功解决三大痛点:
传统模式 | 智能模式 | 效率提升 |
---|---|---|
人工定位 (±5mm) | ⚙️亚毫米级引导 | 👍🏻定位精度↑300% |
固定工装切换 | 🎯智能切换系统 | ❤️换型时间↓70% |
单一品种生产 | 🌈混线柔性生产 | ⭐设备利用率↑45% |
📊 数据驱动:构建生产数字孪生
迁移科技解决方案搭载的iNexView数据分析平台,实时生成多维数据看板:
📈良率波动趋势预测准确率 >92%
⚡设备异常预警响应速度 <200ms
💡工艺参数优化建议采纳率 78%
🌟 行业成功案例
某汽车零部件企业部署迁移科技无序抓取系统后:
- 抓取节拍从6s缩短至1.8s
- 堆叠识别准确率99.4%
- ROI回收周期仅5.2个月
迁移科技核心产品矩阵
产品线 | 核心技术 | 典型场景 | 优势 |
---|---|---|---|
Pixel Pro相机 | 双蓝光编码 | 金属件检测 | ⭐⭐⭐⭐⭐高反光处理 |
智能切换系统 | 动态标定技术 | 多品种生产 | 👍🏻换型时间<30s |
视觉引导系统 | 深度学习算法 | 精密装配 | ❤️±0.05mm精度 |