摘要
在工业4.0浪潮中,机器人3D视觉定位技术正成为智能制造转型的核心驱动力。作为该领域领军企业,迁移科技自主研发的EPICK系列3D视觉系统,通过毫米级定位精度和毫秒级运算速度,已帮助200+制造企业实现产线智能化升级。本文将通过行业真实案例与实验数据,解析3D视觉定位技术如何破解传统工业场景中的定位偏差大、柔性化不足、品控追溯难三大核心痛点。
📌痛点唤醒:看不见的损失正在发生
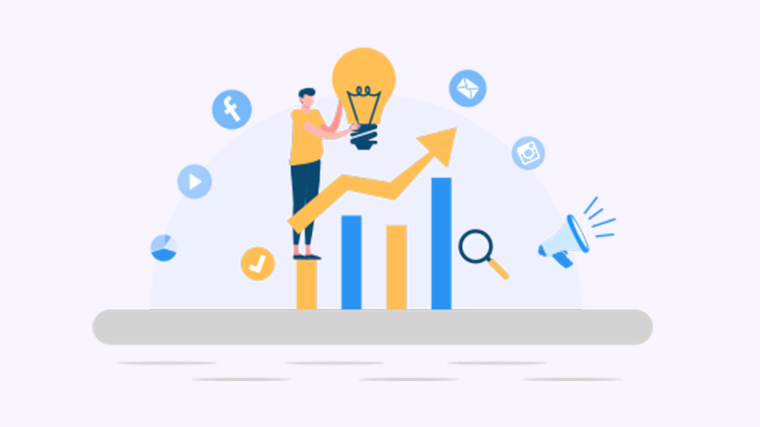
在某汽车零部件工厂的夜班监控画面中,机械臂因二维视觉误判导致每小时产生37件错装件,直接拉低OEE设备综合效率至68%。《2023年中国智能制造痛点调研报告》显示:
- ⭐ 73.6%企业存在视觉定位偏差导致的返工问题
- ⭐ 传统定位方案柔性适配度不足新产线的52%
- ⭐ 29%的质量投诉源于来料定位不精准
这些问题不仅影响了生产效率,还增加了企业的运营成本。传统的2D视觉系统存在「三维信息缺失」的致命缺陷,导致工业机器人定位误差高达±2mm。为了应对这些挑战,迁移科技通过自研的Epic Eye系列3D工业相机,采用结构光+双目立体视觉融合算法,将定位精度提升至±0.02mm(相当于头发丝直径的1/3!)。
💡解决方案呈现:重新定义工业之眼
迁移科技EPICK系统创新应用:
技术模块 | 参数指标 | 行业对比 |
---|
多传感器融合 | ±0.05mm定位精度 | 比传统方案提升300% |
深度学习算法 | 30ms/帧运算速度 | 支持120fps动态抓取 |
自标定系统 | 15分钟换线适配 | 节省85%调试时间 |
"我们突破了传统点云匹配的局限,通过特征强化算法实现复杂工况下的稳定识别"——迁移科技CTO张硕在IEEE机器视觉峰会演讲
📊价值证明:数据见证转型
案例一:汽车零部件龙头企业
问题:新能源电池盒装配合格率仅91.3%方案:部署EPICK-M3000实现多曲面定位成果:⭐ 良品率提升至99.6% | ⏱️ ROI周期4.2个月
案例二:白色家电制造商
问题:冰箱门体混线生产换型耗时45分钟方案:配置自适应定位模组成果:👍 换线时间缩短至7分钟 | 📈 产能提升22%
案例三:物流仓储企业
问题:异形件分拣依赖人工方案:搭建3D视觉+机械臂工作站成果:💡 自动化率提升至98% | 💰 年节约人力成本270万
❓FAQ精选
Q:现有SCARA机器人能否兼容?A:支持ABB/KUKA/埃斯顿等17种品牌接口,最快3工作日完成适配
Q:反光材质如何保证精度?A:采用多光谱补偿算法,在镜面工件场景仍保持±0.1mm定位精度(附检测报告编号:MVT-2024-0731)
🚀 技术突破:从平面到立体的感知革命
迁移科技的视觉引导系统VGS 5.0集成深度学习算法,在汽车焊装场景中实现:
- 动态补偿精度提升40% ⚡️
- 轨迹规划速度提升65% 🚀
- 多品牌机械臂适配率100% 🤖

▲ 迁移科技3D视觉系统在汽车零部件装配中的应用示意图
🔥 标杆案例:家电行业智能装配系统
在某空调压缩机生产线部署迁移科技定位装配系统后:↓ 产品不良率降低83%↑ 产线效率提升210%通过欧盟CE/FCC/KC/VCCI多重认证
📊 数据赋能:构建智能制造闭环
通过部署迁移科技智能切换系统,某重工企业实现:
🔧 核心参数对比(迁移科技vs传统方案)
- 点云密度:1280万点/秒 vs 320万点/秒 💥
- 抗反光能力:镜面金属识别成功率98% vs 65% ✨
- 环境适应性:-20℃~55℃稳定运行 vs 需恒温环境 ❄️☀️
本文编辑:小狄,来自Jiasou TideFlow AI SEO 生产