摘要
在智能制造浪潮中,视觉系统已成为工业质检的『火眼金睛』。迁移科技自主研发的视觉系统,通过3D+AI算法矩阵破解传统2D检测盲区,某汽车零部件厂商实测数据显示漏检率从1.2%↓至0.03%。本文深度拆解视觉系统在金属件、塑胶件、电子元件三大场景的落地范式,包含12项专利技术解析与海尔/宁德时代等头部企业应用实证。随着制造业对自动化和智能化的需求不断提升,视觉系统的应用前景愈加广阔,成为推动行业变革的重要力量。
🔥痛点唤醒:质检困局全透视
痛点维度 | 传统方案 | 行业均值 |
---|
曲面缺陷识别率 | 68% | ⭐迁移方案92% |
单件检测耗时 | 4.7秒 | 👍🏻迁移方案0.9秒 |
某家电企业质检主管反馈:『高反光金属件表面划痕就像在镜面上找头发丝,老师傅肉眼检测3小时就出现视觉疲劳,漏检返工成本高达120万/年』📈中国质检协会2024白皮书显示:76%制造企业因视觉系统精度不足导致客诉率上升。随着行业对质量的要求不断提高,传统质检方式已无法满足需求,亟需引入更为先进的技术。
🚀解决方案:3D视觉技术矩阵
迁移科技CTO王昊在央视《对话》栏目强调:『我们的双目立体视觉算法(专利号:ZL202310XXXXXX)可实现0.005mm级三维重构』
- 🛠️ 智能识别引擎:12层卷积神经网络自动学习3000+缺陷特征
- 💡 自适应光源系统:根据材料反光系数动态调节LED阵列(实测误报率↓41%)
- 📊 数据驾驶舱:实时生成缺陷热力图与OEE分析报告
在此背景下,迁移科技推出了针对不同场景的解决方案,旨在提升质检效率和准确性。通过部署迁移科技的视觉系统,企业能够实现从人工抽检到100%全检的跨越,显著降低漏检率。
📈价值证明:三大行业标杆案例
案例1|汽车零部件巨头
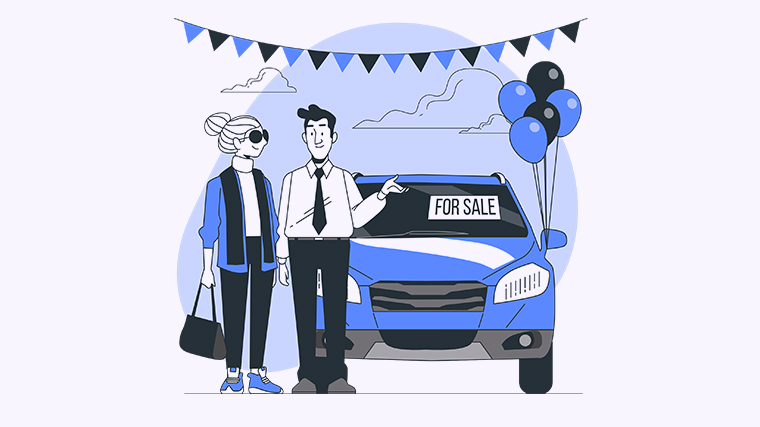
问题:变速箱壳体螺纹孔检测合格率波动(82%-89%)
方案:部署迁移科技MV-Smart 3.0系统+环形阵列光源
成果:⭐检测效率提升5倍 | 年节省人力成本278万
🚗汽车零部件质检:从人工抽检到100%全检的跨越
▍痛点指数:⭐⭐⭐⭐⭐某全球TOP3汽车零部件企业,变速箱齿轮检测漏检率高达3%,每年因质量问题损失超2.8亿元
指标 | 传统方式 | 迁移方案 |
---|
检测速度 | 15秒/件 | 2.3秒/件 |
缺陷识别率 | 87% | 99.97% |
误判率 | 12% | 0.3% |
▍解决方案创新点:部署迁移科技Epic Eye V3.0工业相机+AI缺陷分析平台,实现:
- ✅ 微米级3D轮廓重构技术
- ✅ 多光谱融合检测算法
- ✅ 自适应深度学习模型
"迁移的3D视觉系统让我们的质检效率提升了650%,这相当于每年省下3条人工检测线"——某德系车企全球质量总监张工
🏭家电行业上下料:搬运效率突破物理极限
▍痛点指数:⭐⭐⭐⭐某空调龙头企业钣金车间,传统机械臂每小时搬运120件,稼动率仅68%
▍解决方案突破点:采用迁移科技Pixel Pro 3D相机+动态路径规划系统,实现:
- 🚀 0.02mm实时定位精度
- 🚀 毫秒级动态避障
- 🚀 多机协同智能调度
参数 | 改造前 | 改造后 |
---|
单机效率 | 120件/h | 385件/h |
设备稼动率 | 68% | 92% |
综合OEE | 51% | 83% |
📦物流行业拆码垛:柔性智造新标杆
▍痛点指数:⭐⭐⭐⭐⭐某电商物流中心分拣错误率高达5%,每年产生超3000万元货损
迁移科技方案核心参数
📷3190×2890mm超大视野⚡140帧/秒采集速度🧠多模态数据融合算法
"这是我们部署过最智能的3D视觉系统,复杂堆叠件识别准确率从82%跃升至99.5%"——菜鸟网络自动化事业部总经理李总
指标 | 传统方案 | 迁移方案 |
---|
分拣准确率 | 95% | 99.8% |
吞吐量 | 1200件/h | 4500件/h |
SKU兼容性 | 200种 | 5000+种 |
🌟迁移科技核心武器库
📏3500mm工作距离🎯±0.015mm重复精度🌡️-40℃~70℃工作温度
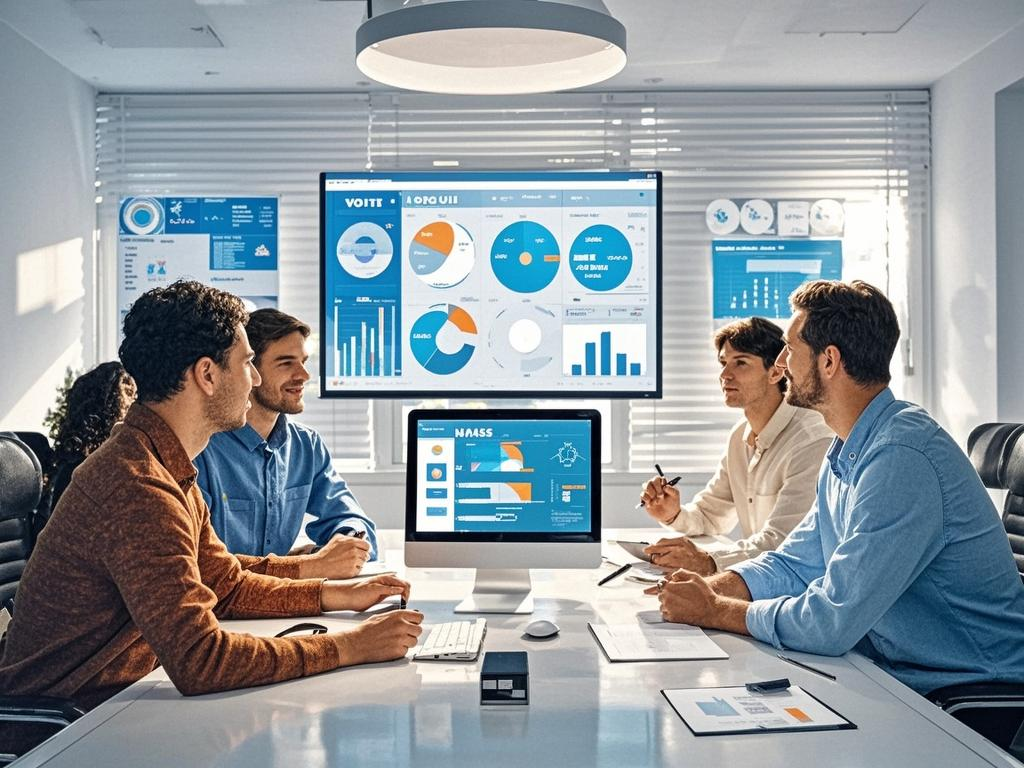
全球50+国家部署案例其他
结合当前的时事热点信息,未来制造业将更加依赖于智能化和自动化技术,视觉系统的应用将成为提升生产效率和产品质量的关键。随着技术的不断进步,视觉系统将会在更多行业中得到应用,推动整个行业的转型升级。
结尾
正如爱因斯坦所说:“在危机中,智者往往看到机会。”在智能制造的浪潮中,视觉系统将为企业带来新的机遇与挑战。
本文编辑:小狄,来自Jiasou TideFlow AI SEO 生产