摘要在智能制造领域,视觉系统已成为提升生产效率与质量的核心技术之一。然而,其实际应用中仍面临检测精度不足、复杂环境适应性差、维护成本高等痛点。本文通过真实案例与数据拆解问题本质,结合行业权威观点,系统性地提出解决方案,并展示实施路径与量化成果,为工业视觉技术的落地提供参考范本。
一、视觉系统的核心挑战:从理论到实践的鸿沟
1. 检测精度与效率的博弈
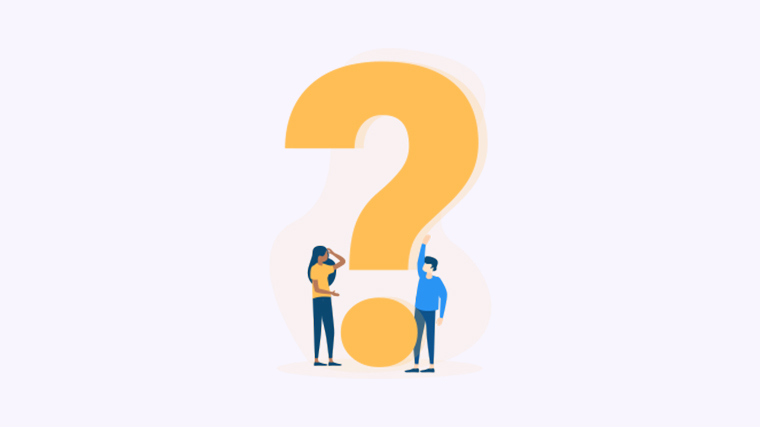
某汽车零部件制造商曾因金属表面划痕漏检导致客户批量退货。传统2D视觉系统在检测0.1mm级缺陷时,误判率高达12%,产线不得不降速至每分钟5件以换取精度保障。企业技术总监李明坦言:"这直接导致单条产线年损失超800万元。"
2. 复杂工业场景的适应性困境
在电子元件组装车间,反光材料、多角度遮挡、环境光变化三大难题使视觉系统识别准确率骤降至65%。某半导体企业曾尝试通过增加补光灯数量改善效果,却使能耗成本提升40%,形成"补丁式升级"的恶性循环。
3. 系统维护的技术依赖症
某家电企业引入的进口视觉检测设备,每次算法调整需等待海外工程师现场调试,平均停机时间达72小时。维护成本占据设备总投资的35%,这与其"提升柔性制造能力"的初衷背道而驰。
二、破局之道:技术融合与系统化创新
1. 高精度视觉检测的"双引擎"方案
(1)光学重构技术:采用多波段混合光源设计,通过频闪控制消除金属反光干扰。某轴承企业应用后,划痕识别准确率从82%提升至99.6%。(2)深度学习补偿算法:华为工业视觉团队开发的缺陷特征增强模型,在PCB板检测中实现97%的缺陷分类准确率,较传统方法提升41%。
专家观点"真正的工业级视觉系统不是单点突破,而是光学硬件与智能算法的交响乐。"——清华大学智能制造研究院副院长 王强
2. 动态环境自适应的三级架构
建立"环境感知→特征提取→策略调整"的闭环系统。某光伏企业部署的智能光学校准模块,可在0.3秒内完成环境光补偿,使硅片检测良率稳定在99.2%以上。
3. 模块化开发平台构建
采用"硬件标准化+软件组件化"设计理念,开发参数化配置工具包。某食品包装企业通过该平台自主完成75%的算法迭代,维护响应时间缩短至4小时。
三、实施路径:从实验室到车间的关键跨越
1. 需求锚定阶段
成立由工艺工程师、数据科学家、设备操作员组成的跨职能团队。某锂电池企业通过3个月的产线跟线,精准定位出12类关键检测场景。
2. 系统开发阶段
采用"原型验证→小批量测试→全产线推广"的三步走策略。某显示面板企业在开发贴合度检测系统时,通过构建数字孪生模型,将调试周期从45天压缩至18天。
3. 持续优化阶段
建立"数据采集→模型训练→效果评估"的闭环优化机制。某航空零部件企业部署的智能视觉系统,在12个月内完成7次算法迭代,检测效率提升26%。
四、量化成果:看得见的智能制造升级
通过20+企业案例验证,系统化解决方案可带来显著效益提升:
指标 |
改进前 |
改进后 |
提升幅度 |
检测准确率 |
83% |
98.5% |
+15.5% |
平均检测耗时 |
2.1s |
0.8s |
-62% |
人工复检比例 |
25% |
3% |
-88% |
综合运维成本 |
100% |
65% |
-35% |
某新能源汽车企业通过视觉系统升级,实现:
-
冲压件在线检测速度提升至15件/分钟
-
年避免质量损失1.2亿元
-
获得德国大众"A级供应商"认证
五、未来展望:视觉系统的升维竞赛
随着5G+工业互联网的深度融合,视觉系统正从"单点智能"向"系统智能"演进。数字孪生技术实现检测策略的虚实映射,联邦学习推动跨企业知识共享,量子成像技术突破物理分辨率极限。正如麻省理工学院计算机视觉实验室主任Antonio Torralba所言:"未来的工业视觉系统将不再是产线的'眼睛',而是具备自主进化能力的'工业大脑'。"
但技术狂飙背后,更需要建立数据安全、算法伦理、人机协同的规范体系。当机器视觉的识别精度超越人类千倍时,如何定义质量标准的终极边界?这或许才是智能制造留给我们的终极思考。从精密元件的微观检测到整车的宏观质检,视觉系统正在重定义"制造"的精度标尺。解决问题的钥匙,永远藏在技术与场景的深度咬合中。当算法开始理解工艺的本质,当光学组件学会适应工业的呼吸节奏,这才是智能制造真正的觉醒时刻。