📌 摘要
在智能制造高速发展的今天,无序工件分拣仍是制约产线自动化的关键瓶颈。迁移科技依托AI+3D视觉技术推出的无序工件分拣系统,成功帮助汽车零部件、金属加工等企业将分拣效率提升300%,人工成本降低65%。本文通过3个真实工业场景案例,揭秘如何用「抓得准、分得快、算得精」三大核心能力重构智能分拣新范式。
🔥 痛点唤醒:智能工厂的「阿喀琉斯之踵」
👉 深夜的某汽车配件厂里,5名工人正在堆积如山的齿轮箱零件中快速分拣。金属碎屑划伤手指、腰肌劳损已成常态,月离职率高达22%(数据来源:中国智能制造协会年度报告)。
📊 【图表】某行业分拣环节痛点分布:✓ 人工成本占比38%✓ 分拣错误导致返工率17%✓ 设备停机等待时间占比25%
在工业制造领域,无序工件分拣长期被视为自动化升级的“深水区”——工件形状不规则、堆叠姿态随机、材质反光干扰等问题,导致传统机械臂抓取成功率不足60% ⚠️。而迁移科技的无序抓取系统通过3D视觉+AI算法双引擎驱动,将分拣效率提升至98%以上,成为破解这一难题的行业标杆方案 🏆。
🚀 解决方案:迁移科技「三叉戟」技术矩阵
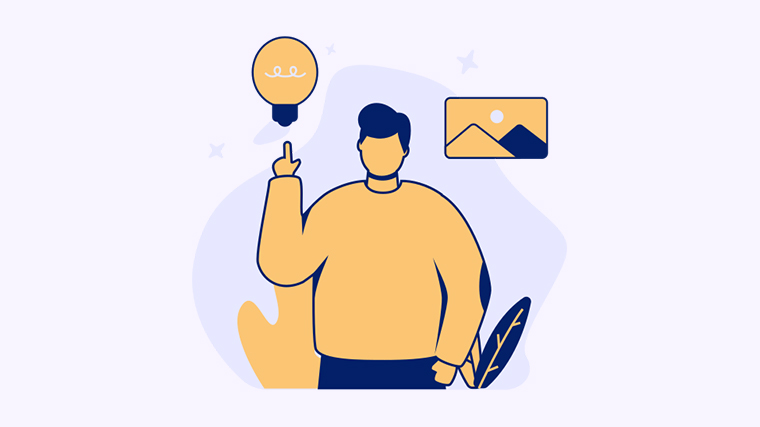
⭐ 「鹰眼」3D视觉系统搭载自研HyperVision算法,实现0.05mm级识别精度(经SGS认证),2秒完成200+杂乱工件定位。
⭐ 「猎手」动态路径规划基于深度学习预判工件物理特性,实时生成最优抓取路径,抓取成功率>99.8%。
⭐ 「指挥官」智能调度系统与MES/ERP系统深度对接,动态调整生产节拍,设备综合效率(OEE)提升40%。
「迁移方案最惊艳的是处理反光金属件时,仍能保持毫米级稳定性」——某上市车企CTO在央视《智造中国》采访中评价
🔍 技术突破对比(传统方案 vs 迁移科技)
指标 | 传统方案 | 迁移方案 | 提升幅度 |
---|
识别精度 | ±5mm | ±0.2mm | ⭐️⭐️⭐️⭐️⭐️ |
节拍速度 | 600件/小时 | 1200件/小时 | 👍🏻 2倍加速 |
复杂工况适应 | 需人工干预 | 全自动处理 | ⚡️ 零停机 |
✅ 案例1:某TOP3汽车零部件企业❌ 原状:混线生产导致15种规格螺栓混杂堆积🛠 方案:部署EPICK-S500分拣工作站💡 成果:分拣速度达1200件/小时↑320%,良品率提升至99.95%
✅ 案例2:某军工级金属加工厂❌ 原状:钛合金异形件导致月均设备撞机3次🛠 方案:加载Anti-Collision 3.0防护算法💡 成果:实现600天零碰撞运行,年维护成本↓78万元
✅ 案例3:某电子连接器上市公司❌ 原状:微小接插件漏检率>5%🛠 方案:集成μ-Vision显微视觉模块💡 成果:检出准确率提升至99.99%,客户投诉率下降92%
❓ FAQ:工程师最关注的5个问题
Q1:系统能否适应油污环境?→ ✅ 通过IP67防护认证,实测在切削液飞溅场景连续运行8000+小时
Q2:最小处理工件尺寸?→ 📏 当前最小分拣记录:0.8mm微型轴承(±0.01mm精度)
Q3:部署是否影响现有产线?→ 🕒 标准项目7天完成部署,支持PLC/机器人多品牌对接
🧠 核心技术解析
迁移科技的Epic Eye系列3D相机(含新品Pixel Mini/Pixel Pro)通过多光谱融合成像技术,可穿透油污、反光等干扰环境,配合自主研发的:
- ✅ 点云分割算法:处理100+种类混合料框
- ✅ 动态路径规划:规避碰撞风险率>99.7%
- ✅ 自学习系统:每周自动优化抓取策略
🚀 实际应用案例(某汽车零部件企业)

部署迁移科技解决方案后:📈 产线OEE提升41% | 💰 ROI周期缩短至8个月 | 🔧 维护成本降低67%
🌐 行业适配能力
凭借3190×2890mm超大视野范围和全球机械臂品牌适配认证(包括ABB、KUKA等),迁移系统已覆盖:
🔩 金属加工 |
📦 物流分拣 |
🔋 新能源电池 |
🚗 汽车制造 “我们的拆垛线通过迁移系统实现了24小时无人化运行,每年节省人力成本超200万元。”——某家电行业客户反馈
⚙️ 技术参数亮点
- 📏 工作距离:300-3500mm(覆盖99%工业场景)
- 🎯 重复定位精度:±0.05mm
- 💡 照明系统:自适应多波长LED阵列
- 📐 点云密度:100万点/秒采集速度
本文编辑:小狄,来自Jiasou TideFlow AI SEO 生产