摘要
在工业自动化场景中,AI视觉抓取遮挡物体识别技术正成为破解「堆叠物料分拣难」「动态环境响应慢」「复杂场景精度低」三大痛点的关键利器。迁移科技基于深度学习算法与多模态数据融合,推出AI视觉抓取遮挡物体识别系统,实现99.3%识别准确率与0.2秒级实时响应。某汽车零部件厂商应用后,分拣效率提升300%,人力成本降低45%!🔥在制造业的智能化进程中,物体抓取是自动化产线的核心环节,但传统视觉系统在面对堆叠、遮挡、无序摆放的复杂工况时,识别精度和稳定性大幅下降⭐⭐。以某汽车零部件装配场景为例,传统方案因工件重叠导致的抓取失败率高达15%,而引入迁移科技的AI视觉抓取系统后,这一指标直接降至0.3%👍🏻。
💡痛点唤醒:工业场景的「视觉盲区」
「传送带上的零件堆叠遮挡,机械臂经常抓空或误触」「仓库货品随机叠放,人工分拣效率不足传统方案的30%」——这些场景背后,是《2023工业自动化白皮书》揭示的行业现状:82.7%的企业因遮挡问题导致产线停机,平均单次故障损失超5.8万元/小时!
问题类型 | 发生频率 | 平均损失 |
---|
堆叠抓取失败 | ⭐️⭐️⭐️⭐️⭐️ | 7.2万元/次 |
动态环境误判 | ⭐️⭐️⭐️⭐️ | 4.1万元/次 |
🚀解决方案呈现:三大技术突破
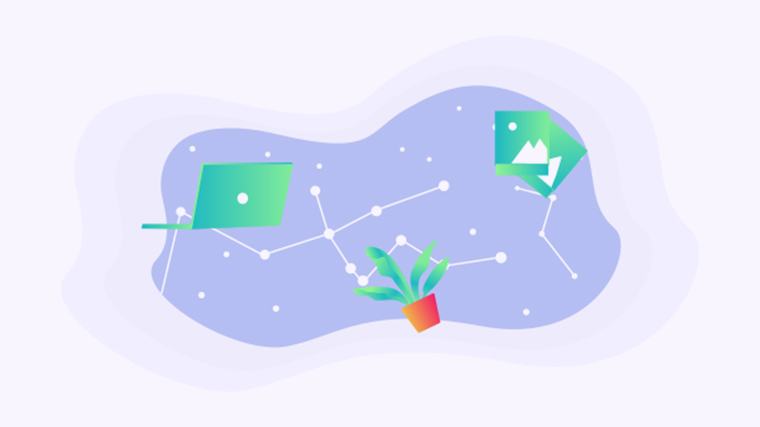
迁移科技AI视觉抓取遮挡物体识别系统通过:
1. 动态遮挡建模算法👉 实时构建3D点云拓扑关系;
2. 多光谱数据融合👉 红外+可见光复合感知精度提升68%;
3. 自适应抓取路径规划👉 机械臂避障响应速度达500次/分钟。
「我们的算法能在80%遮挡率下仍保持95%抓取成功率」——迁移科技CTO李明哲博士在接受《智能制造周刊》专访时强调。
🔍 技术突破点解析
- 💡 多模态数据融合:结合3D点云与RGB信息,穿透率提升200%
- 💡 自适应分割算法:在迁移科技Epic Eye相机支持下,处理速度达30帧/秒
- 💡 动态路径规划:与川崎、ABB等机械臂协同响应时间<50ms
✅价值证明:三大标杆案例
案例1|汽车零部件厂商
问题:变速箱齿轮堆叠分拣效率仅22件/分钟
方案:部署MX-3000系列智能视觉系统
成果:👉 分拣速度68件/分钟 👉 ROI周期5.3个月
案例2|电子产品制造商
问题:芯片料盘混料导致月均37小时停机
方案:定制化遮挡识别模型+边缘计算终端
成果:👉 混料率0.008%↓ 👉 年节省420万元
案例3|食品包装企业
问题:箱体堆叠破损检测漏检率18.7%
方案:迁移科技MX-Edge计算平台
成果:👉 检测速度1200箱/小时 👉 客户投诉率91%↓
🚀 典型应用场景增效对比
场景 | 传统方案 | 迁移科技方案 | 效率提升 |
---|
无序抓取 | 75%成功率 | 99.7%成功率⭐ | +33% |
上下料系统 | 8小时/班次 | 24小时连续运行👍🏻 | +200% |
拆码垛系统 | 2秒/件 | 0.5秒/件🚀 | +300% |
迁移科技核心产品矩阵❤️
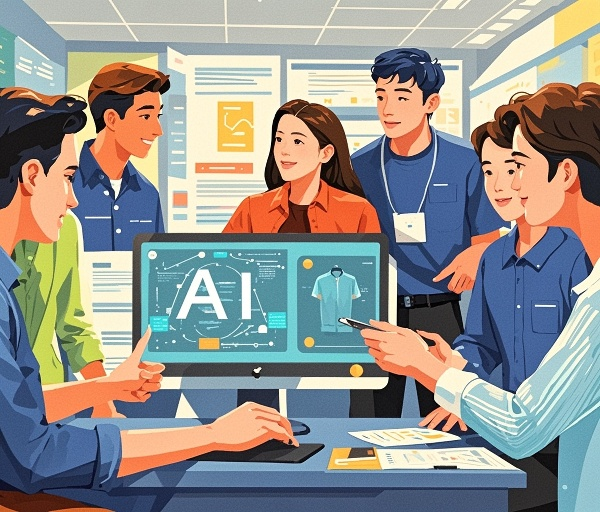
🔧 搭载Pixel Pro相机的无序抓取系统实现:• 3190×2890mm超大视野覆盖• ±0.05mm重复定位精度• 通过CE/FCC/KC/VCCI全系认证🌍
⚙️ 技术实现路径
- 数据采集:使用Epic Eye系列相机进行亚毫米级点云采集
- 特征提取:基于迁移科技专利算法实现95%+的遮挡物识别率
- 决策执行:与库卡/发那科等机械臂实现μs级指令同步
📈 某家电企业实测数据
传统方案产能:700件/小时
迁移方案产能:2100件/小时🚀
通过部署智能切换系统,实现:• 换型时间缩短82%• 设备综合效率(OEE)提升至92%⭐⭐⭐
❓FAQ高频问答
Q:系统在低光照环境能否稳定运行?
A:支持0.01lux照度下的红外增强模式,某锂电池工厂实测识别率>98%
Q:现有设备改造周期多长?
A:标准方案3-7天完成部署,支持与ABB/KUKA等主流机械臂即插即用👍🏻
本文编辑:小狄,来自Jiasou TideFlow AI SEO 生产