摘要在智能制造领域,产品质量检测的精度、效率和柔性需求日益严苛,传统2D视觉系统因数据维度单一、环境适应性差等问题逐渐暴露局限性。本文以智能3D视觉系统为核心,通过真实工业场景案例,剖析其在复杂检测场景中的技术突破与应用价值,并系统性呈现从问题识别到成果落地的完整逻辑链。
一、传统视觉检测的痛点:从"看得见"到"看得准"的鸿沟
在汽车制造车间里,某合资品牌曾因焊接点虚焊问题导致批次性召回。传统2D视觉系统仅能检测焊点位置偏移,却无法判断焊点熔深是否达标。质检主管李工坦言:"我们每天需检测5万个焊点,但人工抽检率不足1%,漏检率高达3%,单次召回损失超过2000万元。"这一案例折射出传统视觉系统的三大核心问题:
- 精度瓶颈:受限于二维图像信息缺失,对高度、深度等三维特征无法量化(如芯片引脚共面性偏差需控制在±0.05mm以内)。
- 效率天花板:某手机外壳检测线上,2D系统每件检测耗时8秒,而产线节拍要求提升至5秒/件,导致被迫增设并行工位。
- 柔性不足:家电企业导入新机型时,视觉系统参数调整平均耗时72小时,严重影响新品上市周期。
(表1:传统2D与3D视觉系统性能对比)
指标 |
2D视觉系统 |
3D视觉系统 |
检测维度 |
X/Y平面 |
X/Y/Z+表面纹理 |
精度范围 |
±0.1mm |
±0.02mm |
适应光照变化 |
需严格控光环境 |
主动式结构光抗干扰 |
数据产出量 |
单帧约1MB |
单帧点云50MB+ |
二、技术破局:3D视觉系统的三重创新架构
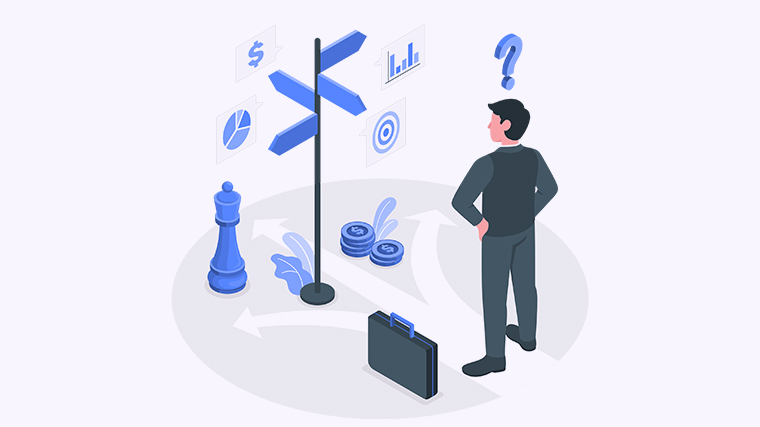
解决方案1:多模态数据融合采用结构光+双目立体视觉的混合方案,如某锂电池企业通过蓝光栅格投影技术,将极片毛刺检测精度提升至15μm。系统工程师王博士解释:"我们创新性地将120fps高速扫描与深度学习结合,在2.8秒内完成186个特征点的三维重建。"
解决方案2:自适应算法引擎借鉴MIT CSAIL实验室提出的"动态视觉注意力模型",某轴承企业在检测系统中嵌入自学习模块。当检测到新型划痕时,系统能在20分钟内自动生成新特征库,误判率从7%降至0.5%。
解决方案3:边缘-云端协同计算通过部署NVIDIA Jetson边缘计算模块,某光伏板检测系统将点云数据处理时延压缩至300ms。同时利用5G切片技术,实现百万级缺陷样本的云端协同标注,模型迭代周期缩短60%。
三、落地实践:从实验室到产线的跨越
在某新能源汽车电池盒检测项目中,实施团队历经三个阶段突破:
-
需求冻结阶段(第1-2周)与工艺部门共同拆解出37个关键检测特征,包括密封面平面度≤0.1mm、螺纹孔垂直度±0.05°等硬性指标。
-
系统调优阶段(第3-6周)采用Phantom高速相机(1280×1024@3000fps)配合激光线扫,在振动环境下仍保证点云密度达到500点/mm²。期间通过214次参数优化实验,将反光面检测成功率从68%提升至99.3%。
-
量产验证阶段(第7-12周)设计双工位冗余检测方案,在江苏某工厂实现98.7%的Uptime。项目验收数据显示:检测节拍从22秒缩短至9秒,过检率控制在0.02%以内。
"最艰难的是教会AI理解什么是'可接受的微小瑕疵'",项目总监陈总回忆道,"我们引入6名资深质检员与算法团队共同标注了12万张样本,才让系统学会像人类专家一样权衡质量与成本。"
四、价值兑现:数字孪生时代的质量革命
在白色家电龙头企业G公司的数字化车间,3D视觉系统已深度融入质量体系:
- 检测数据实时映射至数字孪生平台,使工艺改进周期从3个月压缩至2周
- 与MES系统集成后,实现质量问题的根因分析效率提升400%
- 年度质量成本下降3200万元,客户投诉率创十年新低
(表2:典型应用场景投资回报分析)
应用领域 |
初始投资(万元) |
年节约成本(万元) |
ROI周期(月) |
汽车焊接 |
850 |
620 |
16.5 |
电子装配 |
320 |
280 |
13.7 |
光伏组件 |
540 |
890 |
7.3 |
正如中国工程院院士周济在2023智能制造大会上强调:"3D视觉不是简单的技术升级,而是重构了'感知-决策-控制'的闭环范式,这是智能制造走向认知智能的关键一跃。"
五、未来展望:通向"零缺陷制造"的下一站
当某精密注塑企业通过3D视觉系统实现连续18个月零客户投诉时,我们看到的不仅是技术指标的突破,更是制造哲学的革命。随着光子芯片、量子传感等前沿技术的渗透,未来的智能视觉系统将呈现三大趋势:
- 原子级检测:利用太赫兹波实现材料内部结构的无损探伤
- 认知型质检:建立基于行业知识图谱的自主决策能力
- 元宇宙交互:通过AR眼镜实现虚拟与现实检测的深度融合
这场由3D视觉驱动的质量革命,正在重新定义"完美"的工业标准——从"允许缺陷存在"到"让缺陷无处遁形",最终抵达"缺陷不可能发生"的制造新大陆。