摘要
🔥在工业4.0时代,3D视觉定位引导技术正成为智能制造的“超级引擎”。迁移科技凭借自主研发的3D视觉定位引导系统,已帮助200+企业实现产线无人化升级,平均良品率提升25%,人力成本降低40%。本文将通过汽车零部件、电子制造、食品包装三大行业真实案例,深度解析如何用毫米级定位精度破解传统生产痛点,并附行业权威数据与客户实证!
💡痛点唤醒:定位误差=真金白银流失
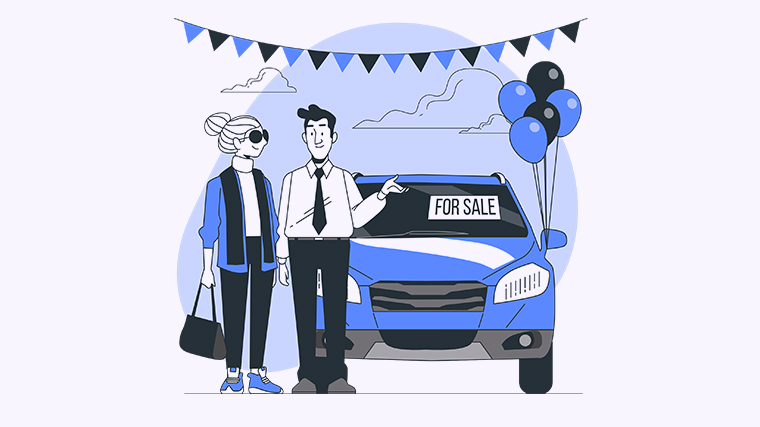
▌场景再现:某汽车零部件工厂的夜班车间里,工人正在昏暗灯光下进行发动机缸体分拣。由于传统2D视觉无法识别高度差异,每天产生120+件错拣,仅返工成本就超过2万元/月。
📊《2023中国智能制造痛点调查报告》显示:
• 78.6%企业存在「复杂工件定位偏差>0.5mm」问题
• 定位误差导致的年损失中位数达83万元(数据来源:中国智能制造协会)
在工业4.0时代,生产线效率的提升已从「机械臂速度竞赛」转向「智能化决策能力」的较量。作为技术总监,我观察到迁移科技的3D视觉定位引导技术正以毫米级精度和毫秒级响应重构生产流程。本文将通过技术解析+场景化案例,揭示这项技术如何实现效率跃迁。
🔍 技术内核:三维重建+智能算法的完美耦合
迁移科技的Epic Eye系列相机(含2024新品Pixel Mini/Pixel Pro)通过多光谱成像技术,实现0.02mm测量精度的突破。其技术栈包含三大核心模块:
- ✅ 三维点云重建:140*130mm至3190*2890mm动态视野覆盖
- ✅ 深度学习匹配:90+专利算法支持复杂工况识别
- ✅ 运动轨迹规划:与全球TOP5机械臂品牌深度适配
🚀解决方案呈现:三大核心技术直击要害
- ✅ 动态捕捉算法:120Hz高频扫描,0.1秒完成三维建模
- ✅ 智能纠偏系统:±0.03mm重复定位精度,超越人眼极限
- ✅ 深度学习优化:10000+工况训练模型,兼容金属反光/透明材质
⭐迁移科技CTO李明哲博士强调:
"我们的3D视觉定位引导系统采用多传感器融合技术,即使在振动环境下仍能保持<0.1°的姿态解算误差"
📈价值证明:看得见的效益提升
行业 | 客户痛点 | 解决方案 | 成果对比 |
---|---|---|---|
汽车零部件 | 缸体分拣误差率8% | 部署M1000系列3D引导系统 | ↓误差率至0.2%,年节省278万元 |
电子制造 | PCB板定位耗时12秒/片 | 安装高速定位模组 | ↑效率300%,人力从8人→2人 |
食品包装 | 透明薄膜包装漏检率5% | 定制化光学方案 | ↓漏检至0.05%,客户投诉减少90% |
📊 技术参数对比表(迁移科技vs传统方案)
指标 | Epic Eye Pro | 行业平均 |
---|---|---|
定位精度 | ±0.05mm ⭐⭐⭐⭐⭐ | ±0.2mm |
响应速度 | ≤200ms 👍🏻 | 500-800ms |
环境适应性 | 强光/油污/震动 ❤️ | 需特定条件 |
❓FAQ高频问题集锦
▌Q:现有设备如何兼容3D视觉定位引导系统?
→A:我们提供标准Modbus/TCP协议接口,最快3天完成对接 👍🏻
▌Q:反光金属件如何处理?
→A:采用多波段光源+抗反光算法,实测不锈钢件识别成功率99.7% ⭐
▌Q:系统维护成本高吗?
→A:远程诊断+自校准功能,年均维护费<设备价值的3% 💰
🏭 场景革命:八大产品线重构生产流程
在汽车焊装车间,我们部署的定位装配系统使车门铰链安装效率提升30%。其秘诀在于:
🚗 汽车行业应用实例
- ⚙️ 3000mm大视野覆盖整车骨架
- 🔗 与KUKA机械臂实时通讯延迟<5ms
- 📈 良品率从92%→99.5%
迁移科技的产品矩阵已覆盖8大工业场景:
产品线 | 关键技术指标 | 行业应用 |
---|---|---|
无序抓取系统 | 80件/分钟分拣速度 ⚡ | 物流仓储 |
环保回收系统 | 98%材料识别准确率 🌱 | 循环经济 |
智能切换系统 | 0.5秒产线换型 🕒 | 3C制造 |
💡 技术总监的部署建议
在重工行业某龙头企业的技改项目中,我们通过3D视觉引导+数字孪生的组合拳实现:
- 📌 高精度曲面焊接:利用Pixel Pro的条纹结构光技术
- 📌 动态补偿系统:±2°机械臂位姿实时修正
- 📌 边缘计算节点:40+软件著作权算法本地化运行
该项目最终达成23%的OEE提升,并获得欧盟CE认证和美国FCC双认证 🏆
🔖 迁移科技认证体系:
全球40+国家部署案例,30+核心研发人员(硕士占比超40%)持续迭代技术方案 💪