走进高精度三维尺寸测量
在现代工业的精密舞台上,高精度三维尺寸测量技术无疑是一位至关重要的 “幕后英雄”。它如同工业生产的 “火眼金睛”,精准地捕捉每一个零部件的细微尺寸信息,为产品质量保驾护航。从汽车制造到航空航天,从电子设备到医疗器械,高精度三维尺寸测量技术的身影无处不在,发挥着不可或缺的关键作用。
以汽车制造行业为例,一辆汽车由上万个零部件组成,每个零部件的尺寸精度都直接影响着整车的性能、安全性和舒适性。高精度三维尺寸测量技术能够在汽车设计、零部件制造、整车装配等各个环节,对零部件进行精确测量和质量检测。在零部件制造过程中,通过实时监测加工尺寸,确保零部件符合设计要求,有效减少废品率;在整车装配环节,对车身、发动机、底盘等关键部件进行精确测量和匹配,保证整车的装配精度和性能稳定性。
再看航空航天领域,其对零部件的尺寸精度和质量要求近乎苛刻。飞机发动机的叶片、航空发动机的涡轮盘等关键零部件,不仅要承受高温、高压、高速等极端工况,还要保证极高的精度和可靠性。高精度三维尺寸测量技术能够实现对这些复杂零部件的高精度测量和检测,及时发现潜在的缺陷和问题,确保航空航天器的安全飞行。
此外,在电子设备制造领域,随着电子产品向小型化、轻薄化、高性能化发展,对零部件的尺寸精度和表面质量要求也越来越高。高精度三维尺寸测量技术可以对微小的电子元器件进行精确测量,为电子产品的设计和制造提供重要的数据支持,助力电子产品不断创新升级。
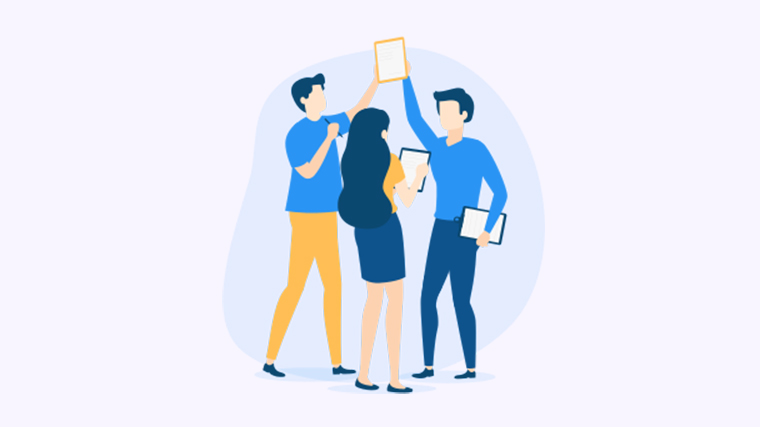
高精度三维尺寸测量技术已然成为现代工业生产中不可或缺的关键技术,它不仅提升了产品质量和生产效率,还推动了工业制造向更高精度、更高质量的方向发展。接下来,让我们一同深入探索高精度三维尺寸测量技术的奥秘。
测量技术大揭秘
接触式测量 —— 三坐标测量机
三坐标测量机是接触式测量中的 “佼佼者”,它的工作原理基于直角坐标系。在一个由 X、Y、Z 三个互相垂直的运动轴建立起的直角坐标系中,测头宛如一位精准的 “舞者”,其一切运动都在这个坐标系中优雅进行,测头的运动轨迹由测球中心精准表示。当进行测量时,被测零件被稳稳地放置在工作台上,测头如同一位严谨的检验员,轻轻与零件表面接触 。此时,三坐标测量机的检测系统就像一台精密的信号接收器,能够随时敏锐地给出测球中心点在坐标系中的精确位置。当测球沿着工件的几何型面缓缓移动时,就如同一位技艺高超的画师,精确地勾勒出被测工件的几何尺寸、形状和位置公差等关键信息。
三坐标测量机凭借其独特的优势,在高精度测量领域占据着重要地位,成为众多精密制造行业不可或缺的测量设备。以下是其优缺点对比:
优点
|
缺点
|
精度极高,能够达到微米级别,甚至在一些高端设备中,精度可以达到亚微米级,这使得它在对精度要求苛刻的航空航天、精密模具制造等行业中备受青睐,能够精准检测高公差的机加工零件及中小型零部件,确保产品质量。
|
检测异形件时,由于其形状的不规则性,测头难以全面、准确地接触到所有测量点,导致检测难度大幅增加,耗时较长;对于大型件,不仅测量空间可能受到限制,而且搬运和装夹大型工件也较为困难,增加了测量的复杂性。
|
可以测量的特征丰富多样,几乎涵盖了所有类型的尺寸测量,如长度、直径、角度、平面度、圆柱度等,还能精确检查度数和同心度等复杂特征,满足各种复杂工件的测量需求。
|
对于柔性材料,如橡胶、泡沫等,由于其质地柔软,测头接触时会使材料发生变形,从而无法获取准确的测量数据,不适用于此类材料的测量。
|
自动化程度较高,可通过编程实现自动化测量,不仅大大提高了测量效率,还能有效避免人工测量时可能出现的主观误差,确保测量结果的一致性和可靠性。
|
设备本身价格昂贵,加上配套的软件系统和高精度的硬件耗材,需要大量的资金投入,这对于一些预算有限的中小企业来说,是一个较大的经济负担。
|
灵活性强,可根据不同的测量需求灵活配置各种探头和夹具等配件,以适应不同形状、尺寸和材质的工件测量,同时也能实现对复杂曲面的精确测量,满足多品种、小批量生产的多样化需求。
|
对环境要求较为苛刻,温度、湿度、空气流动等环境因素的微小变化都可能对测量精度产生显著影响,因此需要保证相对稳定的环境条件,这无疑增加了使用成本和维护难度。
|
非接触式测量
光栅三维扫描仪(拍照式)
光栅三维扫描仪,又被称为拍照式三维扫描仪,宛如一位神奇的 “光影捕手”,基于独特的光学原理工作。它主要由光栅投影设备及两个工业级的 CCD Camera 构成,其工作原理恰似人类的双眼,巧妙地利用了三角测量原理。工作时,光栅投影设备将精心编码的光栅条纹投影在待测物面上,这些条纹如同神秘的密码,带着独特的信息。随着光栅条纹的粗细变化及位移,配合 CCD Camera 快速、精准地撷取数位影像。这些影像数据就像一个个拼图碎片,通过电脑强大的运算处理能力,进行快速、高效的分析和计算,从而精确得知待测物的 3D 外型。
在实际应用中,无论是复杂的汽车零部件,还是精致的艺术品,光栅三维扫描仪都能轻松应对,快速、准确地获取其三维数据。其优缺点如下:
优点
|
缺点
|
精度相当高,部分高端产品的精度能够达到微米级,完全能够满足工业设计、逆向工程等对精度要求极高的领域需求,为产品的研发和创新提供了有力的数据支持。
|
对环境和物体材质的要求较为严格,强光环境下,光栅条纹可能会受到干扰,导致扫描数据不准确;对于黑色物体,由于其吸光性强,反射光线弱,可能会影响扫描效果;而透明物体则会因为光线的折射和透射,使得扫描难度加大,数据质量下降。
|
扫描速度极快,能够在短时间内完成大量数据的采集工作,大大提高了工作效率,尤其适用于对大型物体或需要快速获取数据的场景,如汽车白车身的测量、大型模具的检测等。
|
设备成本较高,高精度的光栅三维扫描仪价格往往不菲,这对于一些预算有限的企业或个人来说,是一个较大的经济障碍,限制了其广泛应用。
|
采用非接触测量方式,避免了与被测物体直接接触,这不仅不会对物体表面造成任何损伤,还能有效减少因接触而产生的变形或误差,特别适用于对表面质量要求高、易变形的物体测量,如文物、精密电子元件等。
|
数据处理相对复杂,虽然支持自动拼接和实时数据处理,但在面对一些复杂场景,如物体表面存在大量孔洞、缝隙或纹理复杂时,仍需要专业人员进行细致的后处理,增加了操作难度和时间成本。
|
适用性极强,无论是各种大小、形状的物体,包括复杂的曲面、内部结构,还是具有特殊表面材质的物体,它都能很好地适应,为产品研发设计、逆向工程及三维检测等提供了全方位的技术支持,应用领域广泛。
|
-
|
自动化程度高,支持自动拼接和实时数据处理,能够自动识别和匹配不同角度扫描的数据,减少了人工干预,提高了数据处理的准确性和效率,降低了人为因素导致的误差。
|
-
|
激光三维扫描仪
激光三维扫描仪则像是一位不知疲倦的 “光速测绘员”,通过激光测距这一核心原理来获取物体的三维信息。工作时,它向被测物体表面发射出一束束激光,这些激光如同快速穿梭的信使,瞬间到达物体表面,然后反射回扫描仪内的传感器。扫描仪根据激光往返的时间,精确计算出其与物体之间的距离,进而确定物体在空间中的位置。通过不断地扫描物体表面,获取大量密集的点云数据,最终快速、准确地复建出被测目标的三维模型及线、面、体等各种图件数据 。
在实际应用中,激光三维扫描仪大显身手,从大型建筑的测绘到工业零部件的检测,都能看到它的身影。它的优点和缺点如下:
优点
|
缺点
|
精度同样可达到毫米级甚至更高,在一些高精度要求的测量任务中,如航空发动机叶片的检测、精密机械零件的制造等,能够提供精准的测量数据,确保产品质量和性能。
|
设备成本居高不下,高精度的激光三维扫描仪价格昂贵,对于许多预算有限的用户来说,是一个难以承受的经济负担,限制了其普及和应用范围。
|
测量范围十分广泛,根据不同类型的激光扫描仪,测量范围可从几厘米到几十米不等,无论是小型的电子元件,还是大型的建筑物、桥梁等,它都能轻松应对,满足各种不同规模物体的测量需求。
|
数据处理复杂,激光扫描获取的点云数据量庞大且复杂,需要专业的软件和强大的计算能力进行后处理和分析,对操作人员的技术水平和设备性能要求较高。
|
扫描速度快,能够在短时间内获取大量点云数据,极大地提高了工作效率,尤其适用于对大面积物体进行快速测量的场景,如地形测绘、大型场地的建模等。
|
精度校正困难,激光扫描仪的精度校正和检查方法较为单一且复杂,需要专业人员使用专门的设备和工具进行操作和维护,增加了使用和维护成本。
|
抗外界干扰能力强,能够在各种复杂的现场测量环境中稳定工作,无论是室内的工业厂房,还是室外的施工现场,甚至是无光环境下,它都能正常工作,获取可靠的测量数据。
|
-
|
部分激光扫描仪设计轻便、小巧,便于携带,方便进行现场测量和移动作业,如在文物古迹的测绘、交通事故现场的勘查等场景中,能够灵活、快速地开展工作。
|
-
|
实际应用案例解析
汽车制造中的应用
在汽车制造行业,某知名汽车厂商在生产一款新型汽车时,充分运用了高精度三维尺寸测量技术,为汽车的高质量生产提供了坚实保障。
在零部件检测环节,该厂商采用三坐标测量机对发动机缸体、活塞、曲轴等关键零部件进行高精度测量。以发动机缸体为例,其内部结构复杂,各个缸筒的直径、圆柱度以及平面度等尺寸精度要求极高,直接关系到发动机的动力输出和燃油经济性。三坐标测量机能够精确测量这些尺寸参数,将实际测量值与设计标准值进行对比,一旦发现尺寸偏差超出允许范围,立即对生产工艺进行调整,有效避免了因零部件尺寸不合格而导致的发动机性能下降甚至故障问题。通过这种严格的零部件检测,该厂商将发动机的废品率降低了 30%,大大提高了生产效率和产品质量。
在车身装配过程中,高精度三维尺寸测量技术同样发挥着关键作用。车身是由众多冲压钣金件焊接而成,其装配精度直接影响到汽车的外观、密封性以及行驶稳定性。该厂商利用激光跟踪仪和拍照式三维扫描仪对车身进行实时监测和测量。在焊接前,对每个钣金件进行三维扫描,确保其尺寸和形状符合设计要求;焊接过程中,通过激光跟踪仪对焊接点的位置进行精确测量,保证焊接精度;焊接完成后,再次对整个车身进行三维扫描,与设计模型进行全面比对,检测车身的装配精度和整体质量。通过这些措施,车身装配的精度得到了显著提高,车身缝隙的均匀度控制在 ±0.5mm 以内,不仅提升了汽车的外观品质,还增强了车身的结构强度和密封性,有效降低了车内噪音和漏水风险,提高了汽车的安全性和舒适性。
航空航天领域的应用
航空航天领域对零部件的精度和质量要求近乎苛刻,高精度三维尺寸测量技术在这里发挥着不可或缺的作用。以航空发动机叶片的测量为例,航空发动机叶片作为发动机的核心部件之一,其工作环境极其恶劣,需要承受高温、高压、高速气流的冲击,因此对叶片的尺寸精度、型面轮廓以及表面质量要求极高。稍有偏差,就可能导致发动机性能下降,甚至引发严重的安全事故。
某航空发动机制造企业采用蓝光高精度三维扫描仪对叶片进行检测。在叶片制造过程中,通过蓝光三维扫描仪对叶片毛坯进行扫描,获取其初始三维数据,与设计模型进行对比分析,提前发现可能存在的尺寸偏差和缺陷,为后续的加工工艺调整提供依据。在叶片加工完成后,再次对叶片进行全尺寸扫描,检测叶片的型面偏差、叶缘轮廓以及叶根部位的尺寸精度等。通过与设计模型的精确比对,能够快速、准确地发现叶片的制造误差,如型面偏差超过 ±0.05mm、叶缘轮廓误差超过 ±0.03mm 等,及时进行修正和优化,确保叶片的质量和性能符合设计要求。经过高精度三维尺寸测量技术的严格把控,该企业生产的航空发动机叶片合格率从原来的 80% 提升至 95% 以上,大大提高了发动机的可靠性和使用寿命。
再看飞机机翼的测量案例,飞机机翼是飞机产生升力的关键部件,其结构复杂,尺寸庞大,对装配精度要求极高。在机翼的制造和装配过程中,某飞机制造公司运用三坐标测量机和激光跟踪仪对机翼的各个零部件进行精确测量和定位。在零部件制造阶段,三坐标测量机对机翼蒙皮、翼梁、肋板等零部件的尺寸和形状进行高精度测量,确保每个零部件的制造精度符合设计标准。在装配过程中,激光跟踪仪实时监测各个零部件的装配位置,通过精确测量和调整,保证机翼的整体装配精度,如机翼的扭转角度误差控制在 ±0.1° 以内,弦长尺寸误差控制在 ±1mm 以内。通过高精度三维尺寸测量技术的应用,有效提高了飞机机翼的装配质量和性能,确保了飞机的飞行安全和稳定性。
技术发展趋势展望
展望未来,高精度三维尺寸测量技术正朝着自动化、智能化以及与其他技术深度融合的方向大步迈进,展现出无限的发展潜力和广阔的应用前景。
在自动化方面,测量设备将具备更强大的自主测量能力。通过自动化测量,设备能够依据预设程序自动完成测量任务,显著减少人工干预,从而大幅提升测量效率和准确性。以工业生产线上的零部件检测为例,自动化测量设备可以在生产过程中实时对零部件进行测量,一旦发现尺寸偏差,立即发出警报并自动调整生产参数,实现生产过程的实时监控和质量控制,有效提高生产效率和产品质量。
智能化则是高精度三维尺寸测量技术发展的另一大趋势。随着人工智能技术的飞速发展,AI 将在数据处理和分析中发挥越来越重要的作用。测量设备能够利用 AI 算法对海量的测量数据进行快速、准确的分析,不仅可以自动识别测量数据中的异常值和错误,还能根据数据分析结果提供针对性的建议和解决方案。例如,在航空航天领域,通过 AI 对发动机叶片的测量数据进行分析,能够预测叶片的疲劳寿命和潜在故障,提前进行维护和更换,确保发动机的安全运行。
高精度三维尺寸测量技术与其他技术的融合也将成为未来发展的重要方向。在智能制造系统中,高精度三维尺寸测量技术将与物联网、大数据、云计算等技术深度融合,实现生产过程的全面数字化和智能化管理。通过与物联网技术结合,测量设备可以实时将测量数据上传至云端,实现数据的共享和远程监控;借助大数据分析技术,能够对大量的测量数据进行挖掘和分析,为生产决策提供有力支持;而云计算技术则为测量数据的存储和处理提供了强大的计算能力,确保数据处理的高效性和准确性。
高精度三维尺寸测量技术的发展将为各行业带来更多的创新和突破,推动制造业向智能化、数字化、高质量化方向发展,助力各行业在激烈的市场竞争中取得更大的优势。
总结与思考
高精度三维尺寸测量技术作为现代工业的 “智慧之眼”,以其无可替代的关键作用,成为推动各行业发展的核心力量。从汽车制造到航空航天,从电子设备到医疗器械,这项技术的应用范围广泛,为产品质量提升和生产效率提高提供了坚实保障。
在技术层面,接触式测量的三坐标测量机以其高精度、丰富的测量特征和高自动化程度,在精密制造领域独树一帜,然而,其对异形件、大型件和柔性材料测量的局限性,以及高昂的设备成本和严苛的环境要求,也限制了其在部分场景的应用。非接触式测量中的光栅三维扫描仪和激光三维扫描仪则凭借高精度、快速扫描、非接触无损测量等优势,在众多领域大显身手,尤其是在对表面质量要求高、易变形物体的测量中表现出色,但它们也面临着设备成本高、数据处理复杂等挑战。
通过实际应用案例,我们清晰地看到高精度三维尺寸测量技术在提升产品质量和生产效率方面的显著成效。在汽车制造行业,它有效降低了发动机废品率,提升了车身装配精度;在航空航天领域,大幅提高了发动机叶片合格率和飞机机翼装配质量,有力保障了飞行安全。
展望未来,自动化、智能化以及与其他技术的深度融合,将是高精度三维尺寸测量技术的主要发展方向。自动化测量将减少人工干预,提高测量效率和准确性;智能化分析将为生产决策提供有力支持;与物联网、大数据、云计算等技术的融合,将推动制造业向智能化、数字化、高质量化方向迈进。
高精度三维尺寸测量技术的发展对于推动工业制造迈向更高精度和智能化水平具有深远意义。各行业应高度重视这一技术的创新和应用,不断探索其在不同领域的更多可能性,为行业发展注入新的活力,共同开创工业制造的美好未来。