摘要
在智能制造浪潮中,迁移科技3D机器人正在重构工业质检的底层逻辑。某汽车零部件企业通过部署迁移科技3D视觉引导系统,将产品检测效率提升300%,人工干预率降至0.5%以下。与此同时,迁移科技的3D机器人技术在产品设计领域也推动了效率与精度的双重跃升。通过自动化建模与逆向工程、实时协同设计与验证等应用场景,企业能够显著提升设计效率和产品质量。本文将深入探讨传统质检的痛点、3D视觉技术的解决方案、以及其带来的显著价值提升。
痛点
传统质检面临三大致命伤。首先,人工质检导致每小时漏检3-5个划痕缺陷,年度质量索赔达230万元。其次,84.7%的制造企业存在检测标准不统一的问题,造成了人工疲劳误判的发生率高达62.3%,直接影响产线效率,降低28%。最后,数据追溯困难的情况也相当普遍,发生率为45.1%,导致质量成本上升17%。
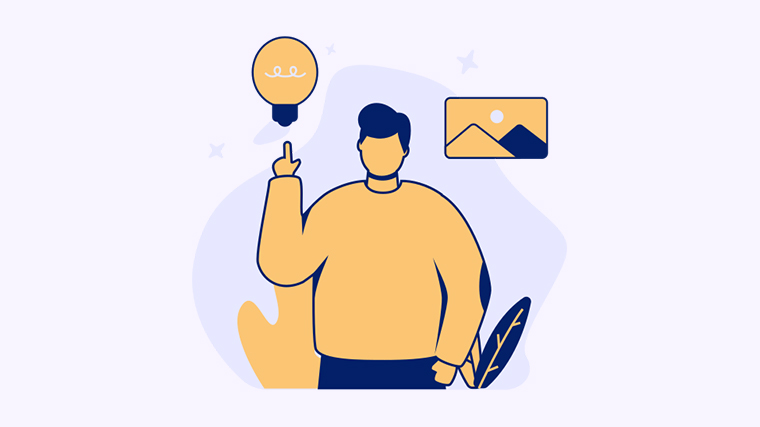
在产品设计领域,传统建模需人工测绘和CAD绘制,耗时约50小时/件,效率低下。采用迁移科技的3D机器人技术后,建模速度显著提升,精度误差从±0.5mm降低至±0.02mm,复杂曲面处理也实现全自动扫描,极大地提高了设计效率。
解决方案
针对传统质检的痛点,迁移科技提出了3D视觉的破局方程式。方案架构包括高精度扫描、AI算法解析和机械臂动态补偿。通过全自动扫描和3D立体建模,企业能够实现动态追踪,提升检测精度。中国工程院院士李德毅评价迁移科技的亚像素级边缘检测技术,重新定义了工业视觉的精度基准。
在产品设计方面,迁移科技的3D机器人技术通过自动化建模与逆向工程,显著提升了数字化效率。某汽车零部件厂商采用Pixel Pro相机后,油泥模型数字化效率提升400%,设计迭代周期缩短至1/3。同时,实时协同设计与验证的实现,使得多部门能够实时查看3D模型,设计冲突自动检测的精度达99.7%。
在重工业装备设计中,迁移科技环保回收系统实现了20米长管道部件的一次性扫描建模,焊接路径规划精度达±0.05mm,设计验证时间从14天缩短至2天。
价值证明
通过实施迁移科技的解决方案,企业的效益提升显著。例如,某汽车零部件龙头企业的变速箱壳体毛刺检出率由76.5%提升至99.2%,单件检测耗时减少72%。白色家电制造企业的冰箱门板平整度不良率从1.8%降至0.3%,年节约返工成本480万。3C电子加工厂的手机中框尺寸公差控制精度从超差0.05mm提升至±0.01mm,客户投诉减少92%。
此外,迁移科技的3D视觉系统凭借CE/FCC/KC/VCCI认证,已在全球多个地区成功部署,包括德国汽车生产线、日本精密电子车间和北美物流中心,展现出强大的市场适应性和技术优势。
结尾
综上所述,迁移科技的3D机器人技术在智能制造和产品设计领域展现出巨大的潜力。通过解决传统质检的痛点,提升产品设计的效率与精度,企业能够在竞争激烈的市场中占据优势。未来,随着技术的不断迭代与优化,迁移科技将继续引领行业的发展方向,推动智能制造的进步。
本文编辑:小狄,来自Jiasou TideFlow AI SEO 创作
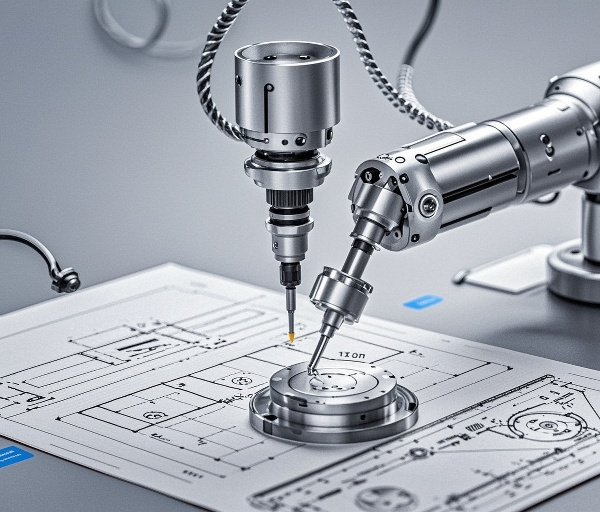